German Machine Tool Manufacturers Tackle Industry 4.0 Together
The VDW presents the industry initiative of the German machine tool industry for networked production for the first time at the EMO Hannover 2017.
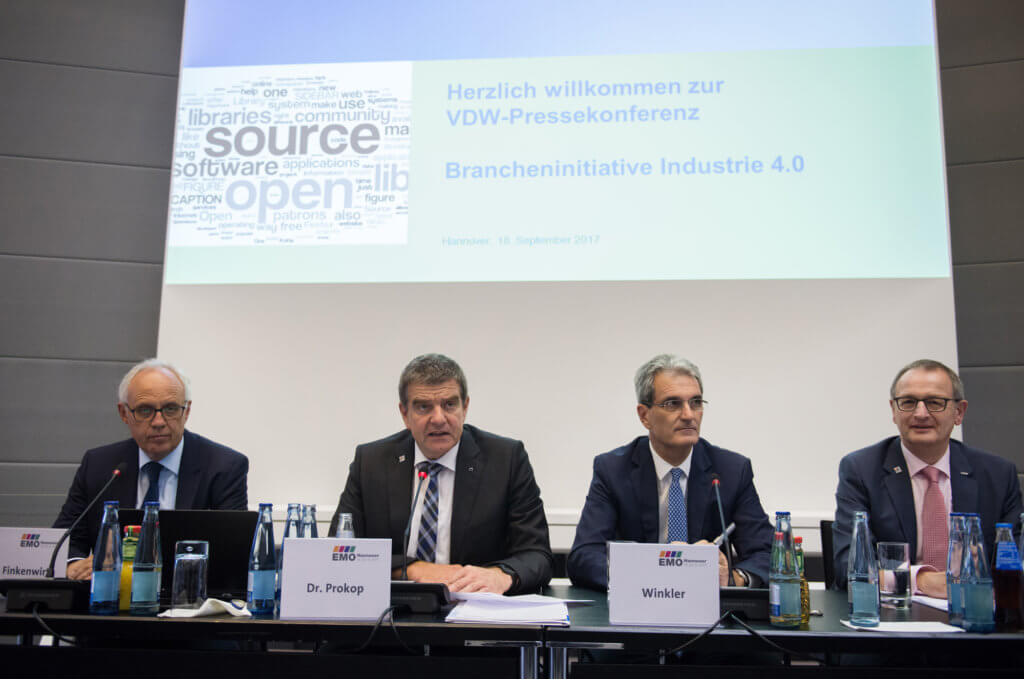
Brancheninitiative Industrie 4.0
The VDW (German Machine Tool Builders’ Association) presents the industry initiative of the German machine tool industry for networked production for the first time at the EMO Hannover 2017. “ The aim is to develop a standard for linking a huge range of disparate machinery control systems to a shared interface (a connector), and create the requisite software,” says Dr Heinz-Jürgen Prokop, Chairman of the VDW on the occasion of the Association’s press conference. A core team is involved in the first phase of the project with the companies DMG Mori, Emag, Grob, Heller, Liebherr-Verzahntechnik, United Grinding, Trumpf and the VDW.
The VDW Executive Board decided on this project in spring of this year, because there has not been a standardised and consistent solution so far. With the planned standard, data is to be read from different machines with different controllers of many generations and transported into infrastructural systems or the cloud in a standardised data format in order to analyse it and use it for optimizing production tasks. “This is the basic requirement for the success of Industry 4.0, especially in medium-sized firms,” states Prokop.
For the machinery manufacturers, too, this would be a significant easing of their workload, enabling them to shed tasks that although they urgently need to be completed are nonetheless outside a manufacture’s core remit and entail high costs. The standard being targeted thus frees the individual VDW member from timeconsuming work on infrastructural issues. Not least, this creates an open system that offers an urgently needed degree of independence and flexibility. “Unfortunately the most recent developments showcased here at the fair also show that in the case of control systems, particularly, the trend toward proprietary ecosystems is still ongoing,” says Prokop. “We intend to counteract this, and are therefore endeavouring to establish a development partnership with the control system manufacturers in particular, in order to render the VDW’s planned specification usable on the broadest possible scale.”
Initial results expected at the beginning of 2018
The following aspects are to be implemented first of all during the course of the project:
- Joint development of an interface specification
- Implementation of a so called connector stack that translates signals from different controller interfaces according to OPC UA (OPC Unified Architecture).
- Implementation of a gateway that allows a secure connection to different IT systems and clouds on the basis of the OPC UA data structure via standard protocols
The VDW had already started developing a so called companion specification in 2013. It has been published since July of this year by the standardisation organisation OPC Foundation. Therefore, the project team can start with joint expansion of this companion specification immediately after the EMO with shared expansion of this interface specification. Our goal is coherently harmonised networking of the production operation; the vehicle for this purpose is OPC UA, and the energy that drives us forward is the jointly specified constant component of the data that we have to exchange for this purpose,” emphasises Prokop.
Results should be available in the first quarter of 2018. The aim is the presentation of a basic data record that can then be commented on publically in the context of the usual standardisation procedures. The requirements are to be specified, the basic specification programmed and around 30 data records described.
When the data is available in a standardised format, the interface to the “rest of the world” still has to be defined. There are already standardised protocols for this, similar to the ones known for the transfer to an Internet browser by means of HTTPS. However, access to this data must be regulated. It requires authentication and access protection. The data must also be precompressed and buffered where applicable, because raw data in particular cannot be sent through the network in high resolution and in real time without having an adverse effect on the machine performance. All these functions are taken over by a gateway that will be specified and implemented as a second project phase.
The third project phase finally deals with the test of the developed solutions with different VDW members. “Furthermore, we will analyse which providers of infrastructure and cloud services most likely cover the need of smaller and medium-sized machine manufacturers in particular,” says Prokop as he describes the further course of action. If the data interface represents the bottom end of networking, then there must be a technological platform at the top end that is as standardised as possible, for which each machine manufacturer can in turn develop its own smart apps. That would be part of the core business of every provider in the future. “This means the provider could deploy his expertise to optimum effect and differentiate himself from the competition, says Prokop.
Sectoral cooperation is the right way forward
The machine tool industry and the VDW are breaking new ground with this cooperation. On the one hand, it is obvious, because a lone wolf would quickly reach its limitations. Without a generally valid standard, the solutions of Industry 4.0 will also find it difficult to find market acceptance and thus rapidly increasing dissemination.
“It is our conviction that it is good and correct to throw any reservations against cooperation overboard, adopt the principle of sharing knowledge, profit from it and work on a common solution, ” summarises Prokop. With the results, even medium-sized firms will be capable of acting very quickly.
Downloads
Pictures
Documents