„Auch der Ingenieur hat einen Platz in der Big-Data-Welt“
Mit gemischten Gefühlen blicken manche Produktionsexperten auf die EMO Hannover und die dortige „industrie 4.0 area“: Sie befürchten, dass Industrie 4.0 zu Algorithmen und Lösungen rund um Big Data führt, die auf lange Sicht das Wissen der Experten überflüssig machen. Entwarnung geben dagegen Oberingenieur Alexander Epple sowie Michael Königs vom Werkzeugmaschinenlabor WZL der RWTH Aachen, die auf das Zusammenwirken von Big Data und fachspezifischem Know-how setzen
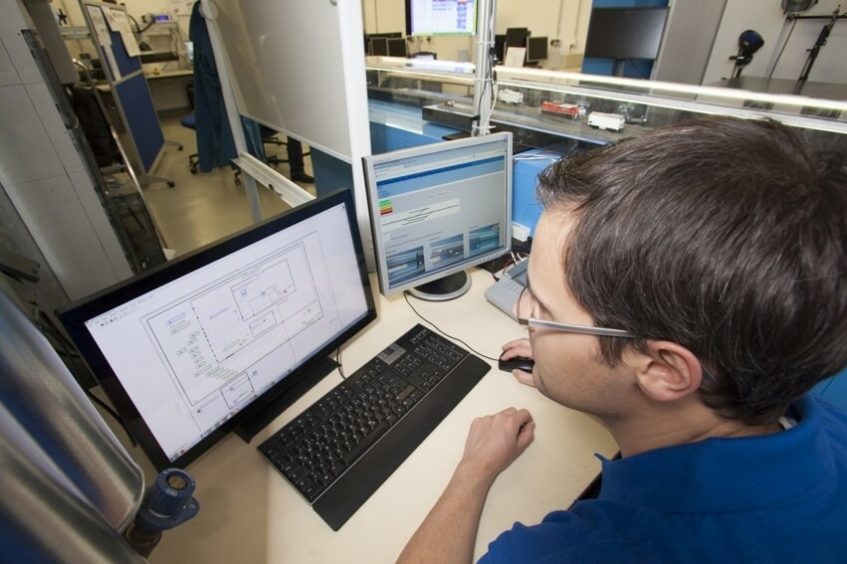
Herr Epple, Sie leiten als Oberingenieur am Werkzeugmaschinenlabor WZL der RWTH Aachen die Abteilung Maschinendatenanalyse und NC-Technik: Wie kamen Sie dazu? Wäre das nicht eher etwas für Mathematiker gewesen?
Alexander Epple: Ich bewundere Mathematiker für ihre mächtigen Algorithmen und ihre Eigenschaft, Probleme mit einem sehr hohen Abstraktionsgrad zu betrachten. Diese Fähigkeiten helfen auch bei der Big-Data-Analyse. In der Produktionswelt gibt es – bedingt durch die Vielzahl an Maschinen und Verfahren – sehr unterschiedliche Arten von Daten. Miteinander vergleichbare Maschinen mit gleichen Prozessen sind daher selten. Rein statistische Ansätze führen unter diesen Voraussetzungen kaum weiter, und abstrakte Big-Data-Ansätze stoßen im Produktionsumfeld schnell an ihre Grenzen. Mehr bringt es, produktionstechnisches Wissen, beispielsweise in Form von Modellen, mit den Daten zu verknüpfen. Daher hat auch der Ingenieur seinen Platz in der Big-Data-Welt.
Spiegelt Ihr Team den interdisziplinären Ansatz?
Alexander Epple: In meinem Team arbeiten sechs Wissenschaftler, die von qualifizierten Programmierern und Maschinentechnikern unterstützt werden. Das Team ist tatsächlich sehr interdisziplinär: Wir verfügen neben Maschinenbauern auch über Informatiker und Elektrotechniker. Außerdem arbeiten Dr. Marcel Fey mit seiner Maschinentechnikabteilung und ich sehr eng zusammen, da seine Abteilung über umfangreiches Modellwissen verfügt. Zusammen sind wir fast 30 Wissenschaftler. Damit kann man Ideen schon vorantreiben. Momentan sind wir dennoch auf der Suche, um unser Team zu verstärken.
Wie weit verbreitet ist dieser fachübergreifende Ansatz in der Praxis?
Michael Königs: Insbesondere im Bereich Simulation bestehen am WZL schon lange interdisziplinäre Teams. Auch an anderen Universitäten oder Forschungseinrichtungen hat sich dieses Vorgehen bewährt. Wir stellen aber auch fest, dass interdisziplinäre Teams im Kontext der modellbasierten echtzeitnahen Datenverarbeitung nicht länger nur optional sind. Vielmehr führt zukünftig kein Weg an dieser Zusammenarbeit vorbei. Erst durch die Verknüpfung und das Zusammenbringen von Methoden und Modellen aus unterschiedlichen Fachbereichen kann das erhebliche Potenzial, das mit der Datenauswertung verbunden ist, erschlossen werden. Zusammenfassend lässt sich somit sagen: Es gab schon immer interdisziplinäre Ansätze, diese werden jedoch zukünftig noch stärker an Bedeutung gewinnen.
Herr Königs, Sie sind einer der Informatiker: Wie gehen Sie in der Welt des Maschinenbaus vor?
Michael Königs: Man lernt in der praktischen Anwendung sehr schnell, dass die Datenqualität aufgezeichneter Signale ausschlaggebend für den Erfolg einer Analyse ist. Es steckt nämlich entgegen der Meinung vieler nicht immer alles in den Daten. So liefern Messsysteme einer Werkzeugmaschine zwar Positionsdaten, allerdings geben diese den realen Werkzeugpfad während einer Fräsbearbeitung nur näherungsweise wieder. Auf Abdrängungseffekte in Folge von Prozesskräften oder geometrisch-kinematische Ungenauigkeiten der eingesetzten Werkzeugmaschine etwa kann in der Regel nicht zurückgeschlossen werden. Durch das Modellwissen können die reinen Signaldaten mit diesen fehlenden Informationen angereichert werden. Erst dieser veredelte Datensatz eignet sich zum Beispiel zur Prognose von erzielten Werkstückqualitäten noch während der Bearbeitung.
Wie umgehen mit den riesigen Datenmengen?
Industrie 4.0 führt zu gläsernen Produktionsstätten, die dank der Zunahme an Sensorik und leistungsfähiger Auswerteelektronik Big Data erzeugen. Doch wie lassen sich die wertvollen Rohdaten etwa einer Werkzeugmaschine erfassen – lässt sich eine ältere Maschine ohne Sensorik nachrüsten?
Alexander Epple: Es gibt Forschungsprojekte, die sich damit beschäftigen, wie ältere Maschinen nachgerüstet werden können. Wir verfolgen darüber hinaus derzeit auch Ansätze, welche zunächst die in der Maschine verbaute Sensorik nutzen. Neben dem Motorstrom erfasst jede Maschine auch aktuelle Achspositionen. In der Regel sind direkte und indirekte Wegmesssysteme verbaut. Mit diesen Signalen können wir beispielsweise die Ratterneigung prozessparallel ermitteln. Auch die Prozesskräfte und Komponentenlasten für Ansätze im Predictive Maintenance lassen sich bestimmen. Dies gilt für ältere und für neue Maschinensysteme.
Big ist aber nicht immer „beautiful“: So ergibt die 100prozentige Datenerfassung der Arbeit eines Bearbeitungszentrums in Echtzeit (35 Kennwerte pro Millisekunde) pro Jahr bereits ein Datenvolumen von 5,8 Terabytes. Wie fischen sie hier die interessanten Fakten heraus?
Michael Königs: Für die Extraktion von interessanten Informationen und Kennwerten nutzen wir sowohl statistische Methoden (Machine Learning) als auch eigens entwickelte Algorithmen, die die Integration von Experten- bzw. Domänenwissen ermöglichen. Generell ist es aber richtig, dass bei kontinuierlicher Datenerfassung eine große Datenmenge anfällt. Nun gibt es Ansätze, nicht permanent mit maximaler Abtastrate alle Daten zu erfassen, sondern nur zu bestimmten Zeiten, nach bestimmten Events – z.B. Übertreten eines Schwellenwerts – oder für bestimmte Prozesse. Andere Ansätze komprimieren die Datenmenge durch Kennwertbildung. Wieder andere Ansätze nutzen bewusst die hohe Datenmenge, um mit entsprechenden mathematischen Algorithmen Muster zu erkennen. Es ist stark anwendungsabhängig, welcher Ansatz der erfolgversprechendste ist.
Lässt sich diese Datenmenge noch mit üblicher Hardware bewältigen oder ist ein Supercomputer – Stichwort Quantenrechner – gefragt?
Michael Königs: Die aktuelle Technik reicht – richtig eingesetzt – in unseren Disziplinen meist aus, wenn Einzel- oder Teil-Modelle von Experten entwickelt werden. Die breite, disziplinübergreifende Verschaltung und Anwendung dieser Modelle bringt die aktuell verfügbare Hardware jedoch schnell an ihre Grenzen. Eine auf diese Bedürfnisse ausgerichtete Cloud-Umgebung, in der sowohl statistisch als auch physikalisch motivierte Einzelmodelle gekoppelt und mit bedarfsgerecht bereitgestellten Rechenressourcen ausgeführt werden können, kann hier die benötigte Konnektivität und Rechenleistung bereithalten. Ich glaube aber nicht, dass sich eine solche Umgebung nur mit Quantenrechnern umsetzen lässt.
Wissenschaftler vom Fraunhofer IPK meinten, es sei sinnvoller, vor dem Speichern in der Nähe der Maschine eine intelligente Vorauswahl zu treffen, bevor dann ein reduzierter Datensatz – Stichwort Smart Data – in die Cloud wandert. Was halten Sie von diesem Ansatz?
Alexander Epple: Der Idee kann ich grundsätzlich folgen. Auch am WZL beschäftigen wir uns mit der lokalen Datenvorverarbeitung und -interpretation und somit der Veredlung der Daten zu smarten Daten in unmittelbarer Nähe des Maschinensystems. Die Vorteile dieser lokalen Datenvorverarbeitung liegen auf der Hand. Allerdings gibt es auch Firmen, die alle Rohdaten ungefiltert in einem zentralen System – etwa einer Cloud – speichern und verarbeiten.
Was ist für Sie eine Cloud und wie lassen sie sich nutzen?
Alexander Epple: Unter Cloud verstehen wir ein Modell für den ortsunabhängigen, On-Demand-Netzzugang zu einem gemeinsamen Pool konfigurierbarer IT-Ressourcen, die bedarfsgerecht eingesetzt und wieder freigegeben werden können. Diese umfassen neben Netzwerkbandbreiten und Rechenhardware auch Services und Applikationen. Im Kontext von Big Data bieten Cloud-Plattformen aufgrund eben dieser Skalierbarkeit und der breiten Verfügbarkeit von Analysealgorithmen gute Voraussetzungen für die nachgelagerte Auswertung von Datenmengen, die zu groß, zu komplex, zu schwach strukturiert oder heterogen sind, um diese manuell oder mit klassischen Methoden der Datenverarbeitung auszuwerten. Technisch herausfordernd ist jedoch unter Umständen die vorgelagerte Datenübertragung. Ein lokales Datenerfassungssystem an der Maschine kann vergleichsweise einfach gestaltet werden, wenn die Daten nur weitergesendet werden müssen. Dies hat natürlich erhebliche Vorteile in der Wartung und im Roll-Out, stellt aber im Gegenzug hohe Herausforderungen an die notwendige Bandbreite zur Datenübertragung. Eine lokale Datenvorverarbeitung und -verdichtung kann sie deutlich reduzieren. Allerdings gehen mit jeder Datenverdichtung auch Informationen verloren, die für die aktuellen Betrachtungen vielleicht irrelevant, für zukünftige Szenarien jedoch ganz entscheidend sein könnten. Manchmal wird einem erst nachträglich bewusst, dass die nicht mehr verfügbaren Informationen doch hilfreich gewesen wären, um ein Phänomen zu interpretieren.
Beide Ansätze haben ihre Vorteile und es hängt von der Strategie des jeweiligen Anwendungspartners ab, welchen Ansatz er verfolgen möchte. Generell bemerken wir eine gewisse Skepsis, Daten zentral in einem Cloudsystem zu speichern. Es gibt aber auch Möglichkeiten einer lokalen „Firmencloud“. Selbst die Datenauswertung direkt an nur einem lokalen Maschinensystem kann schon große Potenziale der Produktivitätssteigerung bieten.
Big Data steigert Produktivität um 30 bis 150 Prozent
Wie kam es zur Zusammenarbeit mit den Experten von SAP, die zusammen mit Cisco und Huawei einen Big-Data-Client entwickelt haben, der im Takt der CNC alle Daten erfasst und speichert?
Alexander Epple: Die enge Zusammenarbeit wurde durch SAP initiiert, da ein Forschungspartner aus der Produktionstechnik gesucht wurde, der neben einer exzellenten Grundlagenforschung auch seit Jahren eine anwendungsorientierte Zusammenarbeit mit Industrieunternehmen vorweisen kann. Wir haben SAP bei Kundenprojekten in sehr unterschiedlichen Bereichen unterstützt. Die Ergebnisse haben uns selbst überrascht. So konnten wir bei einem deutschen Automobilisten mit SAP im Powertrain-Bereich die Produktivität um 30 Prozent steigern und die Ausschussrate erheblich reduzieren. Im Aerospace-Bereich konnten wir die Produktivität ebenfalls um fast 30 Prozent steigern, bei einem deutschen Großmaschinenhersteller sogar um fast 150 Prozent.
Mit welchen typischen Fragen werden Sie konfrontiert?
Alexander Epple: Es besteht oft die Sorge von Maschinenbedienern, Prozessentwicklern oder Qualitätsingenieuren, dass ihr Expertenwissen langfristig nicht mehr gebraucht wird. Wir sind allerdings der Meinung, dass alle wesentlichen Entscheidungen weiterhin vom Experten getroffen werden müssen. Er kennt viele Randbedingungen, die durch Daten vielleicht gar nicht abbildbar sind. Die Datenauswertung muss mit einer geeigneten Visualisierung von Maschinen- oder Prozesszuständen den Bediener bei seinen Entscheidungen bestmöglich unterstützen. Ihm wird durch die neuen Lösungen jedoch insbesondere das wenig Mehrwert stiftende, aufwändige Suchen und Vorverarbeiten einzelner Prozessinformationen erspart.
Der Aufwand bei der Metallbe- und verarbeitung ist hoch: Ließe sich virtuelles Prototyping oder Try-Out mit Hilfe von Big Data so verbessern, dass sich die Anzahl an realen Versuchen reduzieren bzw. sogar ganz eliminieren lässt?
Alexander Epple: Erhebliche Reduzierungen sind sicher möglich. Das Lernen aus Daten mit der Unterstützung von Modellen hat aus unserer Sicht ein sehr großes Potenzial.
Was erwarten Sie und Ihr Team von der EMO Hannover, der Weltleitmesse für die Metallbe- und verarbeitung? Welche Rolle wird dort Big Data spielen?
Alexander Epple: Wegen unserer Zusammenarbeit mit vielen Industriepartnern, die auch auf der EMO Hannover vertreten sind, haben wir bereits eine bestimmte Vorstellung: Ich glaube, es wird zunehmend klar, dass der Nutzen von Big Data im Bereich der Produktionstechnik durch das Einbringen von fachspezifischem Know-how erheblich gesteigert werden kann. Dies nimmt vielen Fachkräften auch die Sorge, dass ihr Expertenwissen durch Big Data bald überflüssig sein wird. Ich erhoffe mir von den Besuchern mehr Akzeptanz und von der sonst eher konservativen Branche eine gewisse Neugier. Ