Latest trends in grinding and tool grinding technology
e-mobility, digitalization and automation: these are just some of the key trends in the grinding technology sector at present. Research experts and the companies exhibiting at the new GrindingHub trade show will be providing insights into the latest technologies and processes in this rapidly developing industry.
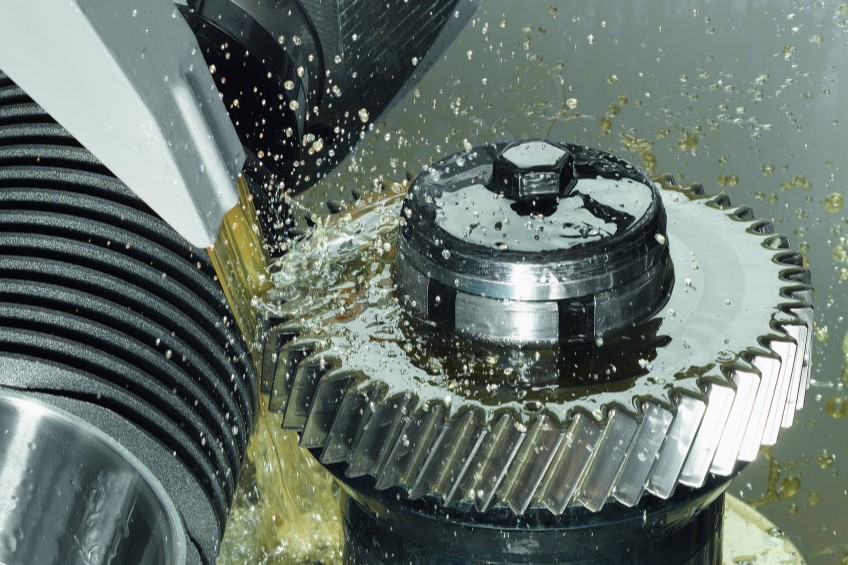
e-mobility, digitalization and automation: these are just some of the key trends in the grinding technology sector at present. Research experts and the companies exhibiting at the new GrindingHub trade show will be providing insights into the latest technologies and processes in this rapidly developing industry.
e-mobility is bringing about a change in the entire powertrain in cars. Gear parts must be ever lighter and increasingly precise and robust. Liebherr-Verzahntechnik GmbH has been taking a very close look at the requirements of e-mobility. Flank line modification methods are used to minimize noise and optimize load capacities. Here, generating grinding with dressing-free CBN grinding worms can represent an economical alternative to corundum worms. The process is reliable, ensures long tool life and significantly reduces the amount of time and effort required for measuring and testing.
The grinding process and clamping equipment for the production of finely worked e-bike transmission parts must be fast and precise. Using special clamping solutions, even small and collision-critical components can be machined without any problems. The exclusive Liebherr machine concept with single-table helps achieve optimum concentricity and high reproducibility in the production of parts with quality requirements in the micrometer range. The choice of process ultimately depends on the specific requirements. Liebherr can test all process parameters using its own machines. “Often there is no right or wrong,” explains Dr. Andreas Mehr, an expert in gear grinding. “As a partner and solution provider, we advise customers and show them alternatives – allowing them to make the best decision. That’s precisely what we’ll be doing at GrindingHub 2022.”
Process monitoring during generating grinding of e-gear tooth systems
Although the design of transmissions in electric cars is simpler than that of conventional internal combustion engines, it places far higher demands on the manufacturing accuracy of the gears. Electric motors must deliver constant torque over a wide speed range at rotation speeds of up to 16,000 rpm. There is also another condition, as Friedrich Wölfel, Head of Machine Sales at Kapp Niles points out: “Internal combustion engines mask transmission noise. Electric motors, on the other hand, are virtually silent. At speeds of 80 km/h and above, rolling and wind noise are the dominant factors, regardless of the powertrain. But in the range below that, transmission noise can become annoyingly noticeable in electric vehicles.” The fine machining of these components therefore requires the use of a generating grinding process that is both productive and, above all, optimized in terms of the noise behavior of the ground gear teeth. It is crucial to avoid so-called “ghost frequencies” which can be caused during component grinding as the result of an unfavorable machine and process design.
It takes much less time to grind gears than to take control measurements: this makes it impossible to inspect 100 percent of all components. The best approach, therefore, is to detect possible defects during the grinding process itself. Process monitoring is crucial here. “Numerous sensors and measuring systems that provide us with a wealth of signals and information are already built into the machines,” explains Achim Stegner, Head of Predevelopment. “We use these to assess the machining process and the expected quality level of each gear in real time in the gear grinding machines themselves. This allows order analysis to be conducted on noise-critical components in a similar way to the checks performed on an end-of-line test bench. In the future, gear grinding will provide significant added value by ensuring that the quality requirements for these components are met. As a GrindingHub exhibitor, we’re very excited by the innovative concept of the show.”
Developments in tool grinding technology
The tool grinding sector is having to meet ever greater challenges. On the one hand, more and more special tools are being produced in small batches, meaning that the process design up to the first in-spec part is gaining in importance from an economic point of view. On the other hand, the robustness and productivity of existing series processes must be continuously optimized so that they can hold their own against international competition even in high-wage countries. The Institute of Production Engineering and Machine Tools (IFW) in Hanover is pursuing several different avenues of research. The first step involves simulative mapping of the tool grinding process to support the process design. The simulation itself predicts the process force-related displacement of the ground blanks before the first cutting tool is produced, allowing this to be compensated for during grinding and thus avoiding any resulting geometric deviations. Furthermore, the load on the grinding tool is analyzed, permitting optimum adaptation of the process planning to the grinding tool used. This improves the machining result and minimizes the number of rejects. “Laser-based sensor technology has also been installed in the machine tool to measure the grinding wheel topography. This helps maintain the superior machining quality even at higher volumes,” explains managing director Prof. Berend Denkena, who is also a board member of the WGP (German Academic Association for Production Technology). “This allows continuous evaluation of the grinding tool status. It means it can be used to determine dressing intervals for specific processes. This helps avoid deviations in workpiece geometry due to wear – and associated rejects.”
Automation + Digitalization
“There has been a significant increase in the speed of grinding technology development in recent years. Advances in digitalization are the main reason for this,” said Dr. Stefan Brand, Managing Director of the Vollmer Group in Biberach, commenting on the latest trends in grinding technology. “We at Vollmer have been using digitalization in automation and data analysis for years now. We have developed our own IoT gateway that we are feeding more and more data into. The latest trend in grinding technology is the further integration of process data. The resulting knowledge gives users helpful insights into how the grinding process can be optimized. The journey into the digital future is constantly evolving. It is becoming clear how merging classic grinding technology with digital functions is not only influencing the grinding process itself, but also changing the market for grinding technology. Digital and automated processes are being used as optimization levers by sharpening services, tool manufacturers and globally operating manufacturing companies alike. This development is one reason why the new GrindingHub trade show is focusing not only on automation and digitalization in grinding technology but also on the areas of technology/processes and productivity. That’s why we welcome the opportunity to present our grinding technology to a broad and international audience at GrindingHub.”
(Size: around 7250 characters, incl. blanks)
Author: Dag Heidecker, daxTR – Technik+Redaktion, Wermelskirchen
Novel generating grinding process for cutting tools
The conventional tool grinding process is gradually reaching its technological and productivity limits in the mass production of cutting tools. This is why IFW is now researching into a new type of generating grinding process for the production of rotationally symmetrical cutting tools. This innovative process allows simultaneous creation of all peripheral cutting edges using a single grinding tool. This, in turn, eliminates many of the grinding tool changes and non-productive times which are normally required. The new generating grinding process promises not only major productivity benefits, but also improved machining quality and in-process wear compensation through shifting.
Contact persons:
VDW (German Machine Tool Builders’ Association)
Gerda Kneifel
Press and Public Relations
Lyoner Str. 18
60528 Frankfurt am Main
Germany
g.kneifel@vdw.de
+49 69 756081-32
www.vdw.de
IFW Institute of Production Engineering and Machine Tools, Leibniz Universität Hannover
PZH Hannover Centre for Production Technology
Prof. Dr.-Ing. Berend Denkena
Executive Director
An der Universität 2
30823 Garbsen
Germany
denkena@ifw.uni-hannover.de
+49 511 762-19333
www.ifw.uni-hannover.de
e-mobility, digitalization and automation: these are just some of the key trends in the grinding technology sector at present. Research experts and the companies exhibiting at the new GrindingHub trade show will be providing insights into the latest technologies and processes in this rapidly developing industry.
Kapp GmbH & Co. KG
Carola Rehder
Head of Communication/Marketing
Callenberger Str. 52
96450 Coburg
Germany
carola.rehder@kapp-niles.com
+49 9561 866-1250
www.kapp-niles.com
Liebherr-Verzahntechnik GmbH
Gear technology and automation systems
Thomas Weber
Marketing
Kaufbeurer Str. 141
87437 Kempten
Germany
thomas.weber@liebherr.com
+49 831 786-3285
www.liebherr.com
Vollmer Werke Maschinenfabrik GmbH
Dr. Stefan Brand
General Manager
Ehinger Str. 34
88400 Biberach an der Riß
Germany
s.brand@vollmer-group.com
+49 7351 571-0
www.vollmer-group.com
Texts and pictures to the GrindingHub can be found in the Press Section at:
www.grindinghub.de/journalisten/pressematerial/
You can also visit the GrindingHub on our social media channels: