Design or non-design: form and function follow ergonomics and operator language
What role does design play nowadays in machine tool manufacture? Does the principle of “form follows function” still apply – or is function sometimes being downgraded in perceived importance in favour of an aesthetically pleasing form? Besides upgraded functionalities, the METAV 2018 in Düsseldorf will also be spotlighting some eye-catching design highlights.
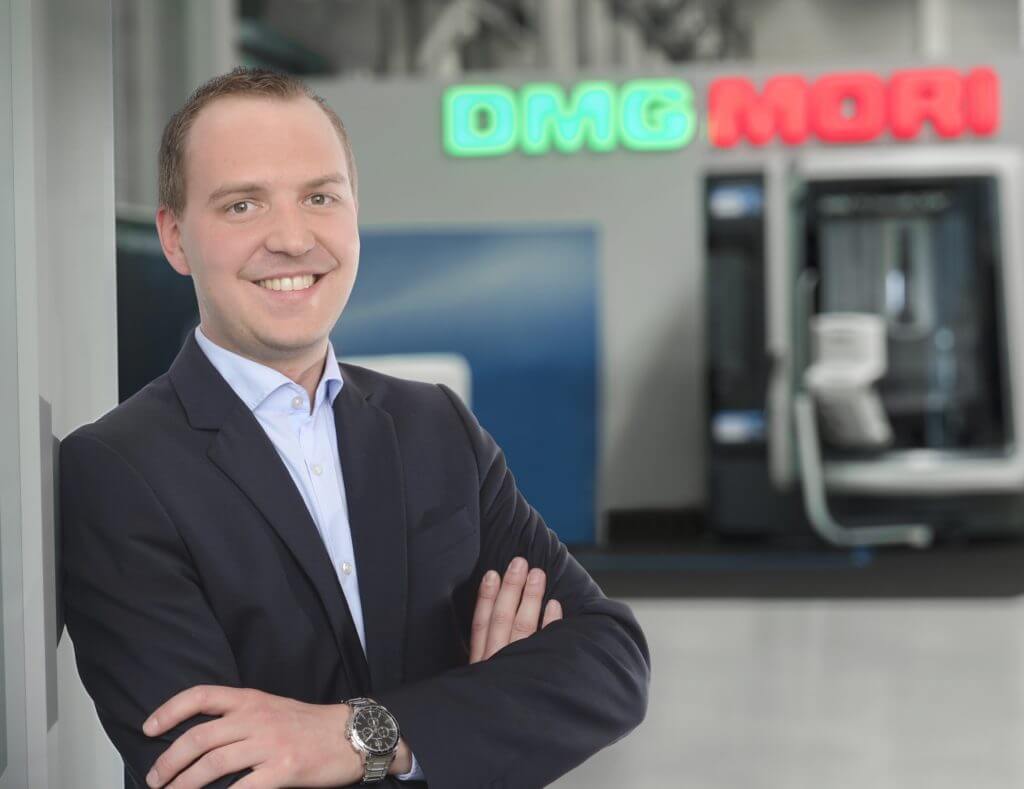
“Design is more than ever being perceived as highly significant in machine tool manufacturing, and is a preferred option for differentiation,” says Philipp Kriener, Manager Corporate Design at Gildemeister Beteiligungen GmbH, Bielefeld: “For example, at the EMO Hannover 2017 we premiered our automation solutions in our new Vertico design. The vertically arranged elements, with their characteristic triangular pattern, are inherently striking, and nonetheless constitute a harmonised whole with our machines. In our design work, we make no concessions in favour of form – a good design is primarily tasked with providing a functional added value and reflecting the upmarket quality of our products for the outside world to see.”
Design as a reflection of inner quality
The influence of design, he continues, is at DMG Mori particularly significant at the human-machine interface. Design makes a vital contribution for the user, enabling him to perform his work sequences at high efficiency in an ergonomically designed environment. For example, the configuration of doors and hatches is given due attention during the design phase, which simplifies regular maintenance routines and helps to extend product lifetimes.
Design’s contribution towards product optimisation in a networked production operation is elucidated by the expert as follows: “Coherently harmonised workflows – even on different terminals and machines – provide us with options for integrating processes and thus rendering them leaner. With the aid of software design, these invisible work sequences are visualised for the user along the entire process chain. Thanks to appropriate design of the products and the operator interface, we offer the user a holistic experience subsuming haptic, visual and action-related perceptions.” In terms of the human-machine interface (HMI), particularly, he continues, networked software solutions create new options for involving the user in the process to optimum effect.
In order to harmonise the disparate requirements of design, production and the user, the “design thinking” approach is adopted. The focus here, besides assembly- and production-friendly design, is primarily on the needs and ergonomic requirements of the user in his work sequences. To quote design expert Philipp Kriener: “For creating our machine tools, we embrace the principle of sustainable design – in other words, even after years have passed, it still has to communicate modernity and innovation at the customer’s facility. For instance, we’re currently developing our new ‘stealth design’, where all surfaces, joints and edges interact to constitute a uniquely distinctive design.”
Design is of major importance for human-machine communication as well. DMG Mori, for example, with its consistent ‘user experience’, is creating a user interface that leads the operator through the processes, and thus offers a major contribution towards product and process optimisation. The aim was through good design to guide the user in the operator control environment so as to ensure that he can perform all worksteps intuitively. “With the progressively closer merging of hardware and software,” says Philipp Kriener in conclusion, “we shall in future be focusing even more closely on the control console. Very soon, for example, we shall already be able to do without additional control panels at automation solutions, and integrate them into the operator’s console”.
Ergonomics are a key constituent of all machinery designs
The importance of design for ergonomics at the human-machine interface is elucidated by Dr.-Ing. Jürgen Walz, Development Director at Gebr. Heller Maschinenfabrik GmbH, Nürtingen: “Operator controls, operator control height, lighting, noise, dusts and liquids are the typical parameters that present-day machinery design is tasked with satisfying. Whereas in the past ergonomics covered only operator control of the machine, nowadays software ergonomics are gaining steadily in perceived importance.”
For this purpose, when creating a new series of machines an operator control philosophy featuring new hardware was developed. Operator control is handled entirely by multi-touch screens. This means that many functions implemented in the past using hardware can be designed using software. In order to improve operator control ergonomics, the console was fitted with a double articulated arm, which can be viewed from both the loading and operator control sides.
Ergonomic maintenance is likewise a paramount consideration for machinery owners. The centralised maintenance display at the control console visualises the machine’s status. For maintenance work, says Dr. Walz, this means “that a ‘small blood count’ is promptly available, which minimises the diagnostics and service work involved and the incidence of standstills”.
Design as a symbiosis of multiple optimised functions
“Form follows function” – “For us”, emphasises Martin Rathgeb, Technical Director of SHW Werkzeugmaschinen GmbH, Aalen, “this principle still applies”. Good design, he believes, is a symbiosis involving a multiplicity of optimised functions: technical, ergonomic, safety functions, handling, emotional, communicative or light-related functions. The operator with his needs is gaining progressively in perceived importance even during the machine’s development stage, which means: design not just for design’s sake, but always with tangible benefits for the user.
To quote Martin Rathgeb: “We want to build ergonomically optimised machines that look good and make the operator feel he’s duly appreciated, since satisfied employees are effective, and utilise the machine’s performative capabilities to the full.” Design, he continues, underlines technological leadership and innovation, reflects the innovative technology in the heart of the machines, creates an identity distinctively different from competitors, enhances visual attractiveness and interest in the product, generates brand awareness, elicits an emotive response, and creates trust.
The influence of design on function is well exemplified not least at the control console of a machining centre by SHW. The innovative conception of the workplace, and the concomitant respect for the employee, the human involved in the work process, and his resultant identification with the product, were paramount considerations at the design development stage.
Martin Rathgeb’s response to the question of how design contributes towards product optimisation in a networked production operation is this: “The vision of a fully automated production operation demands holistic functional concepts where not only can design and manufacturing data be transferred directly to the machining centres, but where harmonised operator interfaces, designations and the ‘machine’s look’ also predominate, with high recognition value for the user, so that all interconnected machines can be reliably, intuitively and efficiently operated.” This future requirement can be met only by a ‘harmonised design concept’ that is defined by the function desired and thus also has to be the basic idea underpinning the entire development process for the machine tool. In this context, it is immensely important to take ergonomics into due account, “since when in future production processes run in a fully automated mode, the quality of the ergonomics involved is the crucial aspect, differentiating the performative capabilities of the machines concerned”.
Human-machine communication is progressively being transformed into the category of digital solutions, such as 3D simulation of machining in real-time, thus rendering processes visible that in practice are not visible by reason of the coolant flow. The requisite monitors can be functionally integrated into the machine only by means of good design.
Operating systems, too, will have to be designed for more convenient simplicity, with intuitive user interfaces modelled on solutions from the field of consumer goods, in order to meet the expectations of the “smart-phone generation”. Martin Rathgeb predicts: “Reaching a destination with one or just a few clicks, and the use of 3D depictions rotatable in virtual space of the workpieces to be machined and prepared, are already paramount factors in the development specifications for the next generation of machines designed to ensure smooth human-machine communication and reliable, cost-efficient production.”
At the METAV 2018 in Düsseldorf, SHW will be “spotlighting our machining center in a new design” – with development work that prioritised supporting the operator in his daily work with and at the machine. Martin Rathgeb explains: “And we will also be showcasing the latest solutions in the field of digital production process support, like our condition-monitoring-system, our camera-aided workpiece alignment and SHW-data-glasses”.