Seizing opportunities for new business and climate protection
The extent to which the climate protection and decarbonization are impacting the world of manufacturing technology will be made clear at EMO Hannover 2023 with its “Future of Sustainability in Production” focus topic. This will be addressing the latest developments in sustainable production, energy efficiency, alternative drives and much more. The combustion engine played a dominant role for decades, but now machine tool manufacturers and suppliers are increasingly looking for ways to compensate for the declines.
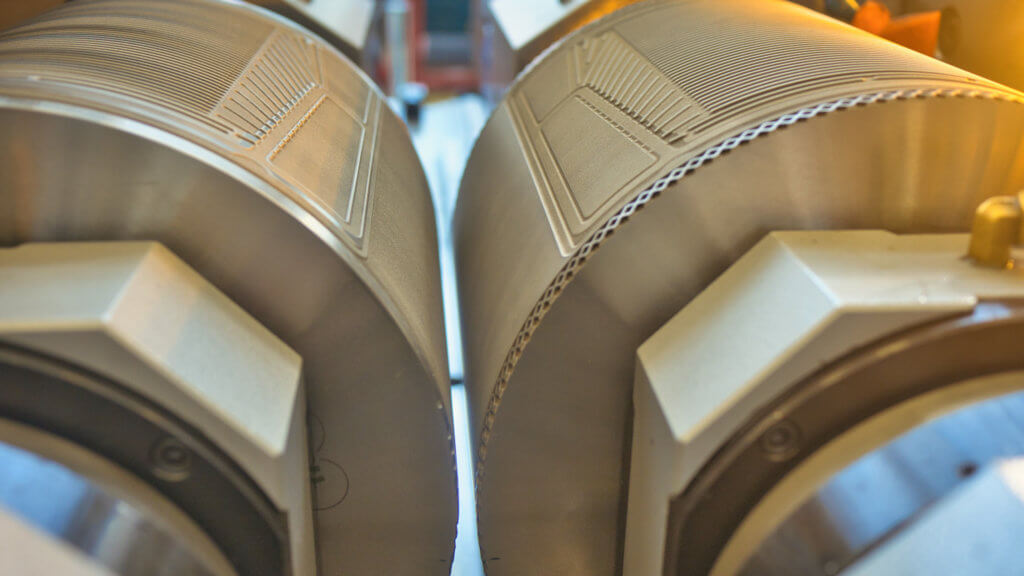
The extent to which the climate protection and decarbonization are impacting the world of manufacturing technology will be made clear at EMO Hannover 2023 with its “Future of Sustainability in Production” focus topic. This will be addressing the latest developments in sustainable production, energy efficiency, alternative drives and much more. The combustion engine played a dominant role for decades, but now machine tool manufacturers and suppliers are increasingly looking for ways to compensate for the declines. A move into hydrogen technologies offers great potential and opportunities for new business. Scientifically supported development partnerships along the value chain could reduce investment risks.
Germany’s search for a reliable supply of green hydrogen is currently a major issue, and not just since the German government renewed its National Hydrogen Strategy in which it lays down the national guidelines for the production, transport and use of hydrogen and its derivatives. Green hydrogen is produced from the electrolysis of water, using electricity from renewable sources – with no greenhouse gases being emitted. Developing the necessary infrastructure is one challenge; actually producing the green hydrogen is another.
Scientific input for innovation
Until sufficient quantities of green hydrogen are available that can replace some of today’s fossil fuel consumption, the WGP (German Academic Association for Production Technology) believes that the main priorities are to automate the production of stacks and electrolyzers, dramatically increase production capacity, and ensure the required quality of the process. Stacks, the core component of electrolyzers in which water is split into hydrogen and oxygen, are currently produced using purely manual methods, and are therefore very costly, the WGP explains. Furthermore, only limited production capacities are available. WGP researchers are keen to provide the scientific input for upcoming tasks.
The Fraunhofer-Gesellschaft as well as various universities and other higher education institutions are currently working on hydrogen technologies, with particular attention being paid to identifying the ways in which industry can participate. Major companies such as Bosch, ThyssenKrupp and ABB have long since developed their own strategies for the fast-growing market. A further important aim is to accelerate the transformation on a broad scale if ambitious climate targets are to be met or if companies wish to create an edge for themselves in the technological development of hydrogen systems.
Virtual platform turbo-driving the value chain
“Referenzfabrik.H2” was set up by the Fraunhofer Institute for Machine Tools and Forming Technology IWU in Chemnitz and is operated jointly with the Fraunhofer Institute for Production Technology IPT in Aachen and the Fraunhofer Institute for Electronic Nano Systems ENAS, also located in Chemnitz. It serves as a pacemaker for the large-scale industrial production of electrolyzers and fuel cells. Referenzfabrik.H2 represents a hybrid production system based on physical and virtual components. It comprises machinery and equipment for the production of the main stack components, including the bipolar plate (BPP), gasket and catalyst coated membrane (CCM).
“Fraunhofer is exploring decentralized solutions,” explains Dr. Ulrike Beyer, head of Referenzfabrik.H2. The novel concept allows the necessary technological developments to be undertaken at the different sites. For example, a forming press for BPPs can be made available in Chemnitz and production modules for CCMs in Chemnitz and Aachen. Their digital twins are collected in a common architecture and used for process comparisons, evaluations and observations. The aim is to develop a technology kit whose individual components can be evaluated from both technological and economic viewpoints. The goal is to reduce the investment risk and support companies in setting up their hydrogen business units.
“There is huge interest in hydrogen technologies, including from SMEs,” notes Dr. Beyer. However, she points out that smaller companies are often more interested in generating clean energy for their own production. “But I think what is more important is to recognize the unique opportunity there is here for generating new business in a huge market,” she says. This applies above all to companies with expertise in metalworking and metal forming. Referenzfabrik.H2 therefore attaches a great deal of importance to industrial companies of different sizes and orientations getting involved and working together with their researchers in order to further the production of hydrogen systems.
Expertise from partner companies – a key component
Everyone works together as equals in the Referenzfabrik, reports Dr. Michael Hirsch, “New Technologies” business unit manager at Profiroll Technologies in Bad Düben. Profiroll has a long tradition of collaborating with the Fraunhofer IWU, says Dr. Hirsch. That is why the company, which specializes in profile and thread rolling technology and is also exhibiting at EMO Hannover in September, came on board at an early stage, he says. There was another good reason for the shift to hydrogen: Profiroll is currently exploring various options as a means of compensating for declines in the automotive segment. However, the greatest opportunities for hydrogen are not believed to lie in the vehicle sector, but rather as an energy carrier in industry and for the storage of energy. Profiroll has developed a roll-to-roll line for the production of bipolar (semi)plates in cooperation with Fraunhofer IWU for Referenzfabrik.H2.
The advantage of hydrogen technologies for Profiroll, says Dr. Hirsch, is that they are based on proven technology: “Fuel cells and electrolysis are nothing new in principle, but so far they have not progressed beyond the laboratory. Now a market is developing, and we need to scale up for mass production.” The Referenzfabrik cooperation raises the prospect of being able to produce faster and more cost-effectively.
Open-door policy
The Referenzfabrik.H2 partner model is designed to allow companies to join at any time with “Starter” status and then to develop through to “Expert” or “Champion”. Events and training courses are offered that initially focus on basic topics such as the different types of fuel cell and electrolyzer, how stacks work, or quality assurance. There are also workshops in which individual process steps are analyzed and coordinated, or issues such as error tolerances and permissible geometric deviations are discussed.
“Such scientifically-based exchanges can help companies save valuable time,” says Dr. Thomas Koch, Head of Product Strategy at NSH Technology, Chemnitz, explaining the motivation for taking active part in the Referenzfabrik. The company recently joined Referenzfabrik.H2 as a partner on the basis of its expertise in the roll-to-roll process, which is necessary for the cost-efficient production of metallic bipolar plates. “We shed light on the value chain and are keen to see what needs emerge in the market, and what weaknesses can be eliminated,” says Dr. Koch. The working groups do the same. The NSH Group contributes experience from turnkey projects for the automotive industry, which is now increasingly turning to alternative drive systems. The main focus in Referenzfabrik.H2 is on rotationally symmetrical plant components and tools, such as those for bipolar plate production, Koch says. But it is also fundamentally about taking production technology for the energy transition to the next level.
Great importance of collaboration on hydrogen
The value chain is already very well covered in the Referenzfabrik, notes Michael Hirsch of Profiroll. Companies large and small are involved, with the spectrum ranging from machine tool manufacturers through to specialists for coatings, seals, cutting processes and laser welding. “Naturally, the Referenzfabrik.H2 teams will become stronger the more people that get involved,” says Hirsch, who would also like to see greater participation from end users and OEMs. He is not worried about working together with competitors. “Of course, pre-production research and secrecy are always an issue,” he acknowledges. “But we are all experienced enough to handle this.”
For Thomas Koch, too, the advantages of cooperation outweigh the disadvantages. He sees far greater danger in experiencing a repeat of the trauma from the development of solar energy systems. “Our goal must be to create low-cost production technology for hydrogen systems,” he cautions. “We cannot afford to squander our technological lead simply because it is cheaper to produce elsewhere.”
Raising acceptance levels for hydrogen – an issue of international importance
Dr. Ulrike Beyer, however, has other worries, which is why she is less concerned about competition when it comes to hydrogen technologies, and much more about cross-border cooperation. “We are strongly committed to ensuring the transformation is a success,” she says. However, it is also clear that Germany will never be able to produce enough green hydrogen for its own needs. It will always be dependent on imports. Here, too, there should be no repetition of old mistakes. “It is clearly in our interest to cooperate as equals and to support the local population,” urges Ulrike Beyer. The companies and well-trained staff in the countries from which Germany imports hydrogen should be supported in setting up their own projects. “After all, the motivation of those who promote a general acceptance of hydrogen is climate protection.”
((Total length: 9,780 characters including spaces))
Author: Cornelia Gewiehs, Freelance Journalist, Rotenburg (Wümme)