Wide range of innovative technological highlights at METAV 2018
Düsseldorf, Frankfurt am Main, July 2018. – This year’s METAV was held from 20 to 24 February in Düsseldorf, where more than 500 exhibitors presented their innovative technologies. The core theme of the event is metalworking, but digitalisation and networking were again given their own spotlight in a separate Industry 4.0 theme park. The structure was changed in 2016 to focus on the four topics of Additive Manufacturing, Medical, Quality and Moulding in specially dedicated areas, and this was once again the case this year.
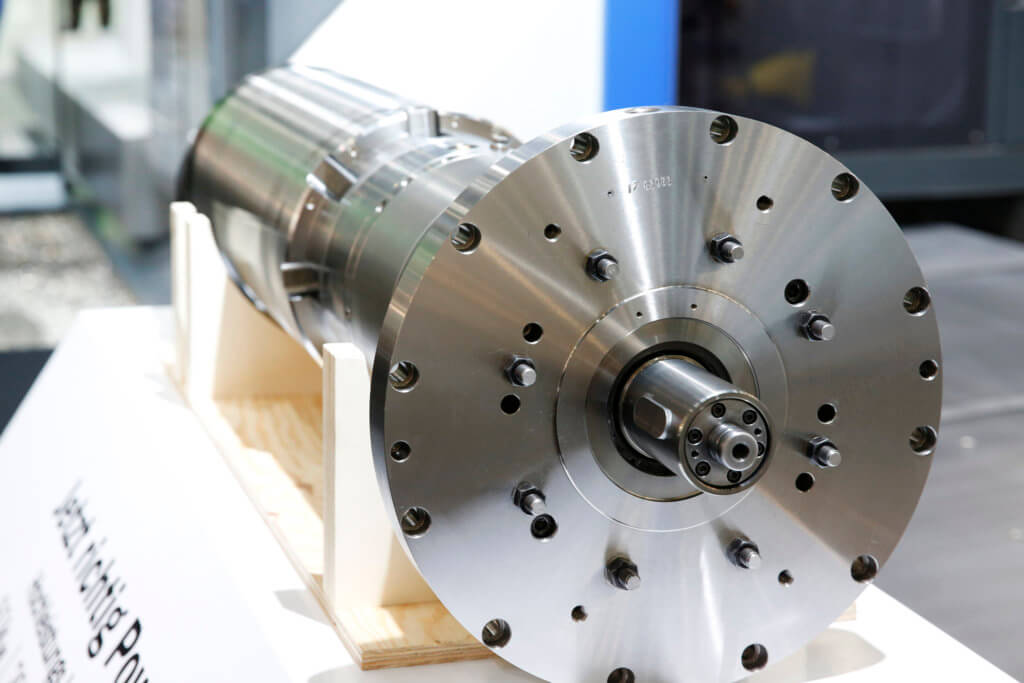
Wide variety of innovative 3D printing processes
Additive manufacturing increases the degree of creative freedom in the production of components, tools and moulds. Systems and software solutions for generative processes were presented, as were innovative components which can be produced using this method, for example in tool and mould making.
Together with its customers and users, the company Trumpf Laser- und Systemtechnik GmbH from Ditzingen, Germany, for example, showcased plastic die-casting tools with complex cooling channels that could not previously be produced using conventional methods. These newly developed tools were manufactured on the company’s own SLM (Selective Laser Melting) machines. Significantly shorter cycle times can be achieved in the series production of plastic injection moulded parts thanks to the improved cooling effect. The resulting increase in productivity leads to cost savings that far outweigh the higher production-related costs for tools and moulds.
