“Grinding community to meet in Stuttgart”
Stuttgart is set to become the international hub for grinding technology and superfinishing from 17 to 20 May 2022 – which is how the GrindingHub, organized by the VDW (German Machine Tool Builders’ Association) in cooperation with Messe Stuttgart and Swissmem, defines itself.
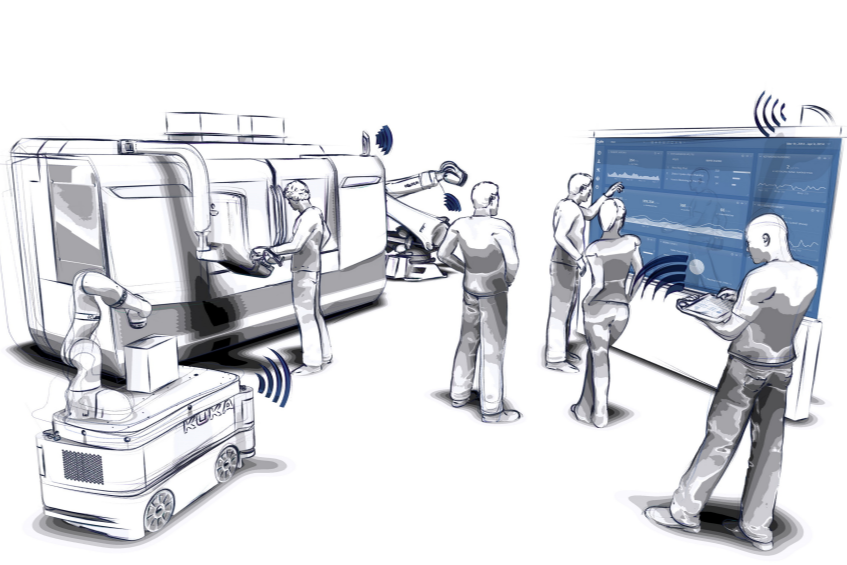
GrindingHub 2022: Dialog between top researchers and high-tech industry
Prof. Berend Denkena, Managing Director of the Institute of Production Engineering and Machine Tools (IFW) at Leibniz University Hannover and spokesperson for the General Committee of the WGP (German Academic Association for Production Technology), and Dr. Sebastian Barth, Senior Engineer and Head of the Technology Planning and Grinding Technology Department at the Laboratory for Machine Tools and Production Engineering (WZL) of RWTH Aachen University, explain why a visit will be more than worthwhile.
What motivates renowned university institutes like yours to participate in the GrindingSolutionPark?
Sebastian Barth: A key reason for us is the professional exchange between top-level research and the high-tech industry. The joint booth in the GrindingSolutionPark provides a great opportunity to discuss how our current research can be implemented in the industrial environment. My team and I are particularly motivated by the opportunity to discuss current challenges facing the industry. This will allow us then to target our research more effectively.
Berend Denkena: We are motivated by the opportunity to identify potential areas for future research and networking possibilities between science and industry. Talking to company representatives and presenting our current research projects, innovations and cooperation opportunities to them provides us with a good opportunity for this.
How important is grinding technology for you?
Berend Denkena: It has long been a core issue at IFW and one which has grown in importance over the years. This is also reflected in the staffing levels. There are now 15 research assistants working on grinding technology, making it the largest working group. The topics range from tool and cut-off grinding through to application behavior and the manufacture of grinding tools. End-to-end digitalization of the grinding process and grinding tool manufacture play key roles in our research.
Sebastian Barth: We accord grinding a great deal of importance, since in many process chains it is one of, if not the primary factor which decides the final functional properties of the components. The WZL has many years of expertise in surface and profile grinding, tool grinding, external cylindrical grinding (between centers and centerless), centrifugal and flow grinding, and robot-guided vibratory grinding. The primary focus is on four aspects: economical machining of innovative materials, targeted and integrated process design and optimization, and the digitalization of grinding processes using sensor technology and sophisticated algorithms.
What does the IFW see as the current trends?
Berend Denkena: There is strong demand for energy and resource-efficient processes – in grinding tool production, for example. Our approach here is to design energy-optimized sintering processes. The secret is to adjust the energy-intensive sintering parameters such as dwell time and heating rate without changing the abrasive coating properties.
We also use additive manufacturing processes. The IFW uses simulation to design tools deterministically. This means that the eventual 3D-printed result corresponds exactly to the design specifications. We demonstrate how it works in practice based on an application example. For those interested, it involves setting pattern grinding beads for wire grinding.
Simulation is a crucial factor in the digitalization of the entire manufacturing process. In Stuttgart we will be using grinding tools to show how manufacturing can be made more flexible and optimized by simulating the complete process chain.
But we also use digitalization for specific solutions. A typical problem in tool grinding is so-called displacement. Process forces push away the tool being manufactured, thereby reducing the potential accuracy levels. Visitors will find out how displacement during tool grinding can be compensated by intelligent process planning and the use of grinding spindles equipped with sensors. In cooperation with the machine tool industry, the IFW has succeeded in significantly increasing the accuracy.
How does the WZL view the role of digitalization?
Sebastian Barth: Digitalization now plays a major role in many areas of grinding technology. The data-based manual optimization of grinding as an isolated process is currently in great demand. I notice that industrial users are increasingly planning to use artificial intelligence (AI) methods to predict the outcome of a process in order to reduce quality variations. AI tools can also be used for predictive maintenance of grinding machines. Digital twins are also nothing new for the industry: they can potentially make products and grinding processes even more assessable and certifiable by combining process data and scientific models. Closer cooperation between industry and research institutions in the future will help to leverage this potential for grinding technology in Germany as quickly as possible.
What other trends are you monitoring?
Sebastian Barth: These range from the production of application- and function-optimized surfaces to the machining of innovative and difficult-to-machine materials such as fiber-reinforced high-performance ceramic matrix composites (CMCs) and nano-polycrystalline cutting materials. Another very important trend concerns process chains as an integrated whole, in which grinding technology often plays a decisive role. This is because process chains can only be comprehensively optimized if the effects of grinding technology on other (usually upstream) manufacturing processes are also taken into account. The WZL will be highlighting the latest production solutions at the GrindingHub.
How can grinding technology increase sustainability?
Sebastian Barth: The answer is: by combining different options, such as the use of bio-based cooling lubricants, data-supported and optimized integrated process, process chain and tool design, and employee training. We have expertise in all these areas at the WZL.
And what are you interested in seeing at GrindingHub?
Sebastian Barth: I’m looking forward to seeing machine innovations, new tool trends, cooling lubricant solutions and key research developments in the GrindingSolutionPark. Of course, I’m especially looking forward to the get-together with the ‘Schleiftagung’ (grinding conference) community, which will now be taking place at GrindingHub. The cooperation between the GrindingHub and the Schleiftagung, which we took over this year, provides an ideal basis for the future. The partnership combines the strengths of Germany’s high-tech industry and the latest research in the field of grinding technology in producing a joint response to current and upcoming challenges.
Berend Denkena: I have a similar focus to Sebastian. In addition to tool-related innovations, I’m interested in innovations in machine tools, such as solutions for complete machining and automation. But I’ll also be checking out the latest developments in lasering for tooling, such as the machining of ultra-hard cutting edges.
Many thanks to both gentlemen for the interview.
(Size: around 8,100 characters including blanks)
Author: Nikolaus Fecht, freelance specialist journalist, Gelsenkirchen
Background GrindingHub 2022 in Stuttgart
The first ever GrindingHub will be held in Stuttgart from 17 to 20 May 2022. It is the new trade fair and the new center for grinding technology. It is scheduled to be run every two years by the VDW (German Machine Tool Builders’ Association), Frankfurt am Main, in cooperation with Messe Stuttgart, and with Swissmem (Swiss association of mechanical and electrical engineering industries) as its institutional patron. Grinding is one of the top 4 manufacturing processes within the machine tool industry in Germany. In 2020, the sector produced machines to the value of 870 million euros. Almost 80 per cent were exported, with about half going to Europe. The largest sales markets are China, the USA and France. Germany, Japan and Switzerland head the list of top global producers. The grinding technology sector produced 4.9 billion euros worth of machines in 2019.
Texts and pictures to the GrindingHub can be found in the Press Section at:
www.grindinghub.de/journalisten/pressematerial/
You can also visit the GrindingHub on our social media channels: