At last: Wide-ranging uses of AI will be possible
Firm up your company for the future. Listen in and join in the conversation at Let’s Talk Science, the monthly EMO Hannover 2023 online seminar at 8.30 h on August 31, 2022.
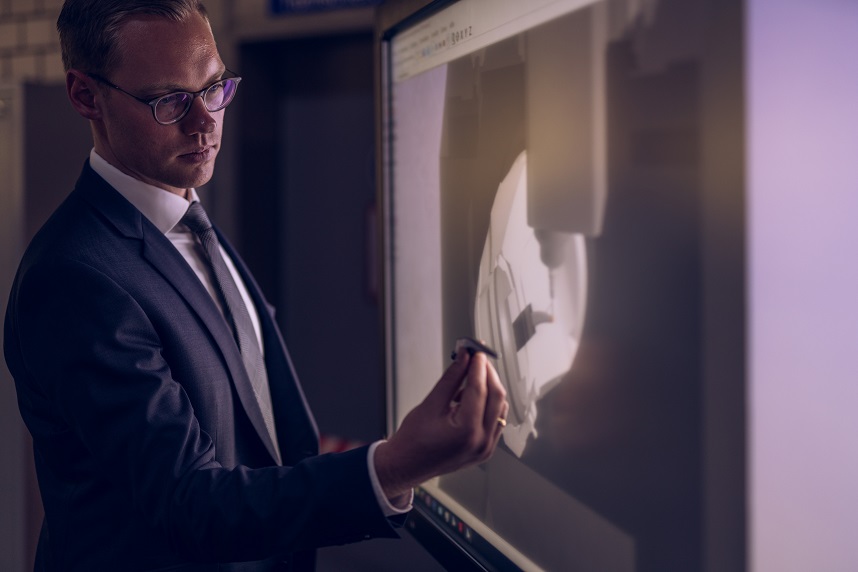
Artificial intelligence (AI) is a buzzword that is to be heard everywhere these days, though the reality behind it still isn’t impacting on everyday practice. The reason being that the complexly computed AI models for specific processes are so inflexible. If a process changes, with different materials being used, for instance, or because of tool wear, the model is unable to adapt. This is something researchers from Hannover now want to change, opening out AI for wide-ranging applications.
To this end, they make use of digital twins, that is, a precisely mapped digital image of a process. There is a great deal of technical and economic potential in such simulations, for they can be of assistance in the early recognition and compensation of deviations in quality. “Until now, however, AI models have been unable to respond to changing process conditions. They had to be retrained, and were thereby naturally a huge drain on time, expertise, and money,” explains Marcel Wichmann, who will show in the Let’s Talk Science online seminar at 8.30 h on August 31, 2022 how small and medium-sized enterprises will be increasingly able to benefit from AI in future. Wichmann is Head of the Production Systems Department of the Institute of Production Engineering and Machine Tools at the Leibniz University Hannover.
Such learning AI models facilitate a so-called adaptive process control, in other words, ongoing adaptation of a process to changing conditions such as the occurrence of tool wear or errors during processing.
Wichmann demonstrates the use of digital twins based on concrete examples. In aerospace engineering, he highlights the example of an application for the regeneration of turbine blades. This application makes it possible to predict the outcome for a particular workpiece and to modify the process if necessary. This, in turn, improves the quality and safety of the component.
A further example demonstrates optimization in the grinding of tools. The forecasts of the virtual tool twin are adjusted continuously on the basis of data feedback, and the process is constantly optimized. In practice, this results in fewer faulty workpieces and shorter run-in processes. The Hannover team also have the ambition of facilitating the imaging of entire production processes from the manufacturing and use of a component all the way to its quality control. “Last but not least, our simulations will improve the productivity of the processes,” Wichmann emphasizes.
“Quite apart from that, in these times of shortages in skilled staff, we are giving companies the opportunity of creating a team with many virtually supported assistants who have access to the experience of older members of staff, and all of this in a group with an experienced employee and a number of assistants.”
Firm up your company for the future. Listen in and join in the conversation at Let’s Talk Science, the monthly EMO Hannover 2023 online seminar at 8.30 h on August 31, 2022.
Downloads
Dokumente