Medical Area at the METAV 2018: customised solutions for curative competence
According to experts, “only the best of the best” in terms of machine tools qualify for use in the medical technology sector. From the viewpoint of a long-standing exhibitor at the Medical Area, the Citizen company elucidates how this is achieved even for highly complex 3D parts by a vastly experienced pioneer.
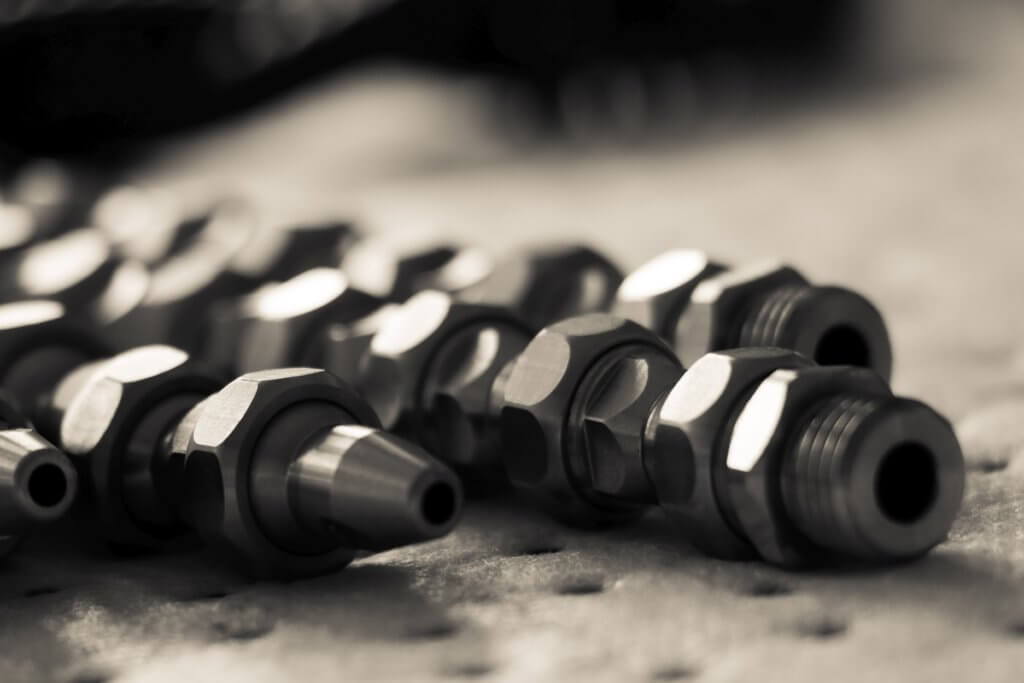
“Medical technology requires high-precision components in terms of quality and dimensional accuracy,” explains Nils Westphal, Branch Manager at the Neuss facility of Citizen Machinery Europe GmbH. “We went into this sector more than three decades ago in Germany and Europe.” Because Citizen was originally a watch producer, the company has always, from its everyday business, been familiar with the manufacture of systems fine-tuned to operate with maximised precision.
People want an “All-Round No-Worries Package”
The customers include globally operating companies that use Citizen’s automatic sliding-head lathes to manufacture bone nails, implants, cannulae, surgical tools and instruments, for example. To quote Nils Westphal: “All the firms involved insist on maximally stringent stipulations not only for their parts, but also for the capability and reliability of the process concerned.” This is why Nils Westphal speaks of what he calls an “All-Round No-Worries Package”, in which the actual machine accounts for around 50 per cent in terms of value. This is complemented by the complete peripherals, which combine to image the entire process. They include not only the loading magazine, the feed system, the high-pressure pump assembly, the discharge system, the palletising unit and the laser head, but also safety-relevant peripherals like fire extinguishing and extractor equipment.
The All-Round No-Worries Package even goes so far that Citizen at a customer’s request will check the process for at least one component earmarked for production on the automatic sliding-head lathe and develop it to optimum process-reliability. “Thanks to our meticulous process acceptance-testing procedures, users can begin production immediately,” says Nils Westphal. “Process-reliability has to be high in order to meet the stipulations applying for validation and to compensate for the shortage of skilled personnel by means of automated manufacturing.” Only with process-reliable operational procedures can the specialist personnel involved handle several machines in the process and maintain high levels of quality assurance.
Appropriate training courses from the basic level upwards also support the customers in skilling the requisite specialised personnel.
Cleanliness is the paramount priority
Cleanliness also plays a vital role in medical technology. Easily accessible machine interiors, automatic chip removal and high-pressure cooling lubrication systems, self-cleaning with a 20-µm filter, ensure that the automatic sliding-head lathes can operate dependably round the clock. “Meanwhile this form of complete machining has already been incorporated in many of the sector’s specifications,” reports Nils Westphal. No less important is burr-free external and internal machining, where the biggest challenge lies in internal boreholes in the ultra-small diameter range, i.e. 0.6 down to 0.25 mm and smaller.
For Nils Westphal, the METAV is an excellent opportunity to showcase the company’s specialised solutions. Back in 2014, under the aegis of the Metal meets Medical Special Show (today’s Medical Area), Citizen had found the fair to be highly beneficial. “We attend the METAV with a major stand of our own anyway,” says Nils Westphal. “With the Medical Area, the METAV offers us a welcome opportunity for separately presenting our corporate expertise in the field of medical technology. We are primarily targeting potential customers from the west and north of Germany, but we are, of course, also happy to welcome visitors from all the rest of Germany and from abroad.”
Machining 3D parts in a single setting
At the Medical Area, Citizen will be exhibiting its Cincom M16-4M8 sliding-head lathe, which is able to machine in 10 to 12 axes workpieces with a diameter of 1 to 16 mm and a maximum machining length of 200 mm. This high-end machine also enables special-shaped 3D parts (such as bevelled implants from dental technology) made of titanium or stainless steel to be manufactured in their entirety in a single setting. “This means that even parts for venous valves can be turned, which used to receive their final contours by milling,” explains Nils Westphal. “Nowadays, they’re produced in a single setting directly off the peg.” Among the special challenges involved in metal-cutting operations are angled abuments (dental support elements) featuring complicated oblique-hole drilling.