Lightweight construction is key technology for global sustainability
Intelligent lightweight solutions are increasingly gaining ground in machine tool construction. The main focuses are on new geometries and materials as well as simulation and 3D printing. Exhibitors at EMO Hannover will be showing how products can be designed and manufactured to meet lightweight and sustainability criteria based on a range of examples.
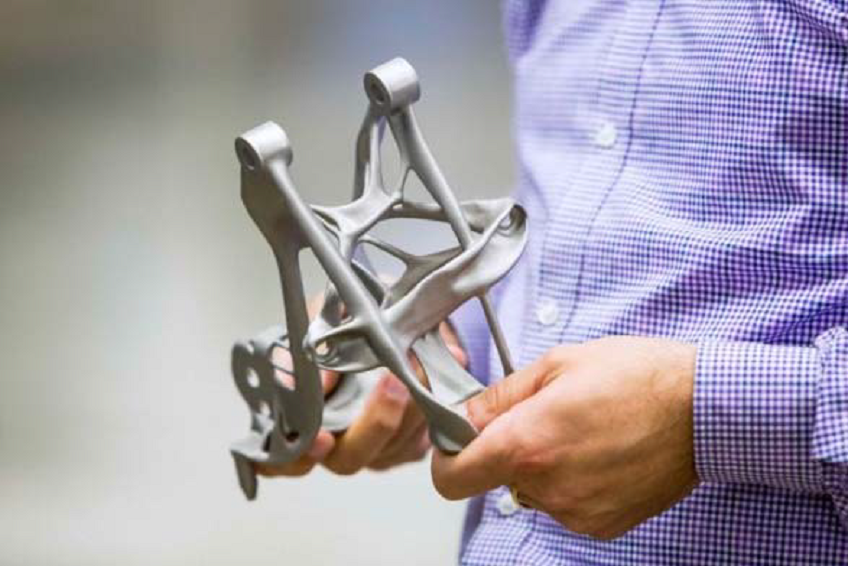
Lightweight construction is a key element in any attempt to achieve more sustainable production. It begins long before the manufacturing process itself and runs through the entire value chain – from the raw material to the finished component. Companies therefore need to address this issue at a correspondingly early stage. “Sustainability is a key factor in our company,” says Steffen Krause, Technical Sales Manager at software developer Autodesk. “Our mission is to automate customers’ design drafts and develop processes which allow them to speed up and improve the design process – while reducing the impact on the environment. With Autodesk technology, manufacturers can improve their performance and help make the world a better place by increasing material and energy efficiency in their design and manufacturing processes.”
Sustainability and a commitment to environmental protection are a matter of course for (and an important part of the corporate identity of) Hainbuch, the Marbach-based manufacturer of workpiece clamping solutions. An “energy policy” has been anchored in the company’s environmental guidelines since 2016. “This helps us reduce emissions and waste, increase energy efficiency, guarantee the economical use of resources and reduce the emissions of hazardous substances. This is because we want to develop and produce products which are not only high-quality, but also environmentally friendly and sustainable,” explains Stefan Nitsche, Head of Product Management at Hainbuch.
Lightweight construction is an essential prerequisite for material efficiency
3D Micro Print GmbH in Chemnitz specialises in the production of micro metal parts using micro laser sintering, and the sale of associated machines. For the Saxony-based company, sustainability also involves developing and manufacturing products with integrated functions which create added value for customers, but without compromising the material properties of the components when in use.
“New geometries must interact with new materials if products are to be generated which offer added value in terms of lightweight construction and sustainability. Here, customers need professional advice to identify the critical points in the product development and manufacturing processes,” emphasizes Thomas Klotz, Head of Quality Assurance at 3D Micro Print.
One thing is certain, however: without 3D printing, lightweight construction is impossible in many areas, making it an essential prerequisite for material efficiency. In some cases it is even possible to combine several parts in the design stage to create a single component. “Autodesk’s Generative Design approach is an important tool that is often used to create new geometric shapes. It helps our customers to reduce weight and consolidate parts. General Motors, for example, combined this approach with additive manufacturing to redesign a seat mount,” says Krause, citing the example of a component that was developed from the outset with lightweight construction in mind. “The new part consisted of just one component instead of eight, as before. It was also 40 per cent lighter and 20 per cent more stable.”
Lighter and smaller clamping devices reduce costs
Hainbuch has developed ultra-light carbon devices to clamp workpieces during milling, turning and grinding. According to the company, these ensure higher productivity, lower energy consumption and reduce the strain on machine drives. The material used for the CFRP clamping devices makes them up to two thirds lighter than the standard version.
“We can offer carbon variants of almost all clamping devices for specific customer areas. In the mini series, we have also developed chucks with a reduced interference contour and mass. These two factors are playing an increasingly important role in finishing. Modern and future-oriented clamping devices are distinguished by their greater tool accessibility and lower energy consumption. Increased spindle acceleration rates shorten the cycle times. This reduces the overall costs per workpiece,” says Nitsche, describing Hainbuch’s approach. At EMO Hannover, the company will be exhibiting the lightweight Manok CFK manual vice, the mini chuck series and many other innovations that incorporate sustainability aspects.
3D Micro Print uses micro laser sintering technology to produce high-precision lightweight metal microcomponents, offering customers product manufacturing and a comprehensive range of services from a single source. The portfolio includes knowledge transfer, functional component integration, process-oriented design, the production of serial parts and, on request, material development. The processes are designed for very high resolution and precise microcomponents in the µm range. Fine grid structures as well as geometries with detailed internal structures are developed and manufactured. The company is presenting solutions for various industries at the EMO in Hanover.
Artificial Intelligence, Virtual and Augmented Reality increase organisational agility
Sustainability and lightweight construction are important because they offer clear value chain advantages to mechanical engineering companies and their customers. This is also confirmed by the Autodesk Technical Sales Manager Steffen Krause: “The business of more than 60 per cent of our customers is based on success factors and goals that are linked to sustainability – and the numbers are rising. This approach is also passed on down the supply chain to the service providers.”
With this in mind, Autodesk has also decided to focus on automation in the form of artificial intelligence, virtual and augmented reality, and 3D printing. This digitally combines everything from design, mechanical engineering and simulation through to CAM, additive manufacturing and factory management. “This uniform platform does away with the silos between the disciplines, enables greater organisational agility between the engineering teams and gives the manufacturers a competitive edge,” emphasizes Krause.
The exhibits showcased on the Autodesk stand at EMO Hannover will give visitors an impression of what the CAM software can do. Complex components with free-form surfaces will be on display, demonstrating the high surface quality that can be achieved. Also included will be examples of hybrid manufacturing which combine additive and subtractive processes. On display, too, will be exhibits that explore the options for generative design.
With the right development tools and extensive engineering knowledge, lightweight construction can open up a whole world of possibilities. The only limits are those set by the laws of physics. “So far, we have been able to meet all customer requirements. The limits of lightweight construction, including reduced interference contours, are only reached when the holding forces, rigidity and precision can no longer be guaranteed,” emphasizes Stefan Nitsche of Hainbuch. Thomas Klotz of 3D Micro Print adds: “Lightweight construction is currently reaching its limits in highly standardised processes and products that leave no room for improvement in performance.”
Counteracting geometric deviations with measurement data
3D metal printing is also offered by Rolf Lenk Werkzeug- und Maschinenbau GmbH in Hamburg. Matthias Otte is in charge of additive manufacturing. He explains the important factors in the manufacturing process: “The component must be dimensionally stable. This means that any warpage and shrinkage caused by additive manufacturing must be counteracted. An important aspect here is optical geometry capture. This allows us to check instantly for any deviations.” Optical metrology allows the company to support the entire additive manufacturing process chain and thus produce precision-fit components. This begins with geometric measurement of the component, continues with measurement of any deviations caused by warpage and shrinkage, and ends with checking of the resulting finished component. Any inaccuracies in the target geometry can be detected during production. A rapid response can be conducted, if necessary. The company is presenting its expertise in the field of 3D printing at EMO Hannover, based on various components.
Author: Annedore Bose-Munde, specialist journalist from Erfurt
Size: around 8,800 characters including blanks