Precision grinding ensures smooth and efficient running in electric vehicles
A cyclist out in the countryside on an e-bike would rather hear birdsong than annoying noises from the bike’s drive unit. Smooth running is also an important factor in electric cars. The electric motor is much quieter than a diesel or petrol engine, meaning that unpleasant noises are more noticeable when driving.
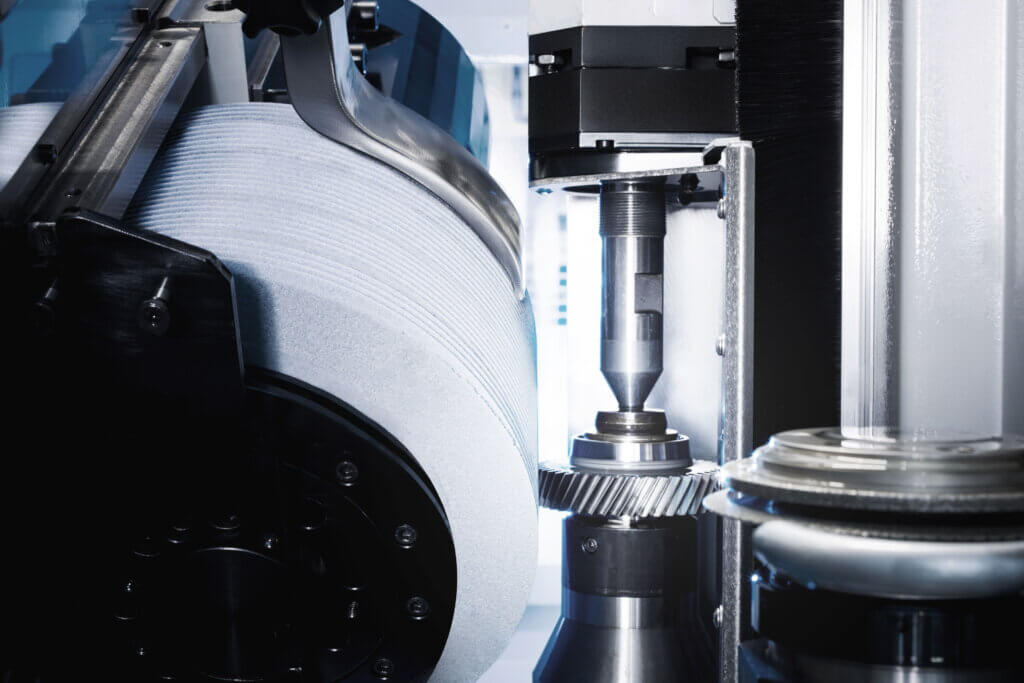
Accuracy in the micrometer range
Electric vehicle drives must be powerful yet compact – a technical challenge that requires extremely high-quality components. State-of-the-art milling and grinding machines are therefore needed to produce the gearings in electric cars. They offer extreme precision down to the micrometer range: one micrometer is roughly a fiftieth of the thickness of a human hair. Under high loads, it is superior microgeometry which determines perfect meshing of the gears. Innovative grinding technology enables very high surface quality grades, optimum concentricity and perfect tooth flank geometries to be achieved. It also ensures that the gears can be adapted to the natural frequencies of the drivetrain and optimally dampen its vibrations.
The gear hobbing and generating grinding machines of GrindingHub exhibitor Liebherr-Verzahntechnik GmbH from Kempten in the Allgäu region of Germany help gear manufacturers to supply large quantities of top-quality components to electric vehicle manufacturers. This guarantees efficient, quiet and clean gear operation. The main focus here is on minimizing friction and increasing tooth flank load-bearing capacity. These can be ensured through fine grinding and polishing.
Superior surface quality
“Compared to conventional combustion engine gearboxes, e-drives generally need more exacting surface qualities in the gearing,” explains Thomas Breith, Head of Product Management at Liebherr-Verzahntechnik GmbH, and cites a couple of reasons for this: firstly, the fundamentally different nature of the transmittable power, and secondly, the high thrust torques. The latter are generated through recuperation which allows energy to be recovered during braking. The exacting requirements with regard to audible and perceptible vibrations (Noise Vibration Harshness, NVH) also require high surface quality in the gearing. And, not least, reduced roughness values ensure a longer battery range. “This means that maximum gearing quality is required for all functions,” says Breith.
Precise roughness specifications
But how can the increased requirements for the production of transmission components be met? Original equipment manufacturers (OEMs) usually specify the required manufacturing processes for suppliers by defining certain surface roughness target values. These are defined in terms of international standards – such as average roughness (Ra), maximum profile height (Rz), core roughness depth (Rk), reduced peak height (Rpk) and reduced valley depth (Rvk). Fine grinding with dual grinding worms facilitate high, but still grindable surface quality grades. “These tools use differently optimized grinding worm specifications for each grinding stroke,” explains Breith. The result is high-precision gear geometries in the DIN and ISO-compliant evaluations, as measured on gear measuring devices. The Rz values are between 1.2 and 1.8 micrometers.
Fine grinding and polishing worms
“We need to use so-called ‘polishing-grinding’ if the OEM requires even higher Rz values of between 0.8 and 1.2 micrometers,” says Breith. A very fine grinding worm and a polishing worm are used. “The polishing cut then only removes 2 to 3 micrometers on the tooth flank. A preliminary test must be carried out to optimize the process for each individual component. Here, it is essential to match the measuring equipment used by the manufacturer with that of the end user,” says the Liebherr manager.
Many challenges need to be overcome in order to achieve a perfect result. According to Breith, the minimum requirement is a high-precision gear grinding machine running the required additional application software. “The process is optimized using appropriate application technology on the part of the machine manufacturer. Process reliability is only possible with very high-quality clamping devices and grinding tools,” he explains. The manufacturer’s expertise is important here, and intensive customer support is crucial.
Innovative technology gives companies competitive edge
The switch from combustion engines to electric drives means that fewer gears and therefore smaller quantities will be required in future. However, increasing quality demands are now being placed on gear manufacturers, making it potentially worthwhile to invest in innovative and flexible technology that can also handle small quantities. Suppliers who invest in equipment for the flexible production of ultra-fine surfaces with different contours can thus gain a competitive edge and a rapid return on investment as the numbers of electric vehicles continue to rise.
GrindingHub exhibitor Emag GmbH, based in Salach in southwest Germany, also offers reliable, high-precision grinding solutions for use in electric vehicles. The technology guarantees maximum surface quality with no obtrusive running noises. The German machine tool manufacturer is now bringing the technology of its Milan-based subsidiary Emag SU to the attention of production planners and will also be showcasing it at GrindingHub. The specialists from Italy develop high-performance solutions for gear grinding.
Not frightened by ghost frequencies
Oliver Hagenlocher, Head of Marketing at Emag, suggests generating grinding machines with an innovative axis concept as outstanding solutions for gear grinding. They can create the perfect surfaces that are so important in electric vehicles. The decisive factor here is that the generating grinding machines have no tangential axis; instead the existing Y and Z axes generate a “virtual” tangential axis through simultaneous movement. This minimizes the distance between the A-axis and the tool contact point, which in turn prevents “ghost frequencies” on the surface of the component.
This may sound rather ethereal, but there are very rational reasons for it. Ghost frequencies are frequencies that do not coincide with the meshing frequencies and their harmonics; they can also be caused in the component during grinding. Ghost frequencies are provoked by minimal irregularities that are almost impossible to avoid in series production. They become particularly critical when these deviations lead to harmonic excitation. A great deal of know-how and process experience is required to recognize and avoid the causes of such irregularities.
Pleasant hum rather than obtrusive noise
As in electric cars, it also makes sense to optimize the surface quality of the drive components in e-bikes – albeit not to the same quality level. “The current e-bike applications do not yet have the same quality requirements as those currently stipulated for the e-drives in cars,” says Breith. However, the Liebherr manager cannot rule out the possibility that “certain gearing criteria for electric bicycles will become more exacting in the future, similar to those in the automotive sector.”
High-precision and modern production technology is therefore essential for suppliers who want to be at the forefront in the transition to electric vehicles. Because only with perfectly polished components can electric cars and e-bikes run with maximum efficiency and purr like a cat when on the road instead of screeching or squealing.
(8.156 Characters, including blanks)
Author: Daniel Schauber, Specialist Journalist, Mannheim
Contacts
Gerda Kneifel
Press and Public Relations
Lyoner Str. 18
60528 Frankfurt am Main
Germany
g.kneifel@vdw.de
Phone +49 69 756081-32
https://www.vdw.de/
Liebherr-Verzahntechnik GmbH
Thomas Weber
Head of Marketing
Kaufbeurer Straße 141
87437 Kempten/Allgäu
Germany
Thomas.Weber@liebherr.com
Phone +49 8317 8632-85
https://www.liebherr.com/
GrindingHub: Hall 7, Stand 7C02, Main Exhibitors
Emag GmbH & Co. KG
Oliver Hagenlocher
Head of Marketing
Austraße 24
73084 Salach
Germany
ohagenlocher@emag.com
Phone +49 7162 17-4267
https://www.emag.com/
GrindingHub: Hall 9, Stand 9C41, Main Exhibitors
Daniel Schauber
Freelance specialized journalist
Meerfeldstr. 14
68163 Mannheim
Germany
daniel@schauber.com
Phone +49 170 2031976
Press Material
Exhibitor & Visitor Quotes (.pdf)
Pictures
Picture 01: Thomas Breith Liebherr Verzahntechnik
Picture 02: Liebherr Gear Solution
Picture 03: Liebherr E Bike
Picture 04: EMAG G160
Picture 05: EMAG Schleifloesung Verzahnung