Plug-and-play for factories
What if a machine could be virtually commissioned before it finally arrives weighing several tonnes in a factory? This is possible with a digital twin and complex computer simulations.
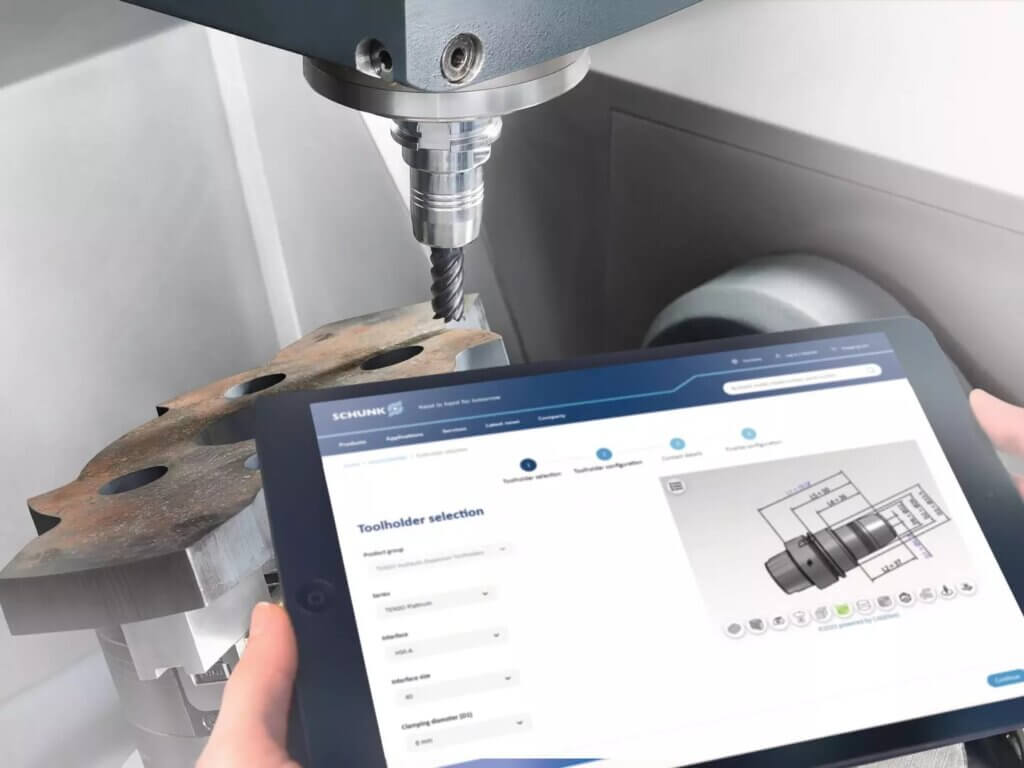
Digital twins and simulation raising efficiency to a new level
What if a machine could be virtually commissioned before it finally arrives weighing several tonnes in a factory? This is possible with a digital twin and complex computer simulations. A 3-D model shows whether the machine is smoothly integrated in the existing production environment: first plug-and-play, then plug-and-produce. NORTEC, Trade Fair for Manufacturers, which will be held in Hamburg from 23 to 26 January 2024, will present the latest state of the art and show what efficiency gains can be achieved.
Production managers are aware of the challenge. Production has been running smoothly for years. A new machine is now due to arrive. A large number of practical questions are raised. Will the new machine achieve the performance that is required for integration in the existing production environment? Can this machine communicate efficiently with other machines? A digital twin can provide answers to these questions. It is an image of the physical asset in a real factory and enables it to be simulated, controlled and improved.
3-D model instead of iron and steel
Computer simulations display their strengths when complex machines have to be integrated in an existing production line or a production hall. Olaf Sauer, who works at the Fraunhofer Institute for Optronics, System Technologies and Image Exploitation (IOSB) as the Deputy Head of Institute, Business Unit Automation and Digitalisation, explains how this functions. “Instead of waiting like in the past for the engineering company to deliver the machine and install it in the designated place in the production hall, a manufacturer can perform the following tests using a digital twin with the virtual machine: based on its dimensions and, if applicable, the movement space, will the machine fit into a production hall or rather a production line? Will the machine possibly collide with pipes or columns? Can the machine already be commissioned virtually, for example with a real control system, but not in steel and iron, but with an operable 3-D model?” A digital twin can also be used to clarify whether the machine meets the required cycle time and volume so that output is maintained along the entire line.
Artificial intelligence even before installation
According to Sauer, complex questions can also be resolved. For example, what signals are sent by the new machine? Can these signals be used to create models beforehand with the aid of artificial intelligence? The machine or system may even include a machine-readable self-description so that it is inserted and recognised, thus enabling a type of autoconfiguration. This is achieved through standardisation. Machine tool manufacturers are creating a USB standard type called umati for Industry 4.0 applications. This acronym stands for universal machine tool interface, i.e. a universal interface for machine tools. umati is based on the platform independent OPC UA Standard. It will, for example, enable machines and systems to exchange data through higher-level data processing in a secure and standardised way.
Digital twins must be customised for every individual case. “In our opinion, the application case is initially decisive,” said Sauer and raises some other questions which have to be answered depending on the utilisation purpose: What will a digital twin be used for and what is its objective? Will a digital twin only be used inside a company or will the submodels of a digital twin be exchanged with other companies? “It then comes down to its interoperability, i.e. whether the submodels are ‘understood’ by other companies,” said the holder of a doctorate in industrial engineering.
It is important to clarify what submodels are required for the application(s) and whether there are already standardised submodels which can be utilised, for example those from the Industrial Digital Twin Association. There should also be clarity as to which IT systems or engineering tools produce which submodels in which format, i.e. proprietarily or in open standards for example.
Digital twins as a free download
Special attention is paid to industry standards for digital twins. The technology group and NORTEC exhibitor Schunk SE & Co. KG, which has its head office in Lauffen am Neckar and produces gripping and clamping systems, is jointly promoting with other companies the further development of the digital twin as an industrial standard in a technology organisation, i.e. the Industrial Digital Twin Association. “Schunk offers digital twins as a free download for all standard catalogue products from its gripping system and tool holder portfolio,” said company spokeswoman Kathrin Müller in response to a request. “When integrated in the simulation environment, the production process can be run through without any risks and can be digitally optimised even before the machine is assembled and installed.
Schunk also recently started offering configurators for customised grippers, gripper fingers, clamping jaws and last but not least, tool holders. “This means that tailor-made products can now also be integrated in simulation before they are ordered. This is to test, for example, whether the workpiece can be ideally machined in terms of accessibility,” said Müller. The special aspect is that digital twins are also available ad hoc for these individual products in a few minutes. Schunk will present a selection of innovations from its clamping system portfolio at NORTEC. Visitors will also be able to see a demonstration of online tools such as the tool holder configurator called “easyToolholder” on Schunk’s stand.
What efficiency gains can a digital twin actually achieve in production in a company? “A digital twin offers a great deal of potential,” said Jakob Trauer, Senior IT Consultant at EM Engineering Methods AG in Darmstadt. This company is involved in the product development process as a system integrator. “For example, factory layouts can be virtually tested and optimized, maintenance operations can be predicted or quality costs can be reduced since a digital twin enables a virtual inspection to be performed with all automated countermeasures,” said Trauer, who previously worked at the Chair for Product Development and Lightweight Structures at the Technical University of Munich (TUM).
Reduce costs, increase turnover, improve sustainability
“In order to better describe these additional benefits in more detail, we developed a Digital Twin Value Framework in collaboration with the Chair for Product Development and Lightweight Structures at the Technical University of Munich (TUM),” said Trauer. This Framework links applications of digital twins with their specific potential. Its objective is to show the metrics with which digital twins can be quantified and how they can help to reduce costs, increase turnover and improve sustainability.
Simulations and/or digital twins are not limited to special branches of industry. “At present the majority of applications can be found in manufacturing industry, production and product development. In order to exploit potential to the full, it is also important to take account of the utilisation phase – the focal point here at present is research.”
