“Real” smart automation
EMO Hannover 2025 showcases unique solutions with direct added value.
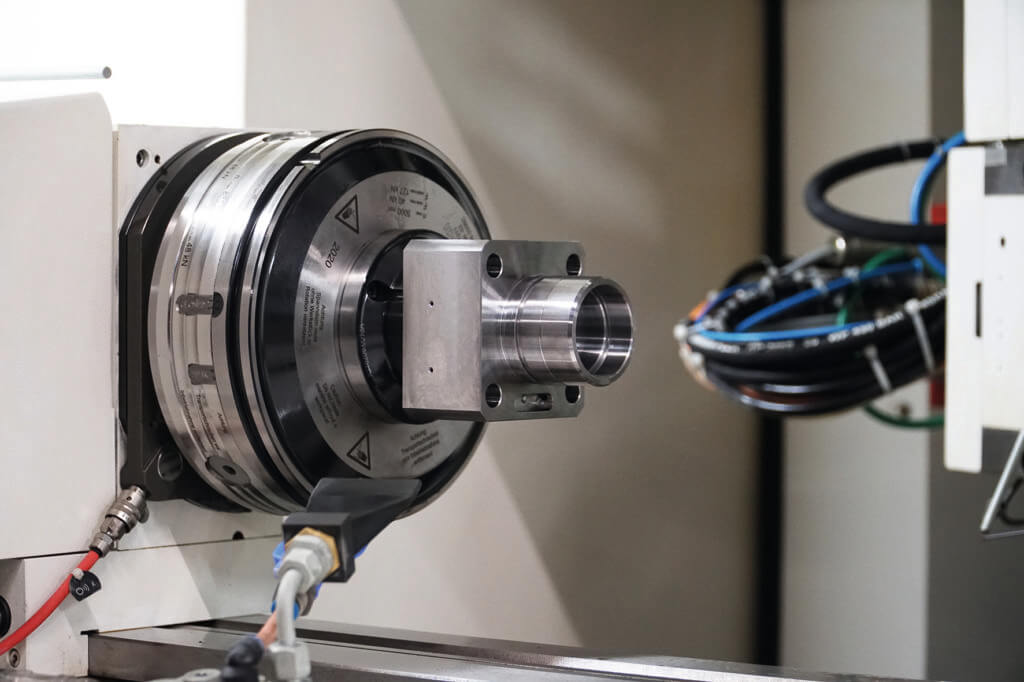
Modern manufacturing companies need automation and digitalization solutions to make their processes significantly more efficient and therefore globally competitive. There is no doubt about that. But which ‘real’ smart innovations actually provide a decisive productivity boost, unlike a ‘simple’ robot, for example? And what about the data world that is absolutely essential for this? Industry and research demonstrate the current status here. And the best thing about it: everything bundled together and much more will be on show again at EMO Hannover 2025 from September 22 to 26.
Briefing: “Guys, last-minute change of plan. Leo, can you please turn 1,000 ball sockets to size on the lathe during the morning shift? And Ria, please finish 200 gears on the machining center.” “All right, boss, no problem.” “Thank you. Have a nice evening.”
So far, so good. But what about tomorrow – when more and more baby boomers retire and there is a shortage of lathe operators and millers everywhere? It will be difficult without automation. But relax – there have long been solutions. Those who think and act flexibly and innovatively and are open to technology in these challenging times can score points – not only with customers, but also with employees.
Simple solutions that can be implemented quickly and cost-effectively with existing machines and personnel are in demand. The smart automation solution from Andreas Maier GmbH & Co. KG in Fellbach (AMF) is a flexible partial automation solution that boosts productivity outside and between existing machines. The loading cell with a particularly small footprint immediately increases productivity. Attached to existing machines, it ensures reliable and unmanned continuous loading and unloading. And thanks to the cleaning module, the parts arrive for the next stage of processing sparkling clean. Together with the intelligent door opening, there is not only potential for greater machine utilization, but also for a real productivity boost. In terms of the shortage of skilled workers, the investment sum and amortization, the solution from the Baden-Württemberg company is a real asset in machining production. Leo and Ria also welcome this… and at EMO 2025, the southern Germans will be presenting further innovations.
Clamping technology for the automation of very small batch sizes
Hainbuch GmbH from Marbach will also be demonstrating that fully automated, flexible production is possible for even the smallest quantities with a pioneering automated clamping device change for the company WTO in Ohlsbach. In the Smart Factory, the machines are set up completely autonomously by robots for each new order. With an accuracy of 3 μm on the workpiece with every clamping device change, unmanned production from batch size of 1 to 100 takes place around the clock. A chuck with axial tension is used for external clamping. The automation-capable chuck enables reliable clamping head changes in order to manufacture a wide range of workpieces and thus increase productivity. 18 clamping sets – consisting of a clamping head with stop – are automatically inserted into the chuck on the machine by robots.
Ten pre-equipped hexagonal mandrels for internal clamping are available in the grinding cell and in the turning/milling cell. The prepared mandrels are automatically converted via a quick-change interface. The interface used guarantees optimum power transmission and precision, resulting in an improved surface quality of the machined parts. Philipp Sommer, Head of Automation at Hainbuch, emphasizes: “Process-reliable clamping technology is the basis of all automation. With our process knowledge, products for in- or post-process measurements and quick-change technology, we occupy the key areas for successful automation.” At EMO 2025, Hainbuch will be demonstrating with live automation how production companies can make the step towards automated production even with the smallest batch sizes (see also Hainbuch info box).
The clamping and gripping device specialist Röhm from Sontheim an der Brenz offers a globally unique clamping solution: the measuring clamping jaw is equipped with sensors and wireless data transmission and can therefore measure the clamping force in real time during machining. “We are revolutionizing the manufacturing process in machining in the long term, because real-time measurement of the clamping force during the machining process offers the user a whole range of benefits,” CEO Gerhard Glanz is convinced. “This starts with higher machine availability, because set-up times can be shortened and machining processes accelerated. This reduces part costs on the one hand, while increasing part quality on the other. This is pure process optimization and a real milestone in the digitalization of production.”
And this is how it works: the forces applied to the jaw are recorded by an integrated sensor and the data is processed. The actual clamping forces applied are measured – this allows process or productivity analyses as well as the documentation of measurement data. With an app from the southern Germans, users can also access the data on the move and evaluate processing parameters. “This is of course a very interesting feature, especially for the production of components that require documentation, for example in the aerospace industry,” says Glanz. “Our product quasi archives the digital fingerprint of the machining as proof of the quality of the production process. This and much more can be seen at our stand at EMO 2025.” The clamping jaw is therefore particularly suitable for the metrological quantification of the clamping forces acting on a workpiece. The VDW Research Institute also came to this conclusion in a study (see Röhm info box).
How far along is AI?
No automation without data: how do research and development see the current status of the machine tool? “The CAD-CAM-NC chain in production technology is often still characterized by a diverse software landscape with an inconsistent data structure,” says Dr. Marcel Fey, senior engineer in the Department of Machine Data Analysis and NC Technology at the Laboratory for Machine Tools and Production Engineering (WZL) at RWTH Aachen University under the direction of Prof. Christian Brecher. The latter coordinated the nationwide, BMBF-funded ProKI project and has now made it a permanent feature in the WGP (Wissenschaftliche Gesellschaft für Produktionstechnik – German Academic Association for Production Technology). “While the CAM system still contains a lot of information about the tool, blank, material and process parameters, this context is largely lost on the machine tool when the NC code is created. However, this context is necessary in order to implement meaningful applications of artificial intelligence in production,” says Fey. “Even in digitally well-positioned companies, collecting the raw data with the necessary contextual information presents us with far greater challenges than the actual AI application. In addition, the mere availability of contextualized information from production already creates considerable customer benefits. Furthermore, in many cases, the evaluation of this data can already deliver excellent results if it is based on engineering expertise and not by an AI.” This is not to say that artificial intelligence does not have great potential in production. On the contrary, it offers enormous opportunities, especially for complex relationships that are not yet fully causally understood. “Nevertheless, the challenge in German mechanical engineering is first of all to create the necessary conditions in terms of a software infrastructure that provides the required data before AI applications can generate real benefits in production technology,” summarizes Fey.
The machine tool as a coordinate measuring machine
Smart automation is always about connecting processes in a targeted manner. “As machine tools are equipped with 3D touch probes as standard, the potential use as a coordinate measuring machine seems obvious. The software and hardware available on the market already support this,” reports Dr. Philipp Dahlem from the WZL at RWTH Aachen University, Chair of Information, Quality and Sensor Systems in Production, headed by Prof. Robert Schmitt. “Although machine tools are becoming increasingly precise thanks to technological progress, challenges remain; the golden rule of measurement technology states that the measurement uncertainty should be smaller than the tolerance by a factor of 10. In addition, compared to conventional coordinate measuring machines, machine tools are exposed to changing production conditions, which makes stable measurement results more difficult.” Can the measurement results be trusted at all? “The ISO TS 230-13 standardization project is working on this, among other things,” explains Dahlem (see RWTH Aachen info box). “It aims to define industrially applicable methods for determining measurement uncertainty in machine tools internationally. Possible application scenarios as well as the limits of this technology will be described – and EMO 2025 will certainly showcase important further developments here too.”
Nothing in modern manufacturing companies works without automation and digitalization. So those who rely on solutions that provide both direct support and long-term added value will increase their productivity and competitiveness enormously. At EMO 2025, decision-makers and users will find everything they need to position themselves in a way that is both smart and future-proof and thus stay ‘one step ahead’.
(Length: 9,952 characters, including spaces)
Author: Dag Heidecker, specialist journalist, Wermelskirchen
Quick-change system
The video from Hainbuch America illustrates how the quick-change technology from the international supplier (eleven subsidiaries worldwide), headquartered in Marbach am Neckar, can be used productively: https://www.youtube.com/watch?v=LRL8ZrcXqCM
Measuring clamping jaw: study and video
The smart clamping jaw from Röhm is ideal for the metrological quantification of the clamping forces acting on a workpiece. This was the conclusion reached by the VDW Research Institute as part of its ‘SensoSpann’ study. The developed measuring concept, which is based on the use of several of these clamping jaws, represents “a qualified basis for further experimental investigation of workpiece clamping at standstill and in process”, according to the study summary of the research institute, which now wants to use the clamping jaws for further investigations.
A YouTube video shows how the smart product from Röhm can be used as a retrofit solution on machine tools at https://youtu.be/dsoDQld_Ia4
Standardization project arouses international interest
The ISO TS 230-13 standardization project is an important step towards opening up ‘measuring with machine tools’ for industrial practice. By shifting component measurements to the machine tool, quality control loops can be shortened and resources saved in production. Together with the rapid development of artificial intelligence and the understanding of the stability behavior of machine tools, which is also being researched by the Chair of Information, Quality and Sensor Systems in Production at RWTH Aachen University, a machine tool that monitors its own production quality is becoming increasingly realistic. “As head of the project, I am also experiencing great international interest in the topic,” says Dr. Philipp Dahlem. “Initiated in Germany, the standardization project also represents an important aspect in relation to the strong machine tool industry in China, which is increasingly influencing standardization.”
www.iso.org/standard/87413.html
Contacts
Gerda Kneifel
VDW
Press and Public Relations
Lyoner Str. 18
60528 Frankfurt am Main
Germany
g.kneifel@vdw.de
Tel. +49 69 756081-32
www.vdw.de
Andreas Maier GmbH & Co. KG (AMF)
Marcel Häge
Head of Marketing
Waiblinger Str. 116
70734 Fellbach
Germany
haege@amf.de
Phone +49 711 5766-264
www.amf.de
Hainbuch GmbH
Clamping Technology
Lena Lohmaier
PR and Public Relations
Erdmannhäuser Str. 57
71672 Marbach
Germany
lena.lohmaier@hainbuch.de
Tel. +49 7144 907-219
www.hainbuch.com
Röhm GmbH
Thomas Roth
Director Business Development
Marketing
Heinrich-Röhm-Str. 50
89567 Sontheim a.d. Brenz
thomas.roth@roehm.biz
Phone +49 7325 16-380
Cell +49 152 22 88 70 93
www.roehm.biz
Laboratory for Machine Tools and Production Engineering (WZL) of RWTH Aachen University
Chair of Machine Tools – Department of Machine Data Analysis and NC Technology
Dr. Marcel Fey
Senior Engineer
Steinbachstr. 19
52074 Aachen
Germany
m.fey@wzl.rwth-aachen.de
+49 241 80-27409
www.wzl.rwth-aachen.de
Laboratory for Machine Tools and Production Engineering (WZL) of RWTH Aachen University
Chair of Information, Quality and Sensor Systems in Production
Dr. Philipp Dahlem
Head of the ISO project ISO TS 230-13 | Industrial Cooperation
Campus-Boulevard 30
52074 Aachen
Germany
philipp.dahlem@wzl-iqs.rwth-aachen.de
Tel +49 241 80 25861
Cell +49 171 9538786
www.wzl.rwth-aachen.de
daxTR – Technology + Editorial
Dag Heidecker
Specialist journalist
Auf dem Scheid 4
42929 Wermelskirchen
Germany
heidecker@daxTR.de
Phone +49 1577 902 1202
www.daxTR.de
Downloads
Pictures
Image 1 – 01 AMF Smart Automation.jpg
Image 2 – 02 AMF Wagen.jpg
Image 3 – 03 Hainbuch Schnellwechselsystem.jpg
Image 4 – 04 Hainbuch Dr Philipp Sommer.jpg
Image 5 – 05 Röhm Daten während der Zerspanung.jpg
Image 6 – 06 Röhm Messende Spannbacke.jpg
Image 7 – 07 RWTH Aachen KI generiert.jpg