Quality Area at the METAV 2018: processes digitally under control
The motivations for visiting the Quality Area at the METAV 2018 are many and varied, but at present plenty of visitors are primrily interested in one topic: how can the quality of their processes be improved with digitalisation? What small and mid-tier companies (SMEs), especially, should bear in mind is outlined by Andreas Wank, a research associate at the Institute of Production Management, Technology and Machine Tools (PTW) at Darmstadt University of Applied Sciences.
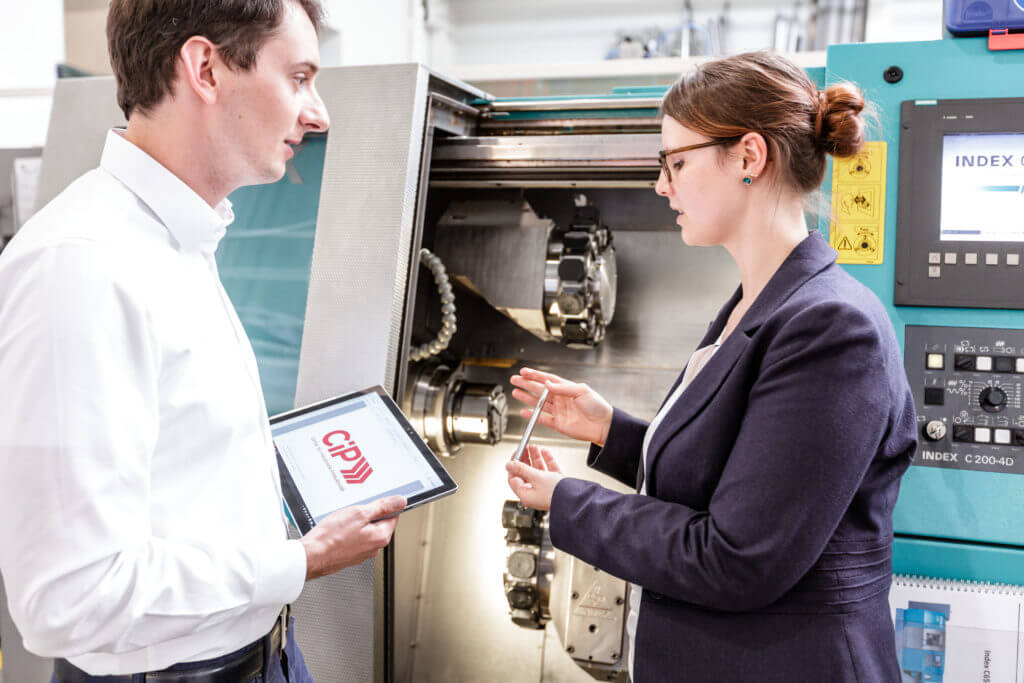
Large corporations sometimes have things easier when it comes to Industry 4.0, says Andreas Wank when explaining his field of research: they are more likely to have funds available to build a new greenfield factory in which they can without risk try out and introduce the new digital approaches involved. The situation is rather different at small and mid-tier companies, who in most cases will find it difficult to digitalise their existing brownfield production facilities. They should accordingly as a first step think very carefully about what specific ratios they wish to improve.
But Andreas Wank’s researches involve not only the field of digitalisation; as Managing Director of the new SME 4.0 Competence Centre in Darmstadt he also helps firms to safely embark on new digital approaches. “We tackle digitalisation primarily in terms of methodology,” he explains. “The focus here is not on replacing human work, but on complementing it.” For this purpose, he continues, it’s necessary in the digital process to automate activities that had hitherto been performed manually, like acquiring and entering measured data. Here, for example, the experts use their Value Flow Analysis 4.0 to identify cases of digital waste in manufacturing processes. These include digital media interruptions, where data are either not being acquired or not being forwarded. To quote Andreas Wank: “Often measured data are entered in the measuring computer by hand, but no regular analyses are performed and the information involved is not forwarded.”
Chaos cannot be digitally eliminated
First-time users should accordingly start by learning to understand their processes and stabilising them before proceeding to digitalise them. “It’s often not worthwhile entering directly into further digitalisation if you don’t know precisely what the processes look like,” explained Andreas Wank. “Things mostly go wrong when someone tries to eliminate chaos with digitalisation.” When analysing a company in Hesse with a high level of variant diversity, for example, his staff discovered that the information flow between Purchasing, Production Planning and Assembly was not functioning flawlessly. Digitalisation had already failed in the first step because no one properly understood the sequence of the information flow.
The experts at the Competence Centre supported the company in adopting a systematised approach: they first of all defined the ideal process sequence, so as to develop a digital support concept together with the staff.
Help for digital self-help
But there are also difficulties involved in bringing together existing, historically evolved IT systems to form a consistently harmonised digital concept. “The major problem here is developing a harmonised digital solution without stopping the operational sequence,” comments Andreas Wank. “It doesn’t help that in small and mid-tier companies this task is mostly handled by staff in addition to their everyday remits.” As an alternative to expensive management consultants, the Competence Centre offers help for digital self-help. It trains staff in methodological approaches, which before using them in their own plants they can then try out safely in the Process Learning Factory (CiP), or the new Energy-Efficiency Factory (ETA) at Darmstadt University of Applied Sciences.
One of the major challenges Andreas Wank encounters during his work is the chance that the information flow in companies will in future be handled without any paper at all. “Ideally, the entire process will be run digitally, since the products concerned will bring the requisite information with them,” he says with a view to the future. “Then the processes can be controlled or interlocked on the basis of real-time data. This would not be possible with a static paper-based approach.” He’s particularly interested in a digital view of quality assurance in conjunction with metalworking applications. To quote Andreas Wank: “This is why I see the Quality Area at the METAV 2018 as a very interesting source of ideas for us.”