“Technologically up-to-date” High-tech manufacturing processes at EMO Hannover 2025
Standardized interfaces ensure efficient communication between the machines
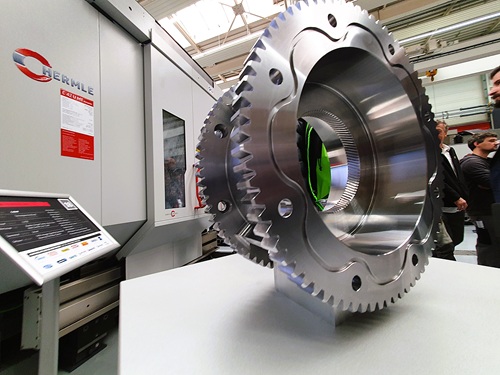
Frankfurt am Main, February 25, 2025 – How can European manufacturing companies succeed in global competition? One particularly effective method is the continuous development and application of innovative technologies. If these can then also be labeled “high-tech”, it becomes even more difficult for other manufacturers to copy the technologies. It is important to develop and maintain this head start – so that it can be turned into a competitive edge. Industrial suppliers and research institutes show how it’s done. These and many more innovation boosters can be found at EMO Hannover 2025.
From precision tools and high-tech machine tools to the integration of simulation analyses: The field is diverse when it comes to gaining a competitive edge, as the following practical examples show.
Four years of development time for high-tech cutting edge
Genuine technological progress is often demonstrated in the perfection of already proven products through further development. Here is an example: One of the biggest challenges in internal machining – depending on the material – is long chips. They wrap around the tool, clog bores or, in the worst case, lead to tool breakage. A chip breaking geometry can help here. This guides and shapes the chip and causes it to break. In the past, specially lasered or ground chip breaking geometries were used for this purpose, which entailed corresponding costs for the cutting insert. Paul Horn GmbH from Tübingen has now succeeded in developing a universal boring tool with sintered chip breaking geometry. It offers a high degree of process reliability thanks to excellent chip control during use. The geometry can be used universally for different material groups and is suitable for internal, face, copy and reverse turning. Managing Director Markus Horn knows the technical and economic challenges in the machining environment and is therefore enthusiastic: “We are pushing technological boundaries. This precision tool pushes the limits of today’s technology and can only be produced with the brain power of clever individuals. It took around four years of development time with numerous tasks relating to both the process and the materials. In the end, we managed to achieve a cost-effective solution to the problems caused by long chips in the internal machining of small bore diameters.”
In addition to the geometry, Horn has also optimized the blank of the cutting insert thanks to greater rigidity and an even more stable cutting edge area. The cooling supply has also been revised. The wide range of applications for the cutting inserts is also reflected in their cost-effectiveness: The costs of the new tool are similar to those of standard cutting inserts without geometry. “This development shows how technology can set you apart from the global competition in terms of technology, economy and price,” concludes Matthias Rommel, also a managing director at Horn. “EMO 2025 is the ideal platform for Horn to present its innovations to international manufacturing specialists in person.”
Powerful machine table – complete machining for particularly high demands
It is becoming increasingly important for machining companies to be able to manufacture components in a single clamping operation. Accordingly, there is demand for powerful 5-axis machines, which can perform a wide range of turning tasks just as efficiently as milling work. According to Dr. Manuel Gerst – Head of Development at Gebr. Heller Maschinenfabrik GmbH in Nürtingen – this is a trend that is gaining international significance: “The proportion of turning performed on our appropriately equipped machining centers is already around 30 percent and will increase to around 40 percent in the future.” Reason enough to raise the essential basis for such turning work to a whole new level. With Mill-Turn-Enforced technology, the engineers from Nürtingen have succeeded in developing a direct-drive rotary table that has exceptional performance data and is to be used in all of Süddeutsche’s 5-axis machines in the future. It has already been used successfully in a Heller machining center (BAZ) since autumn 2024. Another 5-axis machine, including the rotary table, will be available on the market in time for EMO 2025.
But what does ‘exceptional performance data’ mean? The biggest challenge is to achieve equally high torques and speeds. “That’s exactly what we’ve managed to do,” says Gerst, presenting the figures: “With the new table, we can achieve up to 1,250 Newton meters and up to 1,140 revolutions per minute. These values are around 20 percent higher than what is usual on the market. This enables manufacturing companies to achieve enormous chip removal rates.” The Nürtingen engineers have made many adjustments to achieve this. Particularly important: To keep the heat under control, a specially optimized torque motor is used, which generates only minimal heat. The same applies to the bearing. Overall, heat management in the table was the most important lever for success. For safety reasons, software also permanently calculates relevant operating states in order to warn of overloads in good time in extreme cases.
Even complex components can be machined in just one clamping operation
Maschinenfabrik Berthold Hermle AG from Gosheim decided early on to exhibit again at EMO 2025. It will present several 5-axis machining centers with automation solutions, as well as a 5-axis machining center as a mill-turn variant. On this mill-turn machine, components are milled, turned, drilled, ground, butted, deburred, smoothed, countersunk and measured – in other words, 13 highly productive processes for the complete machining of complex components are combined in a single clamping operation in just one component. Users can be shown the technologies relevant to them and integrate them into their processing strategies.
“It goes without saying that all the products on show will revolve around the two dominant themes of automation and digitalization,” says Marketing Director Udo Hipp, looking to the future. The automation of machining centers, in which Hermle has made a name for itself on the market with its own subsidiary for over 20 years, is a steadily growing market in view of the acute shortage of skilled workers. From pallet changers to handling systems or the “premier class” of adapted robot systems: The machine tool manufacturer Hermle is available to provide advice as well as process-related support. “We hope that EMO will live up to its reputation as the world’s leading trade fair,” says Udo Hipp, “and attract numerous international visitors to whom we can show technology ‘Made in Germany’. Hermle offers high-precision 3, 4 and 5-axis machining centers plus full automation and digitalization for ’round-the-clock’ use – and is therefore always ready for new machining technologies. At EMO 2025, we will be demonstrating our high level of expertise in milling, drilling and turning.”
Research spans the gap between high-tech and practical relevance
Prof. Dirk Biermann, institute director at the Technical University of Dortmund, confirms the enormous importance of always being technologically up to date: “The Institute of Machining Technology ISF has been conducting research into all relevant machining topics for over 50 years. In addition to basic research, it also carries out process technology and industry-related research projects.” The following three examples illustrate the range:
High tool temperatures during machining accelerate wear and shorten the service life of the tools. Knowledge of the temperatures can both increase process understanding and contribute to the validation of chip formation simulations. “A the ISF, we have therefore developed an innovative method that enables chip surface temperatures to be determined operando – i.e. under operating conditions,” reports the Institute Director (Photo 05 -A). “Another project deals with internal turning, which can only be carried out at a shallow machining depth due to the projection of the tools, especially for smaller bores. We have therefore developed a new type of tool system that enables internal contouring even in long, deep bores.” This system is integrated into the machine tool as an additional axis and has a strip-guided tool head that prevents oscillations (Photo 05 -B).
“Furthermore, the simulation-based prediction of process behavior can help with the set up of optimized process configurations at an early stage of the value chain,” concludes Biermann. “In the ‘ClusterSim’ research project – together with project partner AG Virtual Machining at TU Dortmund University – machine learning methods are being developed and applied in order to make data-based predictions for individual segments of complex machining processes (Photo 05 -C).” As a member of the Academic Association for Production Technology (WGP), the Dortmund-based institute will be exhibiting together with other WGP institutes at the joint “Sustainability” stand at EMO Hannover.
“EMO Hannover 2025 is a unique platform to discuss these and many other current developments at expert level,” stresses the WGP professor.
(Length: 9,603 characters, including spaces)
Author: Dag Heidecker, specialist journalist, Wermelskirchen
The direct link to the press release: https://vdw.de/presse-oeffentlichkeit/pressemitteilungen/
((INFOBOX Hermle))
Videos illustrate high-tech processes
Hermle is providing three videos to highlight in even greater detail what is currently technically feasible.
- Automatic pallet and vice handling: HERMLE HS flex hybrid C 250 / C 400 (DT)
- Benchmark in 5-axis technology, particularly suitable for large-volume components: Hermle C 42 – the 5-axis benchmark among machining centers with new 24″ comfort control panel
- Robot system – adapted to two 5-axis machining centers from Hermle: Hermle RS 1 robot system adapted to two C 22 U machining centers
((INFOBOX TU Dortmund – ISF))
Consolidate your knowledge in seminars
For a deeper understanding of the interrelationships described, ISF organizes annual seminars on “Process, tool and machine analysis” as part of the Production Academy of the German Academic Association for Production Technology (Wissenschaftliche Gesellschaft für Produktionstechnik [WGP]).
Contacts
Gerda Kneifel
VDW
Communication
Lyoner Str. 18
60528 Frankfurt am Main
Germany
g.kneifel@vdw.de
Phone +49 69 756081-32
www.vdw.de
Hartmetall-Werkzeugfabrik Paul Horn GmbH
Christian Thiele
Communication / Media
Horn-Str. 1
72072 Tübingen
Germany
christian.thiele@de.horn-group.com
Phone +49 7071 7004-1820
www.horn-group.com
Maschinenfabrik Berthold Hermle AG
Udo Hipp
Marketing
Industriestr. 8-12
78559 Gosheim
Germany
marketing@hermle.de
Phone +49 7426 95-0
www.hermle.de
Gebr. Heller Maschinenfabrik GmbH
Jacqueline Rost – Marcus Kurringer
Corporate Communications
Gebrüder-Heller-Str. 15
72622 Nürtingen
Germany
jacqueline.rost@heller.biz
marcus.kurringer@heller.biz
Phone +49 7022 77-5004 or -5683
www.heller.biz
Dortmund University of Technology
Institute for Machining Technology ISF
Prof. Dirk Biermann
Baroper Str. 303
44227 Dortmund
Germany
biermann@isf.de
Phone +49 231 755 2782
www.isf.de
daxTR – Technology + Editorial
Dag Heidecker
Specialist journalist
Auf dem Scheid 4
42929 Wermelskirchen
Germany
heidecker@daxTR.de