Networking and digital know-how for new business models
The METAV organiser VDW (Verein Deutscher Werkzeugmaschinenfabriken – German Machine Tool Builders’ Association) staged its International Press Forum in Aachen on 12 and 13 December. The 21st METAV, the International Exhibition for Metalworking Technologies, will open its doors from 10 to 13 March 2020 in Düsseldorf.
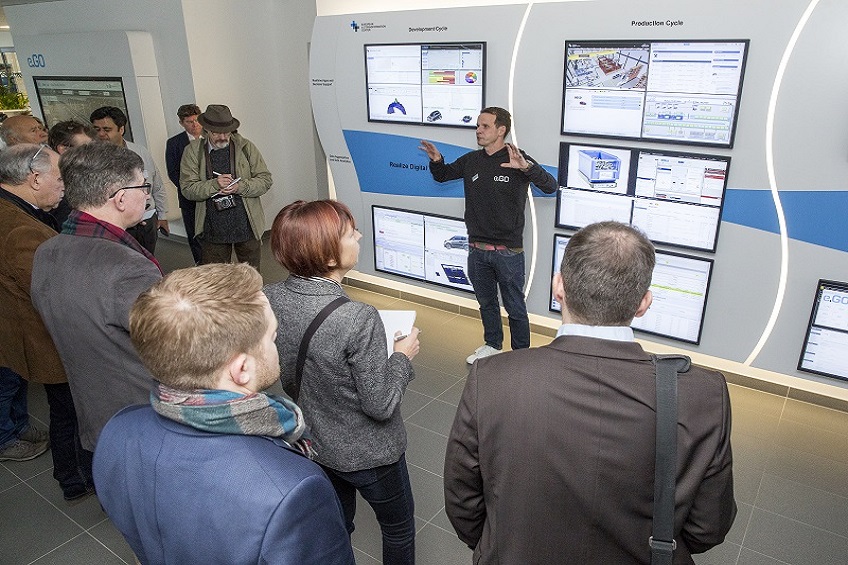
40 years after its launch, the fair is not only a showcase for new metalworking-related products, technologies and services, it also reflects the strong sense of anticipation on the threshold of the fourth industrial revolution. More and more topics – such as networked production, artificial intelligence and Industry 4.0 and the resulting challenges (especially for medium-sized companies) – are vying for attention. The Forum was held in the WZL (Laboratory for Machine Tools and Production Engineering) at RWTH Aachen University, one of the most renowned production technology research institutes in the world. It quickly emerged that both interdisciplinary research and a broad-based drive to transfer knowledge and information are required if industry is to succeed in developing value-added for companies and new business models from vast quantities of data.
Hot topics – The key to METAV success
“Industry 4.0 is gathering pace in the field of metalworking,” said VDW Executive Director Dr. Wilfried Schäfer at the Forum. The METAV provides an opportunity for comprehensive appraisal and evaluation of these developments – from networked manufacturing, cloud applications, data analysis and 5G through to machine learning and artificial intelligence. METAV 2020 will also feature a umati (universal machine tool interface) showcase, albeit in a smaller format to that seen at EMO Hannover. This will demonstrate how quick, easy and uncomplicated it is to exchange data via the umati interface.
The 3rd mav Automation and Digitalisation theme park will provide an exhaustive overview of interesting Industry 4.0 solutions and projects which are already up and running. It will also give visitors the opportunity to talk to the experts. Another key topic is security. The VDW and VDMA are organising their first ever congress on cybersecurity on 11 March 2020. This will address the question of data availability and security. As Dr. Schäfer underlined: “The success of new data service-based business models depends very much on strong security.” The potential nature of such business models is a topic of research at the Aachen WZL. On its METAV stand, the WZL and an industry partner will be exploring the topic of the platform economy, i.e. the monetisation of machine data. Just what significance this holds for the future of industrial production was also made clear at the METAV Press Forum.
Event hosted by prestigious research hub
The WZL of the Rheinisch-Westfälische Technische Hochschule (RWTH) Aachen is a research institute consisting of four mechanical engineering chairs which conduct teaching and research in the field of production technology. It has been carrying out research for over 110 years. The WZL has organised the Aachen Machine Tool Colloquium (AWK) together with the Fraunhofer Institute for Production Technology (IPT) since 1948. It is held every three years and, attracting well over 1,000 international visitors, is one of the largest industrial colloquia worldwide. 2020 will see the 30th such event. With over 45,000 students, Aachen is the largest university for technical degree courses in Germany.
In their quest to find solutions for industrial problems, WZL and Fraunhofer IPT have a history of collaborating with partners from different industries on a diverse range of practical projects that meet the needs of industry. As Prof. Christian Brecher, Head of the Chair of Machine Tools and, from 2020, President of the WGP (Wissenschaftliche Gesellschaft für Produktionstechnik – German Academic Association for Production Technology), made clear in his welcoming speech at the METAV Press Forum, integrative and cross-domain cooperation is also at the heart of the new Internet of Production (IoP) Cluster of Excellence which was launched at the beginning of 2019.
“Based on12 years of research by the Integrative Production Technology for High-Wage Countries Cluster of Excellence, this is the next important milestone in the creation of further application-oriented and innovative solutions in the field of production technology,” says Brecher. The Internet of Production offers secure, real-time availability of all relevant data any time and any where, and is therefore considered to be a core element of Industry 4.0.
Experience modern production technology live
Selected WZL projects were presented by Prof. Thomas Bergs, Chair of Manufacturing Technology. “Upcoming challenges can no longer be met using conventional methods,” stressed Bergs. The Internet of Production facilitates future value creation, increases companies’ ability to deal with crises and thus helps them to cope with changing framework conditions. Bergs explained the ability to forecast in adaptive process chains, presented the benefits of digital twins for quality assurance and underlined the necessity of analysing the data gained during the production process. Only if we succeed in comprehensively evaluating this data and in exploiting the results will it be possible to derive entrepreneurial value-added and new business models. Internet of Production – Turning Data into Value is also the motto of the AWK.
The press forum participants were given a demonstration of this during the subsequent tour of the machine halls. In the MARS (Metrology, Assembly and Robotic Systems) hall of Prof. Robert Schmitt’s Chair of Production Metrology and Quality Management, the integration of intelligent sensors into the production process, including robot-supported handling and assembly processes, was demonstrated on various test benches. A particular focus was on modelling, i.e. digitalisation of the real world and the creation of a digital twin. One of the machine tool-related research focuses of the chair is on “on-machine measurement”, in which machine tools are equipped to carry out closed-loop dimensional component tests. Shifting component testing to the processing machine allows quality control loops to be considerably shortened and costs saved.
The Demonstrationsfabrik Aachen (DFA) of the Chair of Production Engineering headed by Prof. Günther Schuh also presented emblematic examples from the Internet of Production. These included collaborative robots, an industrial 5G infrastructure and various track&trace solutions. The DFA is an independent company devoted to the transfer of knowledge between researchers and those working in industry. Here, small series of products are manufactured under real production conditions. It also tests products and technologies for companies.
High priority for knowledge transfer
A high degree of importance is attached to the transfer of knowledge between the worlds of research and industry. Alongside scientific lectures, the sharing of information among experts (e.g. via the AWK) and its demonstrators in the machine halls, WZL also offers further training events and, most recently, digitalisation surgeries. A seminar on “Digitalisation and Artificial Intelligence in Manufacturing Technology” was included in the WZL programme for the first time in the winter of 2019. It was fully booked within a very short time. As seminar leader Dr. Daniel Trauth explains, answers are provided to frequently asked questions, such as possible forms of digitalisation in participants’ own companies, how new or existing machines can be networked or how artificial intelligence and machine learning can best be exploited. “The main challenge lies in packing all this in one seminar,” says Trauth. There is great demand for information, he says.
Industry 4.0 qualification drive
The VDW and the VDMA are the sponsors of the “Nachwuchsstiftung Maschinenbau” (Youth Education and Development Foundation for Mechanical Engineering). This is committed to meeting the high demand for qualifications and further training. Under the patronage of the Prime Minister of North Rhine-Westphalia, Armin Laschet, the Youth Education and Development Foundation for Mechanical Engineering is currently conducting a state-wide qualification drive for Industry 4.0 entitled NRWgoes.digital. Roughly 300 teachers and about 300 trainers work their way through a 25-day Smart Factory programme which focuses on technical and methodological aspects. As important disseminators, these will then pass on their knowledge to over 1,400 trainees over the subsequent 2.5 years. The trainees can then acquire the additional Digital Manufacturing Processes qualification. “Our goal is to prepare skilled workers for working and learning in the digital world of work of the future,” says Dr. Wilfried Schäfer, Executive Director of the VDW. This aspect, of course, will also feature prominently at the fair. Each day, the Youth Education and Development Foundation for Mechanical Engineering is organising several live sessions with digital leaders on the project at METAV Düsseldorf 2020.
9,296 characters
Author: Cornelia Gewiehs, freelance journalist, Rotenburg (Wümme)
Downloads
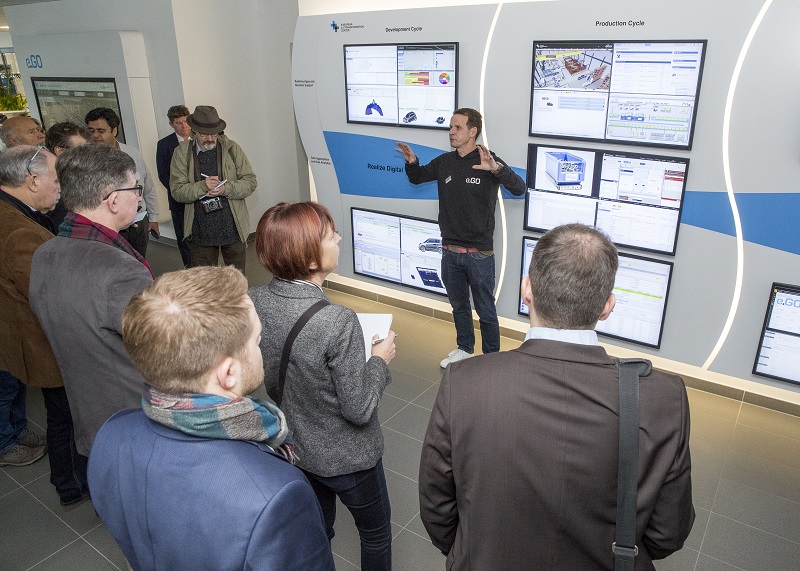