The Aalen-based German company Mapal Dr. Kress KG uses the possibilities of additive manufacturing to produce application-oriented hydraulic expansion chucks. With previous hydraulic expansion chucks, the soldered connection between the base body and sleeve represented a weak point in terms of transmissible torque, temperature resistance and geometry. Additive processes now make it possible to manufacture hydraulic expansion chucks without joints which are individually adapted to the particular machining process. They not only provide the damping effect of a hydraulic chuck, but are also as slim as conventional shrink chucks. According to Mapal, this allows customers to choose the most economical and reliable combination of hydraulic expansion chuck and tool.
DMG Mori GmbH, Hilden, Germany, presented the Lasertec 30 SLM model, a machine for the generative production of components using SLM, which significantly simplifies the otherwise highly complex handling of the powder. A closed powder circuit protects the machine operator from contact with the powder, and the powder from environmental factors such as humidity. The fact that each type of powder is held in its own exchangeable unit facilitates quick and contamination-free powder changes. It is relatively simple to exchange each individual unit, thus avoiding long set-up and downtimes of the machine.
The US company Desktop Metal, from Burlington, presented 3D printers at METAV which can also be used in the office, for example for prototype construction. In the systems, metal powder bound in wax is built up in layers to form a green compact of the component using the bound-metal deposition process. Further process steps include debinding, in which the wax is removed from the component, and sintering, in which the metal powder is fused into a completely sealed part that is free of residual stress. Every step, from the creation of the CAD file to the finished part, is supported by the Studio System software. The material can also be changed quickly and easily using exchangeable material cassettes. Health risks from metal dust are prevented by binding the metal powder in wax.
The company 3D Systems GmbH from Darmstadt, Germany, presented systems for direct metal printing using the powder bed process. The 3DXpert software is an integral part of ProX DMP machines and ensures fast preparation of the print data. The parameters for direct metal printing can be selected from a database for the corresponding powder material. A special feature is the vacuum chamber of the machines, which ensures very low consumption of protective gas and prevents oxidation of the metal powder during laser melting. The largest machines currently available offer maximum construction platform areas of 500 x 500 mm.
Data acquisition and evaluation as the focus of industry 4.0 solutions
The integration of machine tools and monitoring as well as the evaluation and presentation of machine data represent just one aspect of the Industry 4.0 solutions.
Many metalworking companies presented their new developments in the special Industry 4.0 Theme Park show. In addition to the practical solutions presented by the exhibitors, there were also thought-provoking talks and expert discussions on digitalisation. Numerous exhibitors also presented their Industry 4.0 ideas and process optimisation solutions outside the Theme Park.
The German company Gühring KG from Albstadt, for example, presented its GTMS v6 tool management software, a new version of the platform for managing production tools. Serial numbers are used to document and manage tool data throughout the life cycle. The tool management software can be integrated into a company’s existing IT infrastructure (such as ERP, PPS or CAD systems) via interfaces. The software has been made even user-friendlier. The modular structure allows the tool management system to be adapted to the respective requirements of each individual company.
Under the name Heller4Industry, the machine tool manufacturer Gebr. Heller Maschinenfabrik, Nürtingen, Germany, offers a platform for enhanced evaluation of machine data featuring an operator-oriented, web-based user interface. The platform offers the possibility to monitor the (wear) conditions of axes, spindles or other assemblies and report on them in plenty of time before a critical value is exceeded. This information can be used to order and replace a worn bearing or a ball screw, thus avoiding machine failure. Furthermore, process data can be evaluated on the platform and used to optimise processes.
Axoom Solutions GmbH, Karlsruhe, Germany, presented modular, cloud-based solutions for production and the entire value chain in the Industry 4.0 Theme Park. The digital business platform offers Industry 4.0 solutions for manufacturing companies (Smart Enterprise) and machine manufacturers (IoT). In the future the platform will enable companies to handle order management, material procurement, machine occupancy and processing sequences within a single system. The browser-based platform ensures that the data and key indicators are available and retrievable at all times.
Hexagon Manufacturing, Wetzlar, Germany, offers solutions in the field of metrology; its product portfolio now includes coordinate measuring machines, automation solutions and 3D laser scanners. Hexagon showcased one of its highlights, a mobile laser scanner for the digitisation of large components, and brought along a rotor blade of a wind power plant. In addition, Hexagon presented its white light scanner systems which can be used for the contactless digitisation of components in the shortest possible time. The 3D data thus captured can be used in a variety of industrial applications, such as quality assurance.
Significant progress in automation and handling technology
Not only the machining of the components, but also the loading and unloading of the machine tools and the clamping of the workpieces to be machined are important aspects of metalworking. in the field of handling and clamping technology the focus was on innovative automation technologies, but also on new technologies. The goal: to make processes safer, more efficient and more economical.
HandlingTech from Steinbronn in Germany, for example, is a specialist in flexible automation systems, which it presented at METAV 2018 as stand-alone systems or as extensions for machines. It presented an ecoZ robot cell that automates the otherwise costly and time-consuming manual loading and unloading of machine tools. Gripper and prism holders in the deposit station which are adapted to the handling tasks ensure that both cylindrical and rectangular workpieces are handled safely. The systems are specially designed to offer flexible application possibilities, which also makes automation economical for small series production. The robot cell can be loaded and unloaded without interruption via a drawer system outside the safety area.
Security technology in machinery and plant engineering
The German company Euchner GmbH + Co KG, Leinfelden-Echterdingen, has come up with a modular gate box in response to clients’ demands for customised solutions for the locking of safety doors. Euchner’s MGB2 refines the concept of a multifunctional gate box; it enables customers to adapt the functions of the box to their individual needs and circumstances. Two “submodules” with up to three operating elements each can be integrated into the locking module via the mounting plate. Modules can even be replaced during operation (hot-plug compatible). In addition to the locking module, the system also includes a handle module for opening the safety door. A bus module can be used for integration into a bus system via Profinet / Profisafe.
Intelligent clamping
In the field of clamping technology, German company, Schunk, based in Lauffen am Neckar, presented new systems for handling and clamping workpieces and tools. New, flat zero point clamping modules offering greater rigidity provide increased stability and reduced vibration sensitivity during machining of the workpieces. Another innovation presented by Schunk was the Tendo Slim 4ax hydraulic expansion chuck. The outer dimensions correspond to the slim heat-shrink contour as specified in DIN 69882-8, but offer additional advantages such as vibration damping, easier handling and shorter set-up times compared to shrink-fit fixtures.
For lathe chucks, Schunk has developed the Rota NCR, a sealed 6-jaw power chuck in which two jaws are pendulum-mounted in pairs, enabling thin-walled components to be clamped with particularly low deformation. The six jaws distribute the clamping force over a larger area. The sealed system allows maintenance intervals to be significantly extended. Schunk also presented the Rota NCE, a power chuck with a weight-optimised design. The reduced weight lowers the mass moment of inertia when the spindle is accelerated and braked, which in turn saves energy and shortens cycle times.
Hilma-Römheld GmbH, a German based supplier of clamping technology from Hilchenbach, presented a workpiece clamping system that enables positionally flexible and clamping without deformation. The jaws can move independently of each other and adapt themselves in the clamping area to any position of the workpiece to provide optimum clamping and support. As soon as one of the clamping jaws makes contact with the workpiece, the second jaw then moves in and presses against it. The jaws are then clamped and the required clamping force is set. This design allows components to be aligned to internal contours, for example, and then clamped. In addition, deformation is prevented by adapting the clamping point to the position of the workpiece when clamping series of long workpieces such as profiles, rails or strips.
Machine tools – smart and innovative
Spinner Werkzeugmaschinenfabrik GmbH, Sauerlach, Germany, exhibited its 5-axis VC1650-5A precision machining centre, a compact machine with a large working area in which workpieces up to 800 x 800 x 800 mm can be machined in five axes. According to Spinner, despite the size of the machine, its relatively small space requirement is achieved, among other things, by means of a new cover design for the guideways. The installation space is thus 30 per cent smaller than comparable machines. Depending on the application, the machining centre can be configured with a spindle for heavy-duty machining at up to 464 Nm torque or with a spindle for high-speed machining at speeds of up to 18,000 rpm.
Index-Werke GmbH & Co. KG, Esslingen, Germany, set up its CNC multi-spindle automatic MS16C Plus lathe for the METAV 2018 visitors. Six fluid-cooled motor spindles integrated in the spindle drum form the core of this flexible machine. This enables infinitely variable speed control which can be adapted for any spindle position, even during cutting. Driven tools and C-axes enable process steps such as oblique, transverse or eccentric drilling and contour milling. The new Index C200 sl, which is based on the Siemens S840D Solution Line control system, is used as the controller. It is operated via a touchscreen. The iXpanel operating system allows all data required by the operator, such as drawings, order documents, machine documentation or maintenance intervals, to be displayed on the screen.
Citizen Machinery Europe GmbH, Esslingen, in Germany, displayed an innovative process to improve chip breaking while turning long chipping materials. When plastics, brass or free-cutting steel are machined without the addition of chip-breaking alloy components such as lead, the turning process often results in long shavings and coils. This is remedied by Citizen’s Low frequency vibration cutting (LFV), in which the chips are broken in a controlled manner through oscillating tool movement in the feed direction. The process can be used for almost all part geometries and different materials and can eliminate the need to remove long chips while the machine is at a standstill. The Citizen machines incorporate drives and spindles specially designed for oscillating motion and the resulting loads.
Sauter Feinmechanik GmbH from Metzingen in Germany, presented the Sauter Torque Drive, a tool turret with an electric motor integrated in the tool disc for the tool drive. This direct drive system makes it possible to drive the tools directly at speeds of up to 12,000 rpm without an intermediate gearbox. This prevents transmission-related friction losses. The Direct Drive product group is supplemented by Torque Drive which allows milling tools to be driven with an extremely high torque of 85 Nm at 20 per cent duty cycle without the need for gear reduction. The high torque is transmitted via a specially developed coupling, but VDI tools can also be used up to a torque of 63 Nm. A water sensor also registers the input of cooling lubricant into the turret and contributes to process reliability by issuing appropriate warning messages.
Bimatec Soraluce Zerspanungstechnologie GmbH, Limburg an der Lahn, Germany, showcased its developments in the field of intelligent machines. The patented DAS+ system, which is also available for bed, milling and drilling centres, can be used to eliminate chatter vibration, regardless of its cause, through the targeted analysis and overlaying of vibrations. According to the manufacturer, this system can increase cutting performance by up to 300 per cent and reduce production time by up to 45 per cent. The spindle speed can also be automatically controlled using the SSV (Spindle Speed Variation)function. Other systems from the intelligent machine sector include Adaptive Control technology which helps reduce machining times and facilitates unmanned production through automatic feed control. The DBS dynamic ram balance system ensures constant straightness of the milling slide axis (max. 0.02 mm deviation over the complete travel path), regardless of the respective weight of the mounted milling head, cross slide or spindle sleeve. These three technology options are available for the travelling column milling and drilling centre exhibited at METAV which has a travel range of 8,000 mm x 2,200 mm x 1,300 mm. Applications include the commercial vehicle industry, tool and mould making and general engineering for the machining of medium-sized components.
Yamazaki Mazak Deutschland GmbH, Göppingen in Germany, presented its horizontal 5-axis HCR-5000S machining centre, a machine tool for the high-speed machining of aluminium. Developed for the efficient machining of small and medium-sized aluminium components, for example for the aerospace and automotive industries, the machine features a high-speed spindle with a maximum speed of up to 30,000 rpm. High feed speeds (rapid traverse speed: 60 m/min) with acceleration rates of up to 1 G in the X and Y axes as well as efficient chip removal via the machine table (which can be pivoted around the A axis) and a central trough for removal of large chip quantities enable short cycle times and high productivity.
Heidenhain, based in Traunreut, Germany, provided a meeting place for TNC users – with its own stand at the TNC Club. Specialists were able to obtain information and compare notes with other experts and colleagues. For Industry 4.0, Heidenhain is offering its StateMonitor, a straightforward software solution that records the operating states of production machines and displays them on a web-based user interface. This allows data to be retrieved from any device with a web browser. In the event of a malfunction, notification can also be sent by e-mail or SMS, allowing the operator to react as quickly as possible.
Focus on modern tools
Paul Horn GmbH, Tübingen, Germany, presented tool systems for hob peeling of internal gears, splines and internal profiles that help achieve significantly shorter process times than with gear shaping. The tools can be used in specially optimised turning/milling centres, thus allowing the turning and gear cutting operations to be carried out in a single clamping. Up to diameters of 20 mm, the tools are available as solid carbide tools; from cutting circle diameters of 20 mm, as tools made of HSS with an exchangeable carbide head.
Recently added to the range are the milling and turning tools for carbide machining, presented at EMO Hanover 2017. The CVD-D coated tools permit close contour machining of carbide, and offer greater flexibility and cost advantages compared to grinding or eroding.
The Paul Horn product portfolio is complemented by the high-speed SFI Toodle spindles. A turbine drive operates the spindles via the cooling lubricant at a pressure of 10 to 60 bar and 40,000 to 75,000 revolutions per minute. A model which runs on compressed air (3 to 7 bar) and reaches speeds of 35,000 to 60,000 rpm, has also been added to the range. The high-speed spindles can be used with conventional tool holders.
Mapal Dr. Kress KG, Aalen, Germany, introduced a multi-bladed reamer in the form of the HPR400 plus, which allows the indexable inserts to be changed easily on the customer’s premises. Costs for transport to the manufacturer, for stock in circulation and for reconditioning can be reduced as a result. The inserts have four cutting edges, permitting optimum use of the cutting material. The very high accuracy of the insert seat of ± 1 µm in combination with the tolerance of the indexable inserts of ± 2 µm eliminates the need to adjust the tool after changing the worn cutting edges, thus significantly reducing unit costs. According to Mapal, the reamers are available from diameters of 50 mm.
Ecoroll AG Werkzeugtechnik from Celle in Germany, manufactures tools for surface finishing; it presented new developments and refinements of burnishing and deep rolling tools at METAV. In the future, the mechanical burnishing and deep rolling tools will feature a system for digital and wireless determination of the rolling force. It has also developed a new tool concept for deep rolling gears. The groove flanks are processed using multiple rollers arranged one behind the other. The fatigue strength of the gears can be increased by changing the rim zone properties. As a new product line in the Ecoroll range, ECOpeen presented tools for rim layer strengthening by hammering. The tools are designed to be used in CNC machining centres, lathes and robots and to transfer high impact energy recoil-free to the component surface. The impact frequency can be set via the drive speed. The tools can be adapted to the respective machining tasks using exchangeable tool inserts.
News from the Moulding Area
Companies in the tool and mould making industry presented their product highlights in the Moulding Area. The use of new materials and innovative tool concepts promise greater precision and increased productivity.
Hasco Hasenclever GmbH + Co KG, Lüdenscheid, Germany, for example, presented its quenched and tempered tool steel 1.2714HH as a new addition to its extensive range of standard modular components. According to Hasco, it exhibits particularly good dimensional stability and toughness, but also optimised machining properties at a maximum hardness of 400 HB. Further advantages include its high dimensional stability and wear resistance, superior polishing and etching properties as well as the possibility of nitriding and coating at temperatures up to 510 °C.
Another new product from Hasco is the type Z920 manifold block which can be used for the simple configuration of flexible cooling circuits. Central inflow/outflow makes it possible to use shorter hose lengths which, besides creating a clearer arrangement, increase operating and work safety and save energy costs.
Knarr, based in the German city Helmbrechts, has been designing, constructing and manufacturing tools and moulds for moulded plastic injection parts for years now. A special challenge is the production of parts with undercuts or threads. Knarr offers tools with a so-called collapsible core in order to remove threaded parts from the core, The central core is drawn together after injection moulding in order to be able to push the parts away from the tool in the shortest possible time. These tools are specially designed by Knarr for individual articles; they enable cycle times to be reduced significantly.
Meusburger from Wolfurt, Austria, is a manufacturer of high-precision standard parts such as plates and rods for tool and mould making. Heat treatment for stress-relief annealing guarantees particularly low warping levels in the processing of these standard parts with an achievable warping level of over 90 per cent. Zero-point clamping system holders can be positioned and bolted directly to the plates and rods with maximum accuracy. An assembly table was showcased in which the heavy mould elements can be moved with no great effort using an air bearing.
Focus on measurement technology and quality
METAV also showcased numerous innovative products for the precise measurement of tools and components – and not only in the Quality Area.
Zoller, the testing and measuring technology specialists from Pleidelsheim in Germany, exhibited their genius 3s universal measuring machine for cutting tools. This permits the fully automatic measurement of tools via its five CNC-controlled axes. The measuring sequences and tool characteristics to be measured are defined in a photorealistic input dialogue. For example, characteristics such as cutting, clearance or twist angles can be selected and measured using checkboxes. But also the groove and chip space can be scanned without contact.
Renishaw GmbH from Pliezhausen in Germany demonstrated its Equator testing device. This is an option for process monitoring in the production environment, in which the repeatable accuracy and thermal insensitivity of workpieces can be tested. The flexible testing device can be loaded both manually and automatically. The data can be transferred directly to the machine after the test procedure to update the tool offsets.
Keyence Deutschland GmbH, Neu-Isenburg, Germany, presented a series of innovative solutions in the field of microscopy and measurement technology. The IM-7000 digital measuring projector now has a significantly larger measuring volume thanks to an object table measuring 250 x 250 mm. In just seconds it can measure the contour of objects and up to 99 defined characteristics, check them for dimensional accuracy and issue them in test and analysis reports. A newly developed photoelectric proximity switch also makes it possible to detect features on contours that could not previously be detected with conventional lighting. The object is touched by the probe with a very low contact force of only 0.015 N; this allows even relatively light components to be measured without clamping on the stage.
The image-guided 3D coordinate measuring machine from the XM model series now allows even larger components to be measured using a movable and swivelling table. The capturing field of view of the infrared probe is 600 mm in width and 380 mm in height, while the repeat accuracy is given by the manufacturer as ±3 µm. An integrated camera in the probe supports the measuring process by means of augmented reality. The operator is shown measured values on the display of the real component, or remaining measurement points to be measured are displayed.
Summary
Numerous forward-looking technological highlights and new developments which are used in a wide range of innovations were on display at METAV 2018. These included, for example, new additive manufacturing applications and developments in tool and mould construction which are used to create improved geometries and arrangements of tool cooling channels. The resulting design freedom can also be exploited in the development of precision tools.
METAV 2018 also showed that numerous companies are continuing to explore digitalisation and the constant availability of machine data. The cloud-based software solutions which were presented are designed to enable easy and secure access to the data at any time. Digitalisation also increases productivity in the fields of medical technology, quality assurance and measurement technology, for example through more effective measurement processes. In combination with technological developments, digitalisation and networking can further raise flexibility and precision levels in the future and thus ensure the high component quality which is required above all in the metalworking industry, while also yielding optimised productivity.
Author: Jan Nickel, M.Sc., Institute of Machining Technology, Technical University Dortmund, Germany, Tel. +49 231 755 6426, e-mail nickel@isf.de