EMO Hannover 2023: Megatrends supporting manufacturing companies in international competition
European manufacturing companies are faced with multiple challenges when competing internationally. The hurdles that have to be overcome range from high energy and personnel costs to shortages of skilled workers and unstable supply chains for a wide variety of components. However, these very same difficulties are also giving rise to some remarkable innovations. The smart use of digitalization – including artificial intelligence – in combination with robotics and automation solutions can bring about major leaps in productivity and help raise competitiveness on a long-term basis. Cutting-edge solutions will be on show at the EMO Hannover 2023, the world’s leading trade fair for production technology. Practical examples from industry and research show the most effective ways of combining the different technologies.
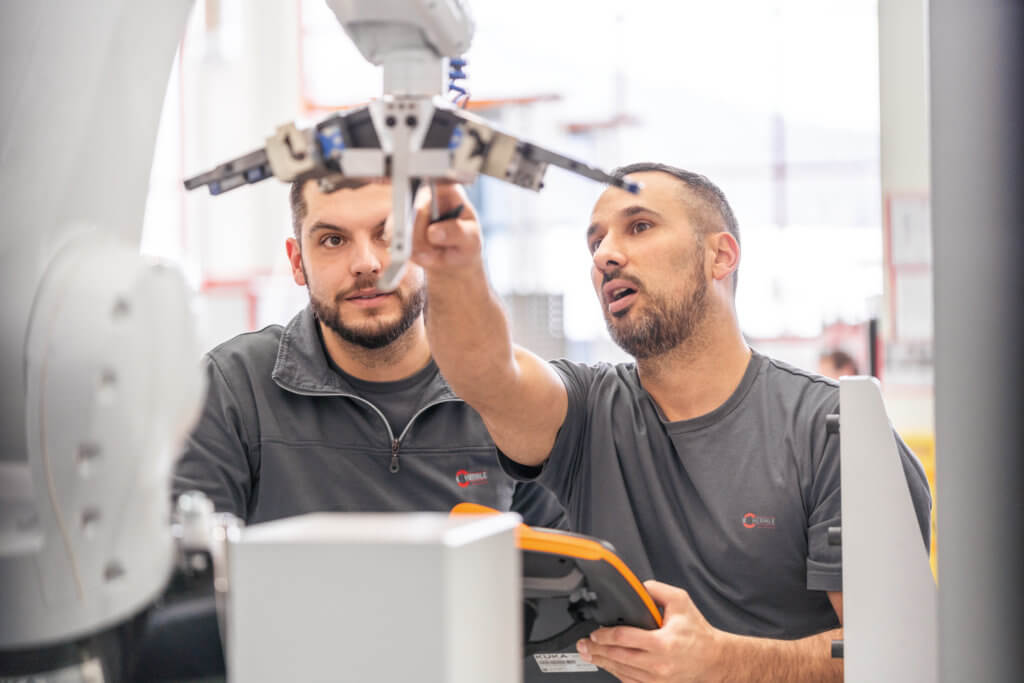
European manufacturing companies are faced with multiple challenges when competing internationally. The hurdles that have to be overcome range from high energy and personnel costs to shortages of skilled workers and unstable supply chains for a wide variety of components. However, these very same difficulties are also giving rise to some remarkable innovations. The smart use of digitalization – including artificial intelligence – in combination with robotics and automation solutions can bring about major leaps in productivity and help raise competitiveness on a long-term basis. Cutting-edge solutions will be on show at the EMO Hannover 2023, the world’s leading trade fair for production technology. Practical examples from industry and research show the most effective ways of combining the different technologies.
Highly attractive platform for information exchange
For Maschinenfabrik Berthold Hermle AG from Gosheim, EMO Hannover is the international trade fair for engineering in 2023. The main topics – especially for Hermle – are digitalization and automation. “Despite the continuous flow of new trends, we always put our customers – and their wide ranging requirements – first,” reports Udo Hipp, Head of Marketing. “Especially in our growth areas, which involve high levels of automation, we often have to consider the aspects of Industry 4.0 and the digitalization of our products. Here we offer solutions in the form of digital modules such as Digital Production, Digital Service and Digital Operation – with each module interlocking with the others. For example, the Digital Operation module provides machine tuning, permitting dynamic adaptation of the controller parameters and intelligent processing setups. The Digital Production module contains various tool and information management and automation control systems. The Digital Service module includes remote maintenance, diagnostic and monitoring systems.
“That’s a whole bunch of digitalization components we are able to offer our customers,” says Hipp. “At EMO Hannover 2023 we will be showcasing permanent digitalization and a number of automation solutions, including robotic and handling systems adapted to our machining centers. One of our priorities is ensuring that our automation solutions are easy to integrate into areas and industries that have not yet given much thought to these processes. It is this very shortage of skilled workers – a frequently heard topic of discussion at present – that is forcing us and our customers to invest in sophisticated automation solutions combined with highly efficient machining centers, ideally all from a single source. We are hoping to see large numbers of high-caliber visitors at EMO Hannover 2023, and we’re also hoping that the event will serve as a platform for an intensive exchange of information and for new projects.”
Flexible and automated loading
The manufacturing industry, especially the machining industry, is currently having to contend with decreasing batch sizes and increasing levels of variance in parts. The situation is further exacerbated by the shortage of skilled workers in all areas. This is forcing companies to keep their machines in operation for as long as possible. One solution offered by automation experts Schunk GmbH & Co. KG, based in Lauffen am Neckar, Germany, is automated pallet handling. This allows systems to be loaded around the clock, even in small-batch and single-part production and with minimum staffing levels.
The system consists of a palletizer module and robot coupling for automated loading. The workpieces and clamping devices are set up on clamping pallets, magazined and successively loaded onto the machining center from the pallet magazine. On the bottom of the pallets is a uniform interface to the zero point clamping system. Similar to an adapter, it connects the machine to a wide variety of workpieces. The pallet systems also have a side interface which allows the pallets to connect securely to a robot or gantry. The southern German company has developed a new generation of power clamping blocks for automated clamping of workpieces in the machine. “The robot and Schunk gripper can then directly load and unload the centric clamping vices and workpieces,” explains Markus Michelberger, Head of Sales Clamping Technology at the company’s site in Mengen. “At EMO Hannover, we will be showcasing further automation and digitalization options in machining, as well as new developments in the field of sustainable, resource-saving clamping equipment.”
AI meets Digital Twins
Although feed drives rarely fail, they can cause high costs in production when they do. In its Kidz project, iwb is conducting research into how predictive maintenance can be implemented by combining algorithms and traditional machine tool models, even in cases where only a few failures have been observed. The background is that feed drives have a considerable influence on the productivity of machine tools: On the one hand, such failures are time-consuming and costly to repair. On the other hand, they significantly influence the machine dynamics and thus the actual metal removal rate. Switching to a predictive maintenance strategy therefore offers great economic potential. However, there is currently no comprehensive system on the market that only uses existing sensors to monitor and predict the condition of feed drive components of producing machine tools.
The Kidz project is therefore carrying out research into a hybrid system for predictive maintenance. It combines a digital twin with modern AI methods. “In contrast to purely data-driven approaches, the hybrid system can work with much less training data in the form of failure observations – which are difficult to obtain in the case of machine tools,” says Michael Zäh, Professor of Machine Tools and Manufacturing Technology at the iwb within TU Munich, emphasizing a key aspect. “At the same time, this approach allows a certain degree of interpretability with regard to its predictions, since wear can not only be detected globally via the digital twin, but also assigned to specific feed drive components.” External additional sensors can then largely be dispensed with, and only internal signals used. Grenzebach Maschinenbau GmbH from Asbach-Bäumenheim is involved in the project, and its machine will eventually be used to demonstrate the functionality of the system. “EMO Hannover 2023 offers an excellent platform for the international exchange of views on the various technical aspects for optimal solutions,” concludes Professor Michael Zäh.
Innovations and international contacts
“EMO Hannover is the number one platform for innovations,” confirms Stefan Raff, Head of Sales Robomachines at Fanuc Europe – Fanuc Deutschland GmbH, based in Neuhausen auf den Fildern. “Which is why it’s only natural that Fanuc is featuring two European premieres involving robomachines in Hanover. I can’t reveal any more at this point.” Overall, Fanuc will be moving in a new direction at the next EMO. Instead of focusing only on its own CNC controls and machines, Fanuc will now also be presenting complete packages to visitors, such as a system for manufacturing automotive parts. The specific demands of electric vehicles have brought about a change in the design of manufacturing facilities. There is a greater need for flexible manufacturing equipment, for instance. Criteria such as TCO (Total Cost of Ownership) and ROI (Return on Investment) are playing a greater role than ever. “In addition, we are seeing further growth in demand for process solutions – a trend that has now well and truly taken hold,” Raff continues. “The European Development Center we have set up in Neuhausen will support the design of such solutions based on European standards.” This gives added weight to the company’s claim: “Fanuc puts customer requirements at the heart of its R&D”. One such example – and representative of many other solutions – is the development and testing of extreme applications such as power skiving on Fanuc machines.
“A crucial factor, we believe, is having up-to-date equipment for initial and further training,” emphasizes Stefan Raff. “Automation is certainly needed as a means of coping with labor shortages in general and the lack of skilled staff in particular – but so. too, is the early and comprehensive incubation of young talent. And so, for the first time, Fanuc will be exhibiting an ‘Education cell’ at EMO, consisting of a machine, a robot and a complete training package. There will certainly be plenty of innovations on show at EMO Hannover 2023. Personally, though, I’m looking forward to the direct contact, especially with international visitors, which we’ve all missed for so long.”
The effective linking of automation, robotics and digitalization represents an established solution when it comes to optimizing process flows in the production environment. And now this approach is increasingly being enriched by digital twins and artificial intelligence. All the big names will be at EMO Hannover 2023 to present their latest solutions and to gather ideas and forge partnerships for their own optimization efforts. Hanover thus offers companies a globally unique opportunity to put themselves far ahead of the competition.
Downloads
Pictures