Measurements trigger an appetite for more
Between fascination and a slight uneasiness –that’s roughly the sort of subliminal reaction even experts occasionally feel when it comes to the subject of “artificial intelligence”. Autonomous robots, self-driving vehicles or cognitive systems that image the functioning of the human brain and are even able to checkmate a chess grandmaster, may trigger concerns regarding a loss of human control. As a key technology for Industry 4.0, self-learning systems can be expected to find their way into the factories, especially if they are introduced gradually and “in small digestible pieces”, and prove that money can be earned with them.
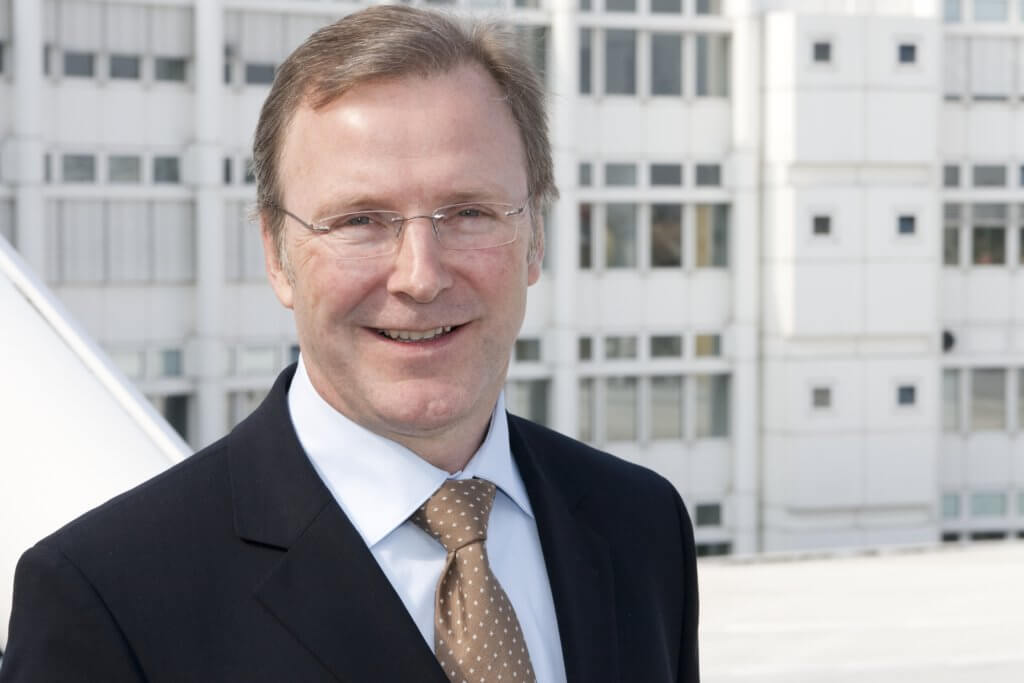
As a sub-category in the field artificial intelligence (AI), it’s primarily machine learning (ML) that’s relevant for industrial manufacturing operations. ML enables systems to understand their surroundings, to plan actions, to respond to impediments, and to communicate with humans. Machines use production data and intelligent algorithms to learn to recognise recurrent patterns and objects autonomously. The learned knowledge can then be applied to unknown and unsorted data. This enables sources of error be identified, processes to be planned and optimised, and forecasts to be drawn up.
Machine learning needs Big Data
The hype currently associated with machine learning, although the concept in actuality dates back to the 1980s, is due to the modern-day options for data processing. It was only with the advent of Big Data applications, high–performance computers and gigantic cloud memories that the appropriate infrastructure came into being, used primarily at first by the internet giants. But the industrial sector is following suit. “From the perspective of robotics, we are following very closely what players on the global market like Google and Amazon, with their IT competences and infrastructures, are developing and researching in regard to production technology,” confirms Prof. Jörg Krüger, Head of the Automation Technology Department at the Fraunhofer Institute for Production Systems and Design Technology (IPK) in Berlin. But the examples from the IT conglomerates cannot be adopted just as they are for industrial applications as well.
It’s true than many companies, especially large ones from the automation and control segment, have been infected by the “ML virus”. But in the view of sectoral pundits the use of machine learning in the industrial segment is in many cases still in its infancy. This appraisal should not be obscured by spectacular demonstrations, e.g. when IBM impresses the public with its Watson system in the Cognitive Factory. Or when Festo, with fascinating exhibits like the very recent “elephant’s trunk”, an intelligent bionic handling assistant, answers the question of how people in the factories of tomorrow can interact with their machines simply, efficiently and above all safely. The technology exists. It’s exciting, and stimulates the imagination, but translating it into real products capable of delivering sales and profits will probably take some years yet.
SMEs and start-ups – the ball’s in their court
The fundamental question involved here is whether machine learning is only something for global players and their ideas for a comprehensive concept of a digital factory. Or whether, besides a top-down development thrust by financially potent large companies with their highly competent research and development departments, a bottom-up breakthrough spearheaded by flexible, innovative small and mid-tier enterprises would also be conceivable.
“Artificial intelligence is an important issue for the future,” says Dr. Wilfried Schäfer, Executive Director of the VDW (German Machine Tool Builders’ Association) and an organiser of the EMO Hannover 2017 (18 to 23 September), the world’s premier trade fair for the metalworking sector. “So small and mid-tier enterprises should also address the possibilities of machine learning in their production operations, enabling them to derive options in good time for their own development thrust.”
For Dr. Cord Winkelmann, Managing Director of Sensosurf in Bremen, things have already been set in motion here on many fronts. “The big companies tend to develop their own solutions, often very complex and comprehensive ones, sometimes spectacular and very effective in terms of marketing,” he comments. “These include a kind of bee swarm flying to and fro, collecting information, exchanging mutual feedback, networking, moving things forward. Digitalisation there is a boardroom issue.”
Innovative start-ups can make their own contribution to progressing development. Sensosurf has adopted the slogan “Sensor integration meets machine learning”. Founded in 2016 as a spin-off of the Institute for Microsensors, -Actuators and –Systems (IMSAS) at Bremen University, the company transfers micro-system technologies to the tough environmental conditions encountered in the mechanical engineering sector. These include flanged and pedestal bearings, linear guides and threaded rods. “We’re exploring fields from which so far there had been as yet scanty information or none at all available,” says Dr. Winkelmann. For data evaluation, machine learning is deployed in order to use information on the machines and processes.
Strategy of small steps
Large quantities of data are essential for machine learning; without them it’s simply not possible. For swift market penetration, says Dr. Winkelmann, it’s crucial that the information generated pays off from the very first moment. “It’s always the small steps we begin,” he explains. These include data evaluation at the machine, networking the machines with each other, detecting what’s characteristic about what’s happening. “Once you see what data are obtained, evaluated and visualised, you quickly get used to the new insights and the opportunities they offer,” says Dr. Winkelmann. “Measurements trigger an appetite for more.” What proves most persuasive for machinery manufacturers, he says, is that the machine learns to protect itself against operator error. The data obtained can also be used as a defence against unjustified warranty claims, for example.
“It’s important to map out migration paths for companies showing how they can introduce the technology of machine learning in small, digestible pieces,” concurs Fraunhofer expert Prof. Krüger. He sees the principal focuses of using ML at machine tool manufacturers as currently centred around the field of condition monitoring. This essentially involves interpreting measured data using pattern detection processes. The knowledge required for detecting process or machine conditions is acquired by the processes of machine learning.
Potentials in energy management
Besides the fields of predictive maintenance, condition monitoring and quality management, however, self-learning systems can also progress energy management. At the EMO Hannover 2017, the Munich-based company Gerotor will be premiering its HPS high-power storage system, which is designed to reduce the energy and connection costs involved with the aid of intelligent algorithms. The idea for the product originated with Formula 1, or to be more precise with the KERS (Kinetic Energy Recovery System) used there. The system was imposed upon racing cars at the time for reasons of environmental protection, since it returns to the drive axle energy produced during violent braking manoeuvres, by means of a rotating flywheel system.
Gerotor’s founders saw huge potential in “this efficient and at the same time wear-free technology, not only for cars driving round in circles,” as Gerotor’s director Michael Hein colloquially puts it. In the search for an application that likewise involves many and frequent braking and acceleration functions, sometimes within a matter of seconds, they found what they were looking for with machine tools and tool spindles. The advantages of digitalising and networking the power storage system were obvious: “If you’re inside the energy circuit, you’re in the information centre too.”
Coupled directly to the line, without requiring a power connection of its own, the new power storage system upgrades the efficiency of the entire line by means of energy recovery, peak smoothing and digitalisation. For this purpose, the system measures all currents and cycles, acquires data and information, improves its own algorithms, and draws conclusions. Whereas with traditional control strategies energy savings of at most 10 to 25 per cent can be achieved, says Michael Hein, users with intelligent strategies ought to achieve about double the savings effect. For Michel Hein, energy management offers a particularly simple and efficient entry route into ML. “Energy systems have to be 100-per-cent predictive,” he emphasises. “We need intelligent control strategies and an infrastructure that re-adjusts itself.”
Return on investment is crucial
He admits, however, that the concept of machine learning is practically ignored in meetings with customers The crucial consideration is rather the ROI (return on investment): “We sell our products solely by means of the argument that we save more than we cost.” This may in fact be one of the reasons why many companies tend to be rather taciturn when asked about their ML strategies. Machine learning is a means to an end, not a sales argument.
There is in any case no blueprint for introducing your own strategies. It’s advisable to call in some expert knowledge, through either one of the various Fraunhofer institutes or outside service providers. As Jörg Krüger explains, each company first has to clarify what form of intelligence is desired for a machine, a system or a robot, such as detection of the machine’s condition, autonomy, automatic adaption to changes like tool wear and tear or component characteristics. Autonomous replanning and self-organisation of production sequences, comprehending human commands and gestures for simplified programming das also rank among the capabilities that a machine could learn by itself. But Jörg Krüger also points out that this entails a further question: who checks whether something has been properly learned before the machine starts to operate automatically with the knowledge concerned?
There are also questions to be answered regarding IT security and data protection, or who assumes liability for decisions taken by an intelligent system. Could perhaps once again the “uneasiness” in dealing with cognitive systems, and possible loss of control come into play here? Cord Winkelmann doesn’t think so. A much more serious impediment for machine learning, he believes, and indeed for the digital transformation in general, is the inadequate provision of fast internet in many places, particularly for plants located in rural areas.