Standardisation of data and models as the focal point
In order to transfer simulations and digital twins from research to industrial practice, some obstacles must be overcome. Trauer refers to an industry survey which was conducted in this respect by the Chair for Product Development and Lightweight Structures. “The most critical aspect was deemed to be the standardisation of data, models and exchange formats,” said Trauer in regard to the digital twin which is called DT for short in technical jargon. Trauer said that EM Engineering Methods is starting precisely there “by designing a suitable ‘DT-ready’ architecture together with our customers and also providing the necessary software solution modules for the backend and users.”
Digital twins are vital for Industry 4.0 and the digitalisation of production. “They can be used to test many aspects in advance before a product or a machine is manufactured. This saves time and money during commissioning, during testing and inside a company because the tests can be performed beforehand in the virtual world and possible errors can be ironed out digitally,” summarised the Fraunhofer scientist Sauer. “The later a defect in a product or a machine is discovered, the more expensive it is to rectify it,” said Sauer who has already implemented projects on lean production, core competencies and production control at customers such as Daimler-Benz, Adtranz and Volkswagen during his career at the Fraunhofer Institute. “Digital twins can also be used throughout the entire lifecycle of a product so that operational data is included in the planning of the next product generation.”
Fingerprint, ECG and foot scan
The term “digital twin” is often equated to simulation. That’s not quite correct as Sauer explained: “Simulation models may be part of a digital twin in the same way as a 3-D model of a machine, a digital product pass, a digital operating manual or a mechanically learned model of the normal behaviour of a machine may each form parts of a digital twin.” “All these are parts which represent certain aspects of a digital twin,” stated the Fraunhofer expert. “When applied to humans, the entire lifecycle is only one part of them; just like a passport, a fingerprint, an ECG, a birth certificate, face recognition or a foot scan so that a ski shoe can be adapted.”
A digital twin offers many advantages. It is already a permanent fixture in smart factories, especially in Germany. In response to the question whether Germany has a development edge over Japanese and American companies in regard to digitalisation themes in industry, Fraunhofer scientist Sauer answered with a clear and an unreserved “Yes”.
“With its strong subdisciplines Germany has everything which is necessary for digital twins,” said the scientist and practical expert, who has also already managed projects for companies from Asia and North America during his professional career. He lists everything which the industrial eco-system in Germany has to offer: developers and manufacturers of embedded systems, component suppliers, mechanical engineering companies, automation suppliers, system houses for product lifecycle management (PLM), manufacturing execution systems (MES) and enterprise resource planning (ERP), engineering and simulation service providers, and finally factory operators. “Germany has a complete ecosystem in order to successfully implement digital twins,” said Sauer. The trade fair NORTEC will open up a window to modern production technologies and show the efficiency gains that can be achieved with complex computer simulations in industrial production. Talks, workshops and discussions relating to current topics in production engineering, for example artificial intelligence, digitalisation and automation, will be held every day on two stages, i.e. the so-called auditorium and the Speakers’ Corner. The North German Simulation Forum and a workshop of VDMA Nord will also be held there.
((Length: 11,628 characters including spaces))
Author: Daniel Schauber, specialist journalist, Mannheim
Contacts
Fraunhofer Institute for Optronics, System Technologies and Image Exploitation (IOSB)
Dr. Olaf Sauer
Deputy Head of Institute, Business Unit Automation and Digitalization
Fraunhoferstrasse 1
76131 Karlsruhe
Germany
Tel. +49 (0)721 6091-477
https://www.iosb.fraunhofer.de/
Schunk SE & Co. KG
Kathrin Müller
Corporate Communications
Bahnhofstrasse 106 – 134
74348 Lauffen/Neckar
Germany
Tel. +49 (0)7133 103-2327
:em engineering methods AG
Jakob Trauer
Senior IT Consultant
Rheinstrasse 97
64295 Darmstadt
Germany
Tel. +49 (0)6151 7376-100
Daniel Schauber
Specialist journalist
Meerfeldstrasse 14
68163 Mannheim
Germany
Tel. +49 (0)170 2031976
Press Material
Exhibitor & Visitor Quotes (.pdf)
Pictures
Picture 01: Olaf Sauer IOSB
Picture 02: Jakob Trauer EM