Plug-and-Play für die Fabrik
Was wäre, wenn eine Maschine virtuell in Betrieb genommen werden könnte, bevor die tonnenschwere Anlage schließlich in der Fabrik steht? Mit dem Digitalen Zwilling und ausgefeilten Computersimulationen wird dies möglich.
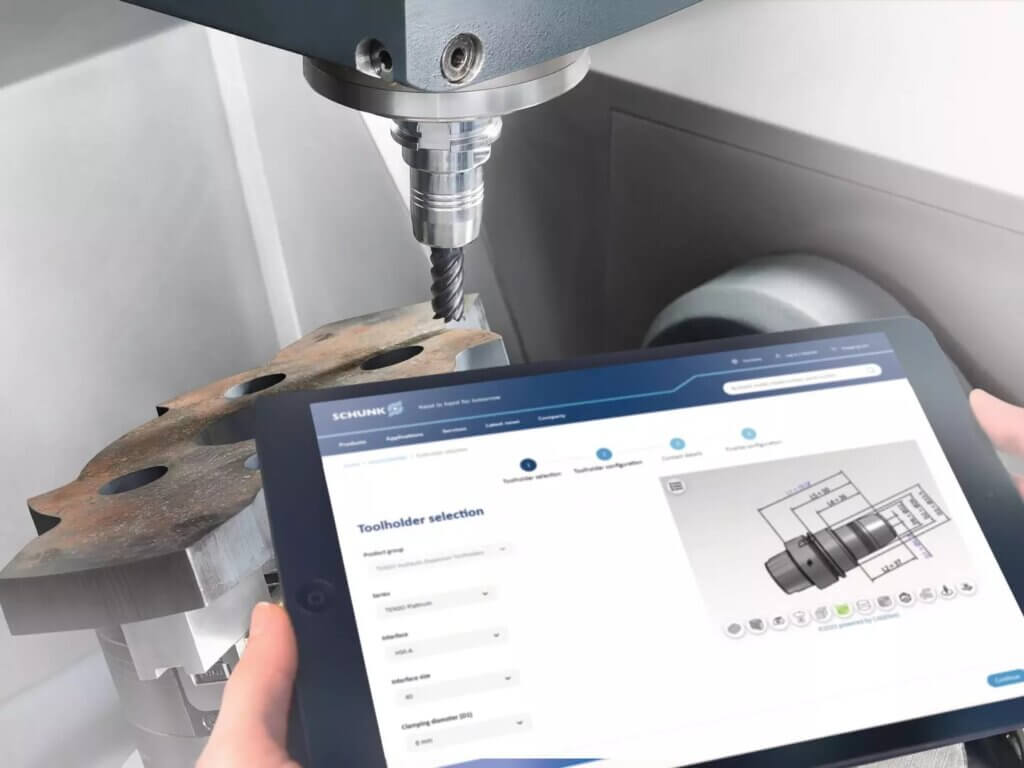
Digitaler Zwilling und Simulation heben Effizienz auf neues Niveau
Was wäre, wenn eine Maschine virtuell in Betrieb genommen werden könnte, bevor die tonnenschwere Anlage schließlich in der Fabrik steht? Mit dem Digitalen Zwilling und ausgefeilten Computersimulationen wird dies möglich. Ein 3D-Modell zeigt, ob sich die Anlage reibungslos in die bestehende Fertigungsumgebung einfügt: erst Plug-and-Play, dann Plug-and-Produce. Was der Stand der Technik ist und welche Effizienzgewinne möglich sind, wird auf der NORTEC, Fachmesse für Produktion, vom 23. bis 26. Januar 2024 in Hamburg zu erfahren sein.
Produktionsverantwortliche kennen die Herausforderung. Die Fertigung läuft seit Jahren rund. Nun soll eine neue Anlage dazukommen. Viele praktische Fragen stehen im Raum. Schafft die neue Maschine die nötige Leistung, um sich in die bestehende Fertigung einzufügen? Kann sie effizient mit anderen Maschinen kommunizieren? Antworten gibt der Digitale Zwilling. Er ist das Abbild des physischen Assets in der realen Fabrik und erlaubt deren Simulation, Steuerung und Verbesserung.
3D-Modell statt Stahl und Eisen
Computersimulationen spielen ihre Stärken aus, wenn komplexe Maschinen in eine bestehende Produktionslinie oder Fertigungshalle eingefügt werden sollen. Wie das geht, erklärt Olaf Sauer, der am Fraunhofer-Institut für Optronik, Systemtechnik und Bildauswertung (IOSB) als stellvertretender Institutsleiter, Geschäftsfeld Automatisierung und Digitalisierung, tätig ist. „Anstatt wie früher darauf zu warten, dass der Maschinenbauer die Anlage liefert und sie an der vorgesehenen Stelle in der Halle aufgebaut wird, kann der Hersteller mit Hilfe des Digitalen Zwillings mit der virtuellen Anlage folgende Tests durchführen: Passt die Anlage von ihren Abmessungen und gegebenenfalls dem Bewegungsraum in die Halle beziehungsweise in die Fertigungslinie? Kollidiert sie eventuell mit Rohrleitungen oder Stützen? Kann die Anlage schon virtuell in Betrieb genommen werden, zum Beispiel mit der realen Steuerung, aber nicht in Stahl und Eisen, sondern mit einem lauffähigen 3D-Modell?“ Außerdem kann mithilfe des Digitalen Zwillings geklärt werden, ob die Anlage die geforderte Taktzeit und Stückzahl einhält, so dass die Ausbringung der Gesamtlinie erhalten bleibt.
Künstliche Intelligenz schon vor der Installation
Auch komplexe Fragestellungen lassen sich laut Sauer bearbeiten. Etwa: Welche Signale liefert die neue Anlage? Können aus den Signalen vorab Modelle mit Hilfe von Künstlicher Intelligenz gebildet werden? Möglicherweise bringt die Maschine oder Anlage sogar eine maschinenlesbare Selbstbeschreibung mit, sodass sie eingesteckt und erkannt wird und so eine Art Autokonfiguration möglich ist. Dies wird durch Standardisierung ermöglicht. Die Hersteller von Werkzeugmaschinen etablieren für Industrie-4.0-Anwendungen eine Art USB-Standard namens umati. Das Akronym steht für universal machine tool interface, also universelle Schnittstelle für Werkzeugmaschinen. umati basiert auf dem plattformunabhängigen Standard OPC UA. Es soll Maschinen und Anlagen unter anderem dazu befähigen, standardisiert und sicher Daten mit der übergeordneten Datenverarbeitung auszutauschen.
Digitale Zwillinge müssen für jeden Fall maßgeschneidert werden. „Aus unserer Sicht ist zunächst der Anwendungsfall entscheidend“, sagt Sauer und wirft eine weitere Reihe von Fragen auf, die je nach Verwendungszweck zu beantworten sind: Wofür soll ein Digitaler Zwilling eingesetzt und was soll damit erreicht werden? Soll er nur unternehmensintern verwendet werden oder sollen die Teilmodelle des Digitalen Zwillings mit anderen Unternehmen ausgetauscht werden? „Dann kommt es auf deren Interoperabilität an, also ob die Teilmodelle von anderen Unternehmen ‚verstanden‘ werden“, sagt der promovierte Wirtschaftsingenieur.
Wichtig ist zu klären, welche Teilmodelle für den oder die Anwendungsfälle benötigt werden und ob es schon standardisierte Teilmodelle gibt, die übernommen werden können, etwa von der Industrial Digital Twin Association. Es muss auch Klarheit darüber bestehen, welche IT-Systeme oder Engineering-Werkzeuge welche Teilmodelle in welchem Format erzeugen, also etwa proprietär oder in offenen Standards.
Digitale Zwillinge kostenlos im Download
Industriestandards für den Digitalen Zwilling stehen besonders im Fokus. Der Technologiekonzern und NORTEC-Aussteller Schunk SE & Co. KG mit Sitz in Lauffen am Neckar, der Greifsysteme und Spanntechnik herstellt, setzt sich im Technologieverein Industrial Digital Twin Association gemeinsam mit anderen Unternehmen für eine Weiterentwicklung des Digitalen Zwillings zum industriellen Standard ein. „Schunk bietet für alle Standard-Katalogprodukte aus dem Greiftechnik- und Werkzeughalterportfolio Digitale Zwillinge kostenlos zum Download an“, erklärt Unternehmenssprecherin Kathrin Müller auf Anfrage. In die Simulationsumgebung integriert, könne der Produktionsprozess risikofrei durchgespielt und digital optimiert werden, noch bevor die Maschine aufgebaut und eingerichtet sei.
Seit Neuestem bietet Schunk auch Konfiguratoren für kundenindividuelle Greifer, Greiferfinger, Spannbacken und zuletzt auch Werkzeughalter an. „Damit können nun auch maßgeschneiderte Produkte vor der Bestellung in die Simulation integriert werden, um beispielsweise zu prüfen, ob sich das Werkstück mit dem Werkzeughalter im Hinblick auf die Zugänglichkeit optimal bearbeiten lässt“, sagt Müller. Das Besondere ist, dass die Digitalen Zwillinge auch für diese individuellen Produkte ad hoc in wenigen Minuten zur Verfügung stehen. Schunk präsentiert auf der NORTEC eine Auswahl an Innovationen aus dem Spanntechnikportfolio. Onlinetools wie den neuen Werkzeughalter-Konfigurator namens „easyToolholder“ können Besucherinnen und Besucher ebenfalls am Stand von Schunk vorgeführt bekommen.
Welche Effizienzgewinne bringt der Digitale Zwilling konkret in der eigenen Fertigung? „Der Digitale Zwilling bietet vielfältige Potenziale“, sagt Jakob Trauer, Senior IT-Berater bei der EM Engineering Methods AG aus Darmstadt, die als Systemintegrator im Produktentstehungsprozess tätig ist. „Beispielsweise können Fabriklayouts virtuell getestet und optimiert werden, Wartungen können vorhergesagt oder Qualitätskosten gesenkt werden, indem der Digitale Zwilling eine virtuelle Inspektion samt automatisierter Gegenmaßnahmen ermöglicht“, erklärt Trauer, der zuvor am Lehrstuhl für Produktentwicklung und Leichtbau der Technischen Universität München (TUM) tätig war.
Kosten senken, Umsatz steigern, Nachhaltigkeit verbessern
„Um diese Mehrwerte besser und umfassender beschreiben zu können, haben wir zusammen mit dem Lehrstuhl für Produktentwicklung und Leichtbau der Technischen Universität München ein Digital Twin Value Framework entwickelt“, so Trauer. Dieses Framework verknüpft Anwendungsfälle Digitaler Zwillinge mit deren konkreten Potenzialen. Es soll aufzeigen, mit welchen Metriken diese quantifiziert werden können und wie sie dazu beitragen können, Kosten zu senken, den Umsatz zu steigern und die Nachhaltigkeit zu verbessern.
Dabei sind Simulationen beziehungsweise Digitale Zwillinge nicht auf spezielle Industriezweige beschränkt. „Zurzeit sieht man die meisten Anwendungen im produzierenden Gewerbe, in Produktion und Produktentwicklung. Um das volle Potenzial ausschöpfen zu können ist es auch entscheidend, die Nutzungsphase zu berücksichtigen – hier liegt momentan der Fokus auf der Forschung.“
Standardisierung von Daten und Modellen im Fokus
Um Simulationen und Digitale Zwillinge von der Forschung in die industrielle Praxis zu übertragen, sind einige Hürden zu überwinden. Trauer verweist auf eine Industrieumfrage, die der Lehrstuhl für Produktentwicklung und Leichtbau hierzu durchgeführt hat. „Am kritischsten wurde die Standardisierung von Daten, Modellen und Austauschformaten gesehen“, sagt er mit Blick auf den Digital Twin, im Fachjargon kurz DT genannt. Trauer sagt, dass EM Engineering Methods exakt dort ansetze, „indem wir gemeinsam mit unseren Kunden eine geeignete ‚DT-ready‘-IT-Architektur konzeptionieren und auch die notwendigen Softwarelösungsbausteine für das Backend und für den Nutzer bereitstellen“.
Für Industrie 4.0 und die Digitalisierung der Fertigung sind Digitale Zwillinge essenziell. „Mit ihnen können viele Aspekte im Voraus überprüft werden, bevor ein Produkt oder eine Maschine gebaut werden. Das spart bei der Inbetriebnahme, Erprobung und im Betrieb Zeit und Geld, weil die Tests vorab in der virtuellen Welt durchgeführt werden können und mögliche Fehler digital ausgebügelt werden können“, fasst Fraunhofer-Wissenschaftler Sauer zusammen. Je später ein Fehler an einem Produkt oder einer Maschine entdeckt wird, umso teurer ist es, ihn wieder zu beseitigen, sagt Sauer, der in seiner Laufbahn beim Fraunhofer-Institut bereits Projekte zur schlanken Produktion, zu Kernkompetenzen und zur Fertigungssteuerung bei Kunden wie Daimler-Benz, Adtranz oder Volkswagen begleitet hat. „Außerdem können Digitale Zwillinge über den gesamten Lebenszyklus eines Produkts genutzt werden, so dass auch Daten aus dem Betrieb in die Planung der nächsten Produktgeneration einfließen.“
Fingerabdruck, EKG und Fuß-Scan
Oft wird der Begriff des Digitalen Zwillings mit Simulation gleichgesetzt. Das ist nicht ganz korrekt, wie Sauer klarstellt: „Simulationsmodelle können Teil des Digitalen Zwillings sein, genauso, wie ein 3D-Modell einer Maschine, ein Digitaler Produktpass, ein Digitales Betriebshandbuch oder ein maschinell gelerntes Modell des Normalverhaltens einer Anlage jeweils Teile des Digitalen Zwillings sein können.“ „Das alles sind Teile, die bestimmte Aspekte des Digitalen Zwillings repräsentieren“, veranschaulicht der Fraunhofer-Experte. Übertragen auf den Menschen sei auch der gesamte Lebenslauf nur ein Teil von ihm; genauso wie der Reisepass, der Fingerabdruck, das EKG, die Geburtsurkunde, die Gesichtserkennung oder der Scan des Fußes, damit der Skischuh angepasst werden könne.
Der Digitale Zwilling bietet viele Vorteile. In der smarten Fabrik hat er bereits einen festen Platz, insbesondere hierzulande. Auf die Frage, ob Deutschland bei Digitalisierungsthemen in der Industrie einen Entwicklungsvorsprung vor japanischen und US-amerikanischen Konzernen habe, antwortet Fraunhofer-Wissenschaftler Sauer mit einem klaren und uneingeschränkten „Ja“.
Deutschland habe mit seinen starken Teildisziplinen alles, was für Digitale Zwillinge erforderlich sei, sagt der Wissenschaftler und Praktiker, der in seiner Laufbahn auch schon Projekte für Firmen aus Asien und Nordamerika betreut hat, und zählt auf, was das Industrie-Ökosystem Deutschland alles bietet: Entwickler und Hersteller von eingebetteten Systemen, Komponentenanbieter und Maschinenbauer, Automatisierungsanbieter, Systemhäuser für Product-Lifecycle-Management (PLM), Manufacturing-Execution-Systems (MES) und Enterprise-Resource-Planning (ERP), Engineering- und Simulationsdienstleister sowie schließlich Fabrikbetreibende. „In Deutschland ist das komplette Ökosystem vorhanden, um Digitale Zwillinge erfolgreich umzusetzen.“, sagt Sauer, Die Fachmesse NORTEC wird ein Fenster zu modernen Produktionstechnologien öffnen und zeigen, welche Effizienzgewinne komplexe Computersimulationen in der industriellen Fertigung bieten können. Auf zwei Bühnen, dem so genannten Auditorium und der Speakers‘ Corner, werden täglich Vorträge, Workshops und Diskussionen rund um aktuelle Themen in der Produktionstechnik präsentiert, wie beispielsweise Künstliche Intelligenz, Digitalisierung und Automatisierung. Dort wird auch das Norddeutsche Simulationsforum und ein Workshop des VDMA Nord durchgeführt.
((Umfang: 11.628 Zeichen inkl. Leerzeichen))
Autor: Daniel Schauber, Fachjournalist, Mannheim
Kontakte
Fraunhofer-Institut für Optronik, Systemtechnik und Bildauswertung IOSB
Dr. Olaf Sauer
Stellvertretender Institutsleiter, Geschäftsfeld Automatisierung und Digitalisierung
Fraunhoferstr. 1
76131 Karlsruhe
Deutschland
Tel. +49 721 6091-477
https://www.iosb.fraunhofer.de/
Schunk SE & Co. KG
Kathrin Müller
Corporate Communications
Bahnhofstr. 106 – 134
74348 Lauffen/Neckar
Deutschland
Tel. +49 7133 103-2327
:em engineering methods AG
Jakob Trauer
Senior IT-Berater
Rheinstr. 97
64295 Darmstadt
Deutschland
Tel. +49 6151 7376-100
Daniel Schauber
Fachjournalist
Meerfeldstr. 14
68163 Mannheim
Deutschland
Tel. +49 170 2031976