Smart savings through efficient process control
Even before the start of the Russia-Ukraine war, rising energy costs were putting pressure on the manufacturing sector. Germany has long had the highest prices for industrial electricity in Europe. At the same time, all companies are being called upon to reduce their carbon emissions significantly and ensure that their production is resource-efficient. Grinding is no exception here. Industry experts are actively looking at how to reduce energy and resource consumption all along the process chain – including at the recent digital “Schleiftagung” grinding conference of the Laboratory for Machine Tools and Production Engineering (WZL) of RWTH Aachen University and at the GrindingHub trade show in Stuttgart in May.
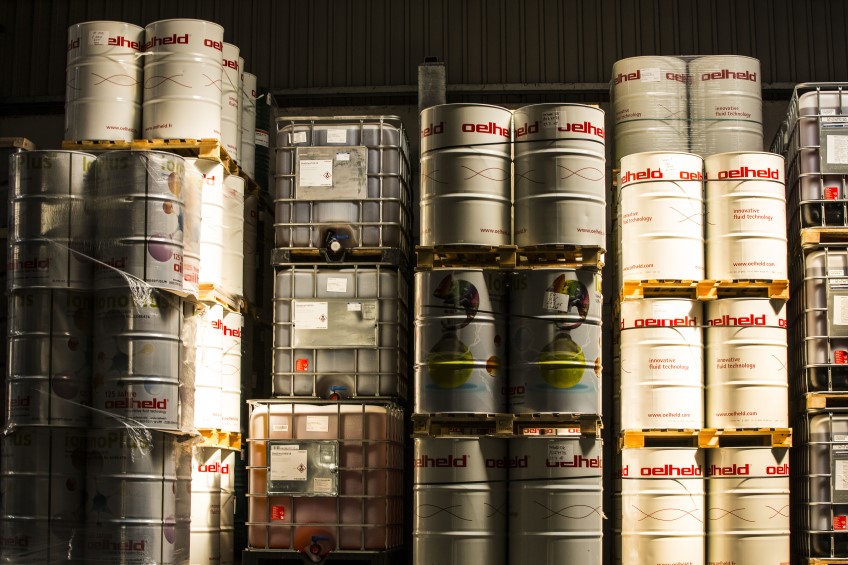
Spotlight on energy and resource consumption at GrindingHub
Rising energy and raw material costs, legal regulations and extended customer requirements are all significant factors which are increasing the importance of energy efficiency in grinding. Within the process chain, grinding is considered an energy-intensive manufacturing process, since comparatively small workpiece volumes are machined at relatively high cost. However, LCA improvements are anything but trivial, and can often only be achieved in small steps or on the periphery of the production operation itself.
Thinking beyond the grinding process
Prof. Thomas Bergs, Executive Director of the WZL and member of the WGP (German Academic Association for Production Technology) introduced a further aspect in his presentation at the grinding conference. He pointed out that grinding technology can make a significantly greater contribution to climate protection and resource conservation if companies are prepared to think beyond the actual grinding process. Optimizing the CO2-optimized design of the grinding process also includes considering the optimized function of the component in use. More efficient process control leads to reduced use of resources not only in the manufacturing, but also in the service phase of the workpiece by ensuring longer service lives and improved functional properties. This requires recording the use of energy and resources for each component in digitally networked production.
For Thomas Bader, Managing Director of Haas Schleifmaschinen GmbH in Trossingen, Baden-Württemberg, improving energy and resource efficiency therefore starts well before the actual grinding process: it begins in the selection of appropriate materials for the construction of the machines. In its Multigrind machines, for example, Haas has opted for a mineral cast machine bed which not only uses 30 percent less energy in production, but is also particularly durable and easily recyclable. In addition, mineral cast beds offer excellent vibration damping, which increases the service life of tools. If tools – in this case grinding wheels – have to be dressed less frequently, this has a positive effect on the energy footprint, says Bader.
Recyclability plays a major role in machine design, emphasizes the Haas manager, as do the requirements of the European RoHS Directive for electrical and electronic equipment. This stipulates that every component must be subjected to a risk assessment for environmentally hazardous substances. “Smart savings” is the watchword when it comes to measures that help reduce energy consumption in machines, says Thomas Bader.
Machines, grinding oils and grinding wheels
There are numerous examples of effective measures. Bader cites energy recovery modules which recuperate the energy of the NC axes and grinding spindles during braking, and the use of economical synchronous motors. Haas Schleifmaschinen also makes use of the intelligent Ecomodus standby concept. This is based on software that reduces power consumption in standby mode by a further 70 percent. The grinding machine manufacturer is also dedicated to minimizing the use of lubricants. For example, the company’s own linear axes rely on the use of economical grease lubrication instead of oil mist. The supply of energy-optimized cooling lubricant (coolant) is provided in a controlled pump operation using 3D coolant shaped nozzles specifically adapted to the workpiece.
The ways in which coolants and grinding oils can influence energy efficiency in the grinding process are explained by Ken Bausch, grinding oil expert at oelheld GmbH. The company is committed to sustainability in the development of its products, production processes and its use of resources – as expressed through its own Hutec (Human Technology) brand for humans, nature and machines. The Stuttgart-based company decided at an early stage to purchase its own machines, which would allow it to carry out test series itself. Analysis and testing equipment can now be used to determine the optimum type of oil based on a finely tuned ratio of viscosity and additives for every machine type and every grinding process, says Bausch. The results include not only long service lives and low refill quantities for the oils, but also quiet, smooth and easy running of the machines, which is indispensable for achieving fast machining, low tool wear, superior surface qualities and economical power consumption. “We are meeting very clearly expressed customer demands here,” says Bausch.
New materials posing new challenges
According to Bausch, these new and in some cases exotic materials that have to be processed will present major challenges in the future – and thus new tasks for the research and development department at oelheld. “We are gliding into new areas together with the machine manufacturers,” says the expert. He is also expecting to receive corresponding inquiries at GrindingHub. Furthermore, oelheld is cultivating partnerships with universities and research institutes in response to ever new technological requirements.
Similarly, the trend toward high-strength materials which are difficult to machine is likely to frustrate efforts to increase energy and resource efficiency, especially given the simultaneous calls for process-reliable manufacturing plants capable of 24/7 production. “The only way to improve energy efficiency in the grinding process is to find a perfect match between the machine, workpiece, grinding wheel, dressing tool, dressing spindle and cooling medium,” says Christoph Müller, Head of Application Technology at Dr. Kaiser Diamantwerkzeuge GmbH & Co. KG, system provider for grinding technology, based in Celle, Lower Saxony. As a rule, the customer’s primary focus is on the component being manufactured, he says. The process of dressing the grinding wheel responsible for carrying out the actual manufacturing process is regarded as non-productive time. Thus, the experts at Dr. Kaiser have the task of conditioning (profiling and sharpening) the grinding wheel in the shortest possible space of time.
Individual limits for process optimization
During process optimization, all parameters, especially cutting speed and feed rates, must be optimized before the dressing tool can be adjusted accordingly. However, it should be borne in mind, says Müller, that each production machine has its own physical limits within the process. Here, he says, it is often necessary to rely on empirical values. Nevertheless, about 80 percent of the optimization potential can be determined by making prior process calculations.
The grinding wheel itself offers optimization potential in terms of cycle time, as it can be trimmed not only for faster grinding but also for a longer tool life. After the unavoidable dressing process to condition the grinding wheel, it will be able to grind stably for longer and create more workpieces until it needs to be dressed again due to grinding wheel wear, abrasion, clogging or loss of shape. According to Müller, Dr. Kaiser is making a contribution to sustainability with its in-house ECO change system, which will also be on display at GrindingHub. Here, the carrier unit can be used several times; only the diamond coating (which wears out over time in the dressing process) is replaced. This saves more than 80 percent of material and energy compared to conventionally manufactured dressing tools.
Durability is key factor in resource conservation
For grinding oil manufacturer oelheld, improving energy efficiency involves creating durable products, ensuring superior quality levels and using high-grade raw materials, emphasizes Ken Bausch. Durability is also the key to resource-saving production for Thomas Bader, Managing Director of Haas Schleifmaschinen. For him it is vital to ensure that the manufacture and use of the company’s Multigrind machines are as environmentally friendly as possible. This includes advising customers on how to obtain the longest possible use of their machines. A lifetime of 30 years is not unrealistic, he says. “It often makes more ecological sense to give machines that are not in continuous use a general overhaul with new components and thus breathe a second life into them than to advise customers to buy new equipment,” Bader notes.
At GrindingHub, Haas Schleifmaschinen will present its first ever Multigrind system in which the machine and control are completely separate. The machine is controlled via a tablet which can be replaced if the operating system is no longer receiving updates or if a fault develops. In this way, machines can continue to offer a long service life even in these times of fast-moving digitalization and increased networking. It is important to think beyond the grinding process itself.
(Size: around 9,581 characters, including blanks)
Author: Cornelia Gewiehs, freelance journalist, Rotenburg (Wümme)
Downloads
Documents
Pictures