Holistic, bionic and disruptive – Additive Manufacturing Area at the METAV 2018 is ideally suited for networking
Components produced by additive manufacturing (AM) are ideally created using processes designed specifically for 3D printing throughout. Under these conditions, generative processes may usefully complement or supersede existing technologies. The current state of affairs is described as follows by one of the METAV’s regular participants Rainer Lotz, who as the Managing Director of Renishaw GmbH from Pliezhausen will be showcasing his firm’s capabilities at the Additive Manufacturing Area for what is already the second time.
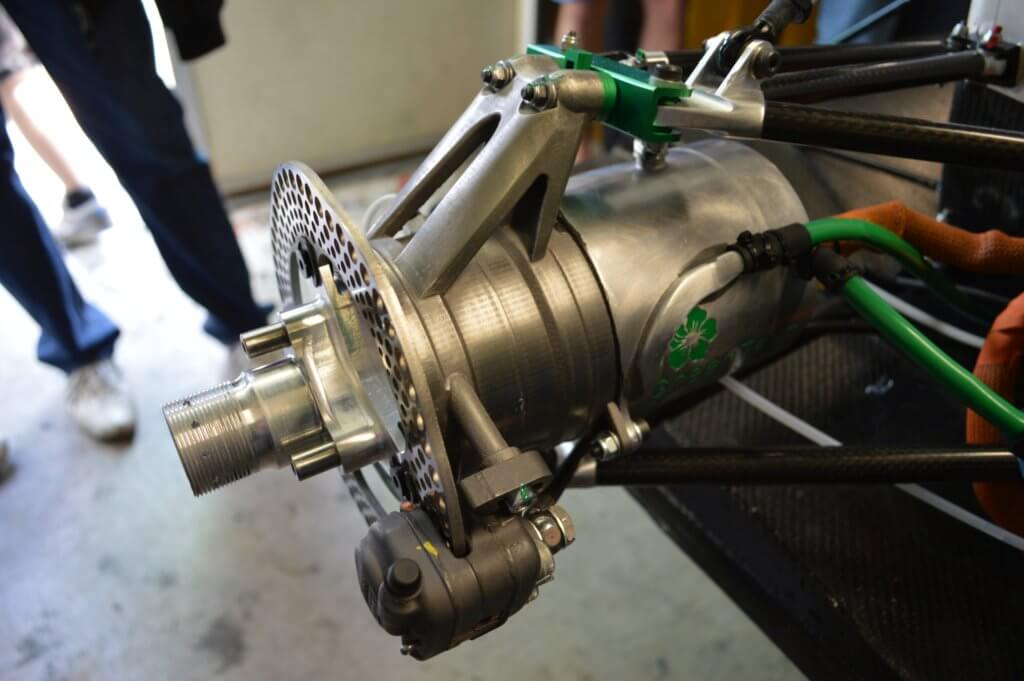
Renishaw has been actively involved in the field of additive manufacturing since 2006, and since 2011, thanks to the take-over of MTT Technologies Limited, it has been building 3D metal printers itself: what role is generative manufacturing currently playing for your company?
Rainer Lotz: We are continuing to use it ourselves, of course, in order to speed up our own development processes, and also as a new line of business for AM machines and all the relevant services involved.
Marc Saunders, Director Global Solutions Centres at Renishaw, says generative manufacturing may lead to disruptive changes on the market. Where are Renishaw’s processes already superseding older technologies?
Rainer Lotz: Together with medical experts, we have successfully developed a complete process for manufacturing customised facial prostheses, including the requisite surgical tools. The entire process chain can be seen at our Solution Centre in Wales, which focuses primarily on medical technology. For example, a motorcyclist once came to Renishaw to thank us for the reconstruction of his face following an accident. For a Formula Student racing car, we successfully produced a wheel mount that substantially downsized the total weight of the vehicle, so as then to set up a new world record for acceleration. In the industrial sector, too, we’ve already gained a foothold: one example here is tool inserts for plastics injection-moulding, which thanks to contour-hugging cooling significantly reduce tool wear and tear and the cycle times involved – while also substantially improving the quality of the parts concerned. Our staff at the Solution Centre in Pliezhausen can draw upon more than ten years of experience in this field, and make us one of the world’s market leaders.
What do you think of the view that industrial-scale 3D printing will not become widely adopted until the entire process chain has been holistically optimised?
Rainer Lotz: That will not suffice, because there’s a further step that has to be taken. Success will stand or fall with the creativity and process-engineering expertise of the designers involved. If I want to get maximum added value from additive processes, the rethink has to already begin at the product design and development stage. In parallel, we began at a very early stage to offer the concomitant services and software, intended to assist design engineers in their work. With a view to the holistic digital workflow, we’re also focusing on interfaces to the software of all front-ranking manufacturers, like Siemens, Dassault or Auto Desk.
Is bionic design the new order of the day?
Rainer Lotz: That is indubitably an interesting approach, but the development people will then also have to take due account of changing functionality in terms of the stresses acting on bionically designed workpieces. Other aspects are no less interesting. For example, an additive manufacturing process for pump housings rendered assembly steps formerly required downstream superfluous, because it enabled the nipples previously flanged on, for example, to be easily integrated into the design. Or with a metal-cutting tool, we were able to fit additional blades and design cooling channels that have thus substantially upgraded the performative capabilities concerned. So the added value created by additive manufacturing extends far beyond a bionic design.
What are your intentions with the new Solutions Centres and with what are called rental cells?
Rainer Lotz: The Solution Centres offer us an option of doing practical work with our customers, and developing processes and parameters that are suitable for them. Of course, there we offer capabilities like part optimisation, benchmarks, test series and contract manufacturing. The arrangement involved is this: the customer rents a cell with a complete line, which he either operates by himself, or in which as a beginner he methodically familiarises himself with the technology concerned, assisted by an experienced Renishaw operator. If necessary, the customer involved can adopt the process developed in the cell one-to-one in his company later on. The technical feasibility of their parts in an additive process is currently of major importance for many of our visitors.
What are your reasons for participating again as an exhibitor in the Additive Manufacturing Area, which was organised at the METAV for the first time in 2016?
Rainer Lotz: The entire industry is still at a very early stage in this regard, where the degree of maturity is as yet very low compared with ablative processes. So the METAV 2018, in conjunction with the specialised “Inside 3D Printing” conference, offers an ideal framework for networking with numerous users and firms in the sector. Only together can we increase still further the developmental speed of this technology. We believe it will invigorate the entire sector, and are looking forward to plenty of rewarding mutual feedback.
What will you be showcasing at the METAV 2018?
Rainer Lotz: Our exhibits there will include solutions for additively manufactured tools made of maximum-strength steel, which up to now had not been amenable to laser melting due to the risk of cracking involved. We have now succeeded in creating a dependable process using a line with a specially heated build chamber. This is of particular interest for the METAV community, and can be performed in this quality at present only on Renishaw’s lines.
Interviewer: Nikolaus Fecht, specialist journalist from Gelsenkirchen
Downloads
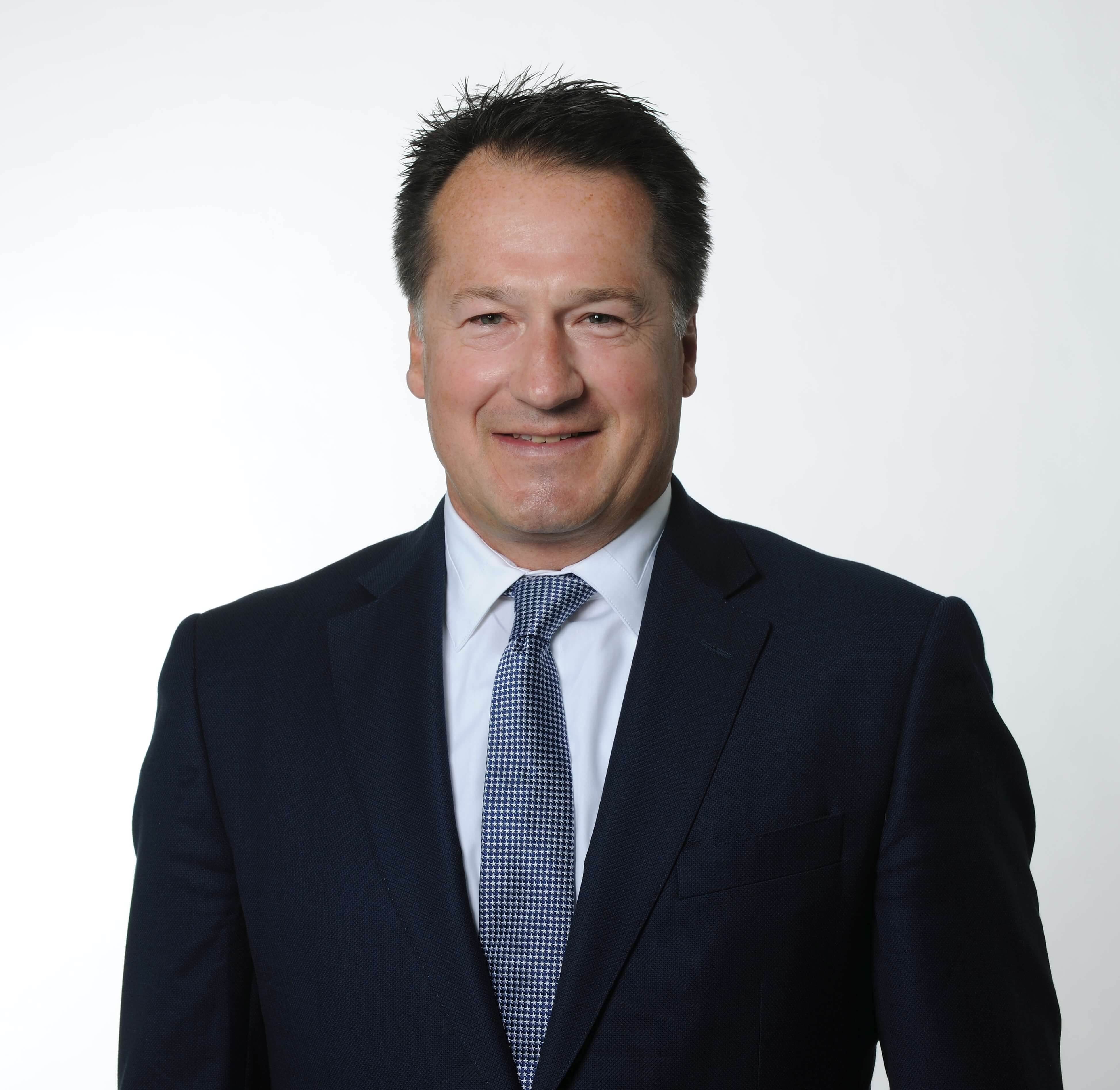