Developing tools with artificial intelligence
In the Priority Program (SPP) 2422 “Data-driven modelling in forming technology”, the Institute of Forming Technology and Machines (IFUM) at Leibniz Universität Hannover, together with the Institute of Industrial Manufacturing and Factory Operation (IFF) at the University of Stuttgart and the Fraunhofer Institute for Manufacturing Engineering and Automation (IPA), is investigating the influence of process fluctuations in closed-die forging processes on component quality.
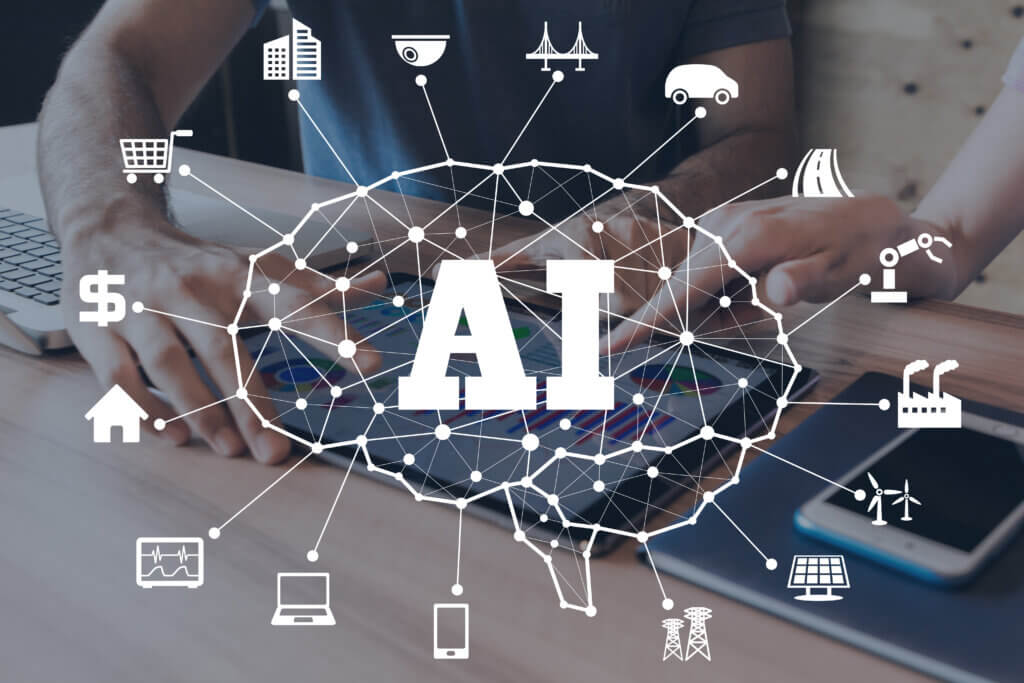
In the Priority Program (SPP) 2422 “Data-driven modelling in forming technology”, the Institute of Forming Technology and Machines (IFUM) at Leibniz Universität Hannover, together with the Institute of Industrial Manufacturing and Factory Operation (IFF) at the University of Stuttgart and the Fraunhofer Institute for Manufacturing Engineering and Automation (IPA), is investigating the influence of process fluctuations in closed-die forging processes on component quality.
Many complex interactions occur in hot forging that cannot yet be fully explained. Scientific studies have shown that these processes can lead to considerable fluctuations in the service life and causes of failure of the tools used. Forged components are therefore often produced with a considerable surplus of material in the form of a burr in order to obtain a defect-free finished component after deburring and machining. However, this process stabilization through flash forming increases the material and energy requirements, which has a negative impact on the economic efficiency and CO2 footprint of the process.
The research project aims to identify and quantify unknown interactions by digitizing a multi-stage series forging process. For this purpose, special data-based models are used to uncover previously unknown correlations and process fluctuations. Explainable AI will not only be used to make precise predictions, but also to make the underlying decisions comprehensible and interpretable. Based on these data models, adapted designs of the die surfaces are to be developed in order to make future process generations more robust against process fluctuations. This should make it possible to reduce safety factors such as flash or oversizes without reducing the good part window.
By using Explainable AI, the identified interactions can be converted into domain knowledge and used for the design of new processes or tool geometries. This is particularly important in view of the current shortage of skilled workers.
This innovative approach promises more efficient and sustainable production in the drop forging industry, which brings both economic and ecological benefits.
Contact
Eduard Ortlieb
For further information, please contact Eduard Ortlieb from the Institute of Forming Technology and Machines (IFUM) at Leibniz Universität Hannover (LUH),
Phone +49 511 762-2161,
e-mail ortlieb@ifum.uni-hannover.de