When laser lettering disturbs concentricity
Even though the digital transformation is increasingly revolutionising all areas of the METAV 2018, one thing is certain: even today’s digitalised metalworker is still earning his money with a blade. The crucial considerations applying for micro-tools used in tool and mould construction are outlined by the Baden-based tool manufacturer Stefan Zecha, Managing Director and Managing Partner of Zecha Hartmetall-Werkzeugfabrikation GmbH from Königsbach-Stein. The company will be one of the exhibitors in the Moulding Area.
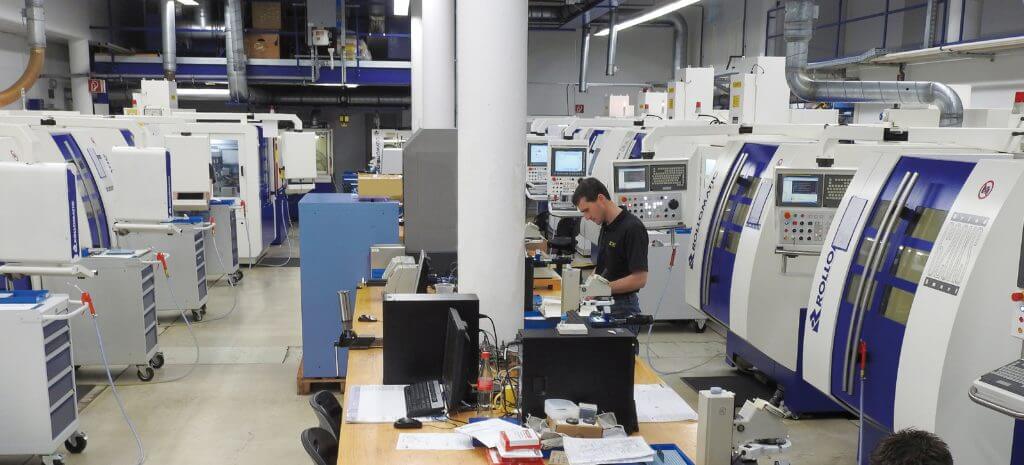
Stefan Zecha, your customers include tool and mould manufacturers: what requirements does this sector stipulate for the machining tools involved?
Stefan Zecha: We produce high-precision tools with micrometre accuracy, for which tool and mould manufacturers insist not only on high reproducibility, but also on fast and punctual deliveries.
For what is known to be a very quality-aware sector, how do you demonstrate compliance with quality stipulations for your drilling bits, milling cutters, thread-whirlers and reamers?
Stefan Zecha: For over ten years now, we have been lasering a number onto every tool, making it possible to trace who manufactured it when under what conditions from what hard-metal blank, and where the relevant report on the manufacturing process and the measurements concerned has been filed. Using what is called the Life Number, a tool can thus be unambiguously identified even years after a customer’s order was placed. We inscribe it on the end of the shaft, and not on the shaft as others do.
Why don’t you inscribe the Ident Number on the shaft itself?
Stefan Zecha: Tool and mould manufacturers insist on optimal concentricity characteristics for their tools, which a lasered shaft cannot supply, because the surface is then no longer entirely smooth. Due to the stringent requirements involved, by the way, we manufacture all our shafts ourselves, because it’s at the shaft that high precision begins.
What’s your recipe for success?
Stefan Zecha: High quality is assured by our rigorous purchasing policy. We always buy our hard-metal from the same vendors. So we will never, ever order hard-metal anywhere in the world for reasons of cost. When it comes to coatings, too, we stick to long-standing partners, working closely together with their R&D departments. But apart from the coating, the production operations are otherwise handled in-house with high vertical integration. This is why we do our own grinding as well. A tool with a diameter of one millimetre or less will not forgive any errors in the thousandth-of-a-millimetre range (µm).
One of your specialities is edge preparation, whose precision is crucial in determining the subsequent success of the machining operation: how precisely can you get the cutting edges into the shape you want?
Stefan Zecha: We can prepare them precisely to an accuracy of 0.5 to 0.8 µm, which is essential for guaranteeing consistently high quality.
Why when it comes to graphite machining do you work together with a diamond coater, a machinery manufacturer and an electrode producer?
Stefan Zecha: More and more often nowadays, we not only have to supply the tool, but increasingly keep an eye on the entire process as well. This includes determining the cutting data, for example. These three firms are in their different ways closely involved with the entire process chain. When it comes to coatings, particularly, we attach great importance to collaborating with other companies, since nowadays every year brings new coatings that we have to take on board. So we test all the coatings concerned very rigorously before we then use particular coatings on our tools for around three to five years.
What role do the METAV and the Moulding Area play for you?
Stefan Zecha: I regret that for fairs on this topic, especially, there’s a definite southward trend. So I’m delighted that with the Moulding Area the METAV has devoted a separately themed section to tool and mould construction.
What will you be showcasing at Düsseldorf in terms of innovations for tool and mould manufacturing and other sectors?
Stefan Zecha: We will be exhibiting ball, torus and shaft cutters, which – thanks to rigorous machining of the cutting edges with laser technology (R = 1 µm) and the special
blade geometry involved – significantly reduce the cutting forces and the amount of heat generated. In Düsseldorf, we shall here be showcasing a specially developed option for copper electrodes.
Das Interview führte Nikolaus Fecht, specialist journalist from Gelsenkirchen