International METAV Press Forum hosted by Phoenix Contact- Communication is the key
From 20 to 24 February 2018, the METAV in Düsseldorf will be the venue for spotlighting modern technologies, services and trends in the world of metalworking. Besides exhibits and keynote topics themed around the value added chain, the “Areas” will spotlight solutions from fields such as tool and mould construction or up-to-the-future technologies like additive manufacturing and Industry 4.0. In order to illuminate the links between classical metalworking and innovative developments on show at the METAV, the fair’s organiser, the German Machine Tool Builders’ Association (VDW) arranged an international press forum in Blomberg, Westphalia (between Paderborn and Bielefeld). For the hosting company Phoenix Contact, besides topics of “Digital process chains in tool construction” and “Additive manufacturing”, discussions centred primarily on strategies for Industry 4.0.
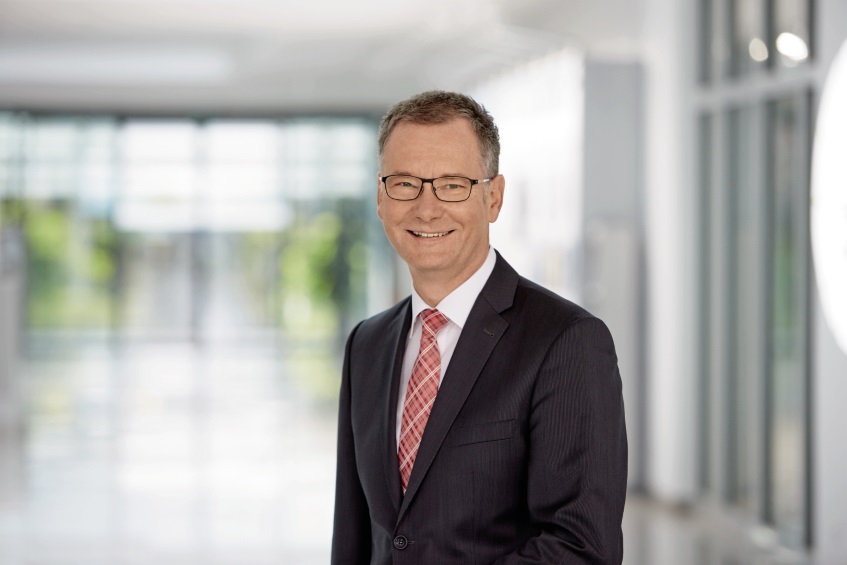
Phoenix Contacts’ product range covers components, systems and solutions in the fields of electrical engineering, electronics and automation. This tradition-steeped family firm, founded in 1923 as a one-man business trading in catenary wire terminals for electric trams, exemplifies the growing importance of connection and automation technologies. Today, the company employs around 15,000 people worldwide. The Phoenix Contact Group comprises 12 companies in Germany, and more than 50 sales firms of its own, plus 40 agencies in Europe and overseas. One man who has experienced and helped to shape around 30 years of this evolution is Roland Bent, Corporate Technology Officer at Phoenix Contact. “Automation has significantly accelerated developments in the industrial sector,” he says. “But this will in future be far exceeded by the speed at which the industrial world is now going to be transformed in the era of digitalisation.” Roland Bent sees the industrial sector as entering a phase, “in which we are learning with and from each other”. But each company is basically faced with the decision “either to simply wait passively for the digital transformation to happen or proactively join in shaping it”.
Digitalising the value added chain
Phoenix Contact is geared up for the future. The company attaches high priority to Industry 4.0 with two essential aspects: firstly, smart technologies for its own production operations, which with machinery designed and built in-house and high vertical integration offer excellent terrain for the consistent use of digital data. Secondly, the firm’s specialists are developing in “cooperative conceptions” innovative automation products for customers’ production lines. All this is being driven forward by a “digital agenda” that is based on digitalisation of the value added chain: “Only firms that provide a digital image of their production results will in future be able to deliver into this chain,” is Roland Bent’s firm conviction.
At the METAV Press Forum, Frank Knafla, Master Specialist Industry 4.0 at Phoenix Contact, explained the importance of the internet for this development: “Using the internet as a communication system in industrial applications opens up entirely new options for organising and controlling the entire value added chain along the life-cycles of products and production systems,” to quote Frank Knafla. The combination of industrial Ethernet communication and the internet, with the resultantly direct interlinkage of things, services, people and machines, he added, enables smart applications to take on a new dimension. But here, too, different worlds were colliding, which first had to learn to communicate with each other. “Communication is the key,” says Frank Knafla.
Profinet and the cloud
The ability to access external computer infrastructures in the cloud enables users to process the huge quantities of data that will in future be acquired along the value added chain. Proficloud is the magic word that at Phoenix Contact stands for professional, holistic cloud solutions for automation. As Frank Knafla explains, decentralised systems communicate here “directly and securely over the internet” on the basis of the familiar Profinet (Process Field Network) standard. For this purpose, cloud control systems are installed at any desired locations, which link up to the Proficloud over the internet. At the local facility concerned, the decentralised cloud control systems appear like local Profinet subscribers, i.e. completely transparent and without any further configuration or additional programming. With the Proficloud from Phoenix Contact, data security is assured thanks to TLS (Transport Layer Security) encryption. All information that the cloud supplies can be communicated directly into the field level. Thus, for example, ERP order data can be transferred directly from the Proficloud using the Profinet protocol into the production line at the user’s own plant. Besides the professional cloud solution, Phoenix Contact offers the associated communication technology for sturdy and secure networks, including WLAN, in mechanical engineering applications.
Starting off with practically relevant fields of action
Since the advantages of Industry 4.0 for the production operations of mid-tier companies, in particular, may sometimes appear somewhat abstract, Phoenix Contact has defined practically relevant fields of action. “We don’t implement everything that’s technically possible,” explains Frank Knafla, “but only what guarantees an advantage for the process involved”. Aspects like quality, flexibility, performative capabilities and cost-efficiency are the primary focus.
In order to utilise the advantages of digital data in applications like tool and mould construction, all process phases within the value added network must first be supported with a harmonised digital description. Each physical product is assigned digital data. Using the appropriate technology, which ranges from heavy plug connectors and power supplies with individualised parameterisation to marking systems and individualised design solutions for embedded systems, Phoenix Contact creates the associated infrastructure. This enables project-referenced information to be acquired on things like costs and material types in injection moulding, so as to make the right decisions for producing plastic components.
Electrical connections and permanent, unambiguous identification of all components are here indispensable in the complex networked industrial sector. Since fast, error-free wiring can gain valuable time in the installation process and minimise the make-ready work involved in modularised systems, Phoenix Contact has developed push-in connection technology. Decentralised subscribers and control cubicles can thus be wired swiftly without requiring any tools. Conductors are plugged in without any direct contact with energised parts. The push-in product range includes terminal blocks, circuit-breakers, plug connectors and distributor blocks.
Batch Size One for the same costs as mass production
With its product portfolio, its services and solutions, Phoenix Contact aims to create the preconditions for fully automated manufacturing of increasingly individualised end-products down to Batch Size One. The company demonstrates what this might look like as exemplified by its own manufacturing line for producing isolating amplifiers at its facility in Bad Pyrmont. Isolating amplifiers, explains the company, are needed in electrical systems whenever sensitive measured-value signals need to be transmitted free of interference from the sensor into the control level. Since this sometimes entails highly individualised requirements, the automation specialists produce the isolating amplifiers as configurable variants on flexible production lines. Communication between product, staff and machine leads to an improved process sequence, says the firm, in which even small batch sizes can be produced cost-efficiently. From order placement to the finished product, all systems involved utilise digital data.
As an illustration, the creation of an isolating amplifier can be described as follows: a PCB fitted with SMDs (surface-mounted devices), on which up to 154 components can be accommodated, runs on the production line through a punch and laser inscription to “marriage” with the housing. After the product has been programmed with the firmware, an electrical test is performed before it is dispatched. From the first step onwards, an RFID tag establishes a link to the information that the higher-order system supplies. This includes, for example, details of what tests have to be conducted on the device and what firmware has to be implemented. Thanks to the tag, the higher-order system knows the current machining status of the individual module. On the screen, the employee sees the information he needs for his remit. Thanks to communication between the product and the line, the employee is always able to master the complexity entailed by the diversity of variants involved.
In actual fact, however, the product’s genesis begins much earlier: with the aid of a web configurator, the user selects the device best suited for his purpose, and then specifies the individual configuration. The isolating amplifier now produced to his stipulations is supplied without any extra charge even in Batch Size One. But that’s not all: if the conditions in the factory subsequently change, e.g. because the line is expanded, the isolating amplifier can be adapted to suit the new requirements involved. The user defines the new parameters by means of an app or PC software, and transfers them to the device by NFC (Near Field Communication) or Bluetooth. Information on the devices is retained, so that each configuration can be re-ordered. Unambiguous identification of the module concerned, moreover, enables the associated calibration certificate to be retrieved.
Networking and cooperation for new business model
Irrespective of the technical preconditions for Industry 4.0, which were mapped out by Phoenix Contact at the METAV Press Forum, the challenges of the future lie in developing new business models from the technical options available. In this context, enormous importance is attached to mutual feedback with other players and shared research projects involving academic institutions as well. Phoenix Contact is at the same time researching the effects on the workplace entailed by digitalisation. In conjunction with the OWL University of Applied Sciences, the company has designed the “Combicon Workshop of the Future”, in which the changes in remits and qualifications are explored.
Industry 4.0 live at the METAV
With the industrial “internet of things”, meaning interlinkage of machinery and sensor data with the virtual world, classical factory and process automation can be expected to gather significant momentum, as was clearly evident at the METAV Press Forum. In Düsseldorf, the “Industry 4.0 Theme Park”, which at its premiere two years ago had already proved to be a crowd-puller at the METAV, will pick up on this topic and provide insights into digital manufacturing. Here, too, the question will be answered of how small and mid-tier companies can benefit from digital manufacturing. On the joint stand, the company and research institutions will be showcasing solutions already implemented. The associated experts’ forum is tasked with presenting examples of best practice and providing further topics for discussion. The exhibitors’ stands will offer sufficient opportunities for mutual feedback, fully in line with the motto: communication is the key – for both innovations and further digital development.