Die Tage der klassischen Werkzeugmaschine sind nicht gezählt
Alle Welt redet von 3D-Druck, additiver Fertigung und generativen Schichtbautechnologien. Gleichwohl frisst die klassische Werkzeugmaschine noch lange nicht ihr Gnadenbrot. Die EMO Hannover 2017 präsentiert ein internationales Gala-Menü der Fertigungstechnik – mit alternativen Verfahren als vielversprechendem Sahnehäubchen.
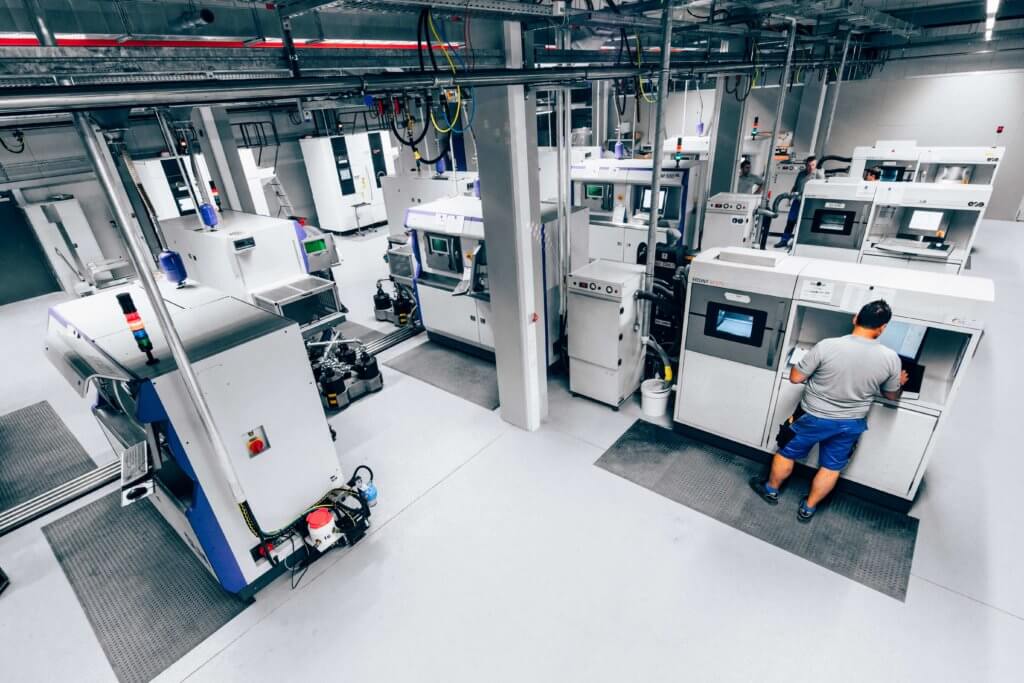
Sein Anliegen, „Kompetenzen im Bereich Schichttechnologien in die Produktfertigung zu übertragen“, hat Carl Fruth mittlerweile längst erreicht: Im Rahmen eines Technologietags mit Hausausstellung im April 2017 konnte die Fit AG (Fruth Innovative Technologien) im oberpfälzischen Lupburg neben der Einweihung eines neuen Bürogebäudes zudem die „erste additive Fabrik“ eröffnen. Die „Fit-Factory ist auch in einem internationalen Umfeld einzigartig in Bezug auf Fertigungskapazität und Automatisierungstechnik und soll als Vorlage für weitere Additive-Manufacturing-Fabriken der Fit-Gruppe dienen“, so der Firmengründer und Vorstandsvorsitzender Fruth. Er ist ein Pionier der additiven Fertigung – und ein Visionär, für den es schon vor zehn Jahren „keine Frage war, dass Schichtbautechnologien in Zukunft Normalität im Fertigungsalltag sein werden und der Absatz von Fräsmaschinen oder Spritzgussmaschinen immer weiter zurückgeht“.
Das heißt aber noch lange nicht, dass die Tage der „Mutter aller Maschinen“ – also der klassischen Werkzeugmaschine – gezählt sind. Das belegen eindrucksvoll die Innovationen, mit denen die Aussteller der EMO Hannover 2017 aufwarten. Als Hemmschuh für den Durchmarsch additiver Technologie in die individualisierte Massenfertigung bezeichnete Fruth selbst noch vor einigen Jahren die „fehlenden produktionstauglichen Fertigungsanlagen“. Das hat sich inzwischen verändert. Carl Fruth formuliert es so: „Es gibt eine große Anzahl zarter Pflänzchen. Eine Vielzahl unserer Kunden möchte gerne eine Substitution bestehender Komponenten mittels additiver Technologien herstellen. Das ist jedoch nur sehr selten möglich. Im Regelfall wird eine Neuentwicklung der Komponenten und sehr häufig auch der angrenzenden Komponenten des Systems notwendig. Zum einen scheuen viele Unternehmen vor diesem Aufwand zurück und zum anderen benötigt man natürlich auch spezielle Entwicklungskompetenz für diese neue Fertigungstechnologie.“
Neue Konstrukteure braucht das Land
Wenn traditionelle Gestaltungsrichtlinien außer Kraft gesetzt werden, bedarf es auch einer neuen Generation von Konstrukteuren, die funktionsorientiert denkt. Additives Herstellen bedeutet laut Fruth, „dass mit der Gestaltung nicht nur die Geometrie, sondern auch die Materialeigenschaften sowie die Bauteilkosten wesentlich festgelegt werden. Diese Komplexität erfordert spezielles Training und Erfahrung. Hinzu kommt, dass es bis heute kein Softwaretool gibt, in dem alle erforderlichen Funktionen vorhanden sind. Man muss also mit unterschiedlichen und komplexen Softwaretools arbeiten. Sehr häufig verliert man beim Übergang von einem Tool zum anderen Informationen. Wenn man bei der Bauteilentwicklung bis zu acht Iterationen benötigt, ist der erhebliche Aufwand hierbei offensichtlich.“
Die benötigten Kompetenzen habe zudem nicht ein einzelner Konstrukteur, sondern nur ein Team. In den klassischen Unternehmen sind die Kompetenzen noch dazu auf verschiedene Abteilungen aufgeteilt – hinzu kommen Kompetenzgerangel und Unsicherheit. Innovative Unternehmen sehen das aber auch als Chance: „Wir unterstützen unsere Kunden in diesem Prozess und trainieren sie Bauteil für Bauteil auf Höchstleistung in AM-Design. Deshalb nennen wir diese Produkte auch ADM – Additive Design and Manufacturing“.
Beim Thema „additive Fertigung in automatisierten Prozessketten“ – früher von ihm als „Achillesferse“ bezeichnet – blüht Fruth geradezu auf: „Sie treffen jetzt mein Steckenpferd. Wir haben keine digitale Spezifikation unserer Produkte. Deshalb fliegt Industrie 4.0 nicht, und deshalb klappt es auch mit der Automatisierung nicht richtig. Wenn alles per Hand automatisiert und optimiert werden muss, ist das ganz klassische Massenfertigung – ein alter Hut!“ Ob ein Roboter am Band steht oder ein Mitarbeiter das Produkt wendet, dabei gehe es nicht um fundamental neue Ansätze: „Solange eine Zeichnung und dicke Aktenordner mit Text notwendig sind, um ein Produkt zu spezifizieren, wird das nichts mit Industrie 4.0. Und dabei geht es nicht darum, ob es auch eine PDF-Datei der Spezifikation gibt – es geht um maschinenlesbare Spezifikationen und deren vollautomatische Umsetzung.“ Bisherige Schwachpunkte, wie die Reproduzierbarkeit der Prozesse, die Qualitätssicherung bei Massenfertigung oder verlässliche Simulationsmethoden, seien dagegen fast ausgeräumt: „Alle Beteiligten haben das Problem verstanden und arbeiten zielgerichtet an Lösungen.“
Mehr Technologien teilen sich den Markt
Die unvermeidliche Frage, ob denn die konventionelle Werkzeugmaschine arbeitslos wird, beantwortet der AM-Experte differenziert: „Die Fertigung von Bauteilen erfolgt in einer Prozesskette. Heute und auch morgen. Additiv gefertigte Bauteile benötigen ebenso wie andere Fertigungstechnologien eine Qualitätsprüfung: ob jedes Bauteil oder jedes 50. bei Gleichteilen, spielt dabei gar keine Rolle. Insofern denke ich nicht, dass es ein Ersetzen bestehender Technologien gibt.“ CNC-getriebene Verfahren seien alle sehr flexibel einzusetzen und würden alle ihren Markt haben. Die Frage sei vielmehr: „Welchen Anteil kann jede einzelne Technologie am Gesamtkuchen haben?“ Das Stück für die unterschiedlichen additiven Fertigungstechnologien ist derzeit winzig klein, es könne nur größer werden. Fruth glaubt jedoch auch, „dass der Kuchen insgesamt für CNC-Verfahren größer wird, auf Kosten werkzeuggebundener Fertigungstechnologien und anderer sehr personalintensiver Verfahren. Wir setzen auf die Kombination der unterschiedlichen CNC-Technologien.“
Auf der bevorstehenden EMO Hannover 2017 erwartet Fruth „die neuesten CNC-basierten Fertigungstechnologien, zu denen die additive Fertigung zählt, zu finden sowie neuartige potenzielle Produktlösungen in diesem Bereich. Eine Vielzahl von Anlagenherstellern additiver Verfahren und Materialhersteller stellen auf der EMO Hannover aus. Für uns als Betreiber der Anlagen ist die Messe daher interessant.“
Durchgängige Software-Lösungen für die additive Fertigung
Eine „neue Lösung für die additive Fertigung“ bietet seit kurzem Siemens PLM Software, die Business Unit für Product Lifecycle Management (PLM), Köln, an. Sie besteht aus integrierter Software für Konstruktion, Simulation, digitale Fertigung sowie Daten- und Prozessmanagement. Dadurch sei es möglich, ein „generatives Design automatisiert zu erstellen, und zwar auf Basis neuer Funktionen für optimierte Topologien“. So entstehen häufig organische Formen, auf die ein Konstrukteur von sich aus kaum käme und die mit herkömmlichen Fertigungsmethoden nur sehr kompliziert oder gar nicht zu fertigen wären. Mögliche Anwenderzielgruppen sind der Automobilbau, die Luftfahrtindustrie oder die Medizintechnik.
Die „revolutionäre Lösung“ und ihre Anwendungsmöglichkeiten erläutert Peter Scheller, Marketing Direktor bei Siemens PLM Software: „Das Besondere ist, dass es sich um eine durchgängige Plattform handelt. Basierend auf unserer Convergent-Modelling-Technologie beziehen wir innerhalb unserer NX-Software für integriertes CAD alle für das 3D-Drucken relevanten Produktentwicklungsschritte ein, vom Scannen bis zum Drucken. Beim 3D-Druck gibt es schon eine ganze Menge Einzellösungen in verschiedenen Nischen, sei es von Druckerherstellern oder anderen Anbietern. Der wichtige Schritt, den wir jetzt gehen, ist die Integration aller Prozessschritte in eine Plattform mit zentraler Bedienoberfläche, auf der sowohl die Geometrie als auch die Druckbahnenerzeugung in einem sicheren Datenformat abgelegt werden.“
Darüber hinaus hat Siemens PLM Software im Rahmen dieser Strategie Pläne für eine neue Online-Kollaborationsplattform vorgestellt, die eine weltweite Zusammenarbeit für die Fertigungsindustrie ermöglichen. Ziel sei es, einer globalen Fertigungsindustrie „on-demand-Produktkonstruktionen“ und 3D-Druck-Produktionen leichter zugänglich zu machen. In der Massenfertigung, so Scheller, „ist der 3D-Druck noch nicht vollständig angekommen. 3D-Druck kommt aus dem Prototyping und wird bislang überwiegend auch dafür eingesetzt. Wir stehen aber gerade an einer Schwelle: Das Verfahren tritt aus dieser Nische heraus; viele Unternehmen denken aktuell über einen Einsatz in der Massenfertigung nach oder verwenden das Verfahren schon dafür.“ Wenn man an additive Fertigungsverfahren in industriellem Maßstab denke, „ist aus unserer Sicht ein prozesssicheres Datenformat extrem wichtig, auf dessen Basis man Bauteile zuverlässig immer wieder in gleicher Qualität herstellen kann. Solch eine Plattform gab es bislang nicht, deshalb stellen wir unseren Kunden diese zur Verfügung.“ Gerade für die industrielle Produktion sei es sehr wichtig, Bauteile umfänglich beschrieben in digitaler Form vorliegen zu haben. Nur so könne man bei Rückfragen oder gar im Schadenfall auf diesen digitalen Zwilling zurückgreifen und Ursachenforschung betreiben.
Seine Erwartungen zur EMO Hannover 2017 bringt Peter Scheller so auf den Punkt: „Siemens wird auch weiterhin in Innovationen investieren und mit Technologiepartnern zusammenarbeiten, um neue Lösungen zu entwickeln, die für Fortschritte bei der additiven Fertigung sorgen und den 3D-Druck weiter vorantreiben. Deshalb freuen wir uns zur EMO Hannover 2017 auf gute Gespräche und den Austausch mit Kunden und Partnern. Die Messe ist eine hervorragende Plattform, mehr über aktuelle Herausforderungen und die Wünsche der Kunden zu erfahren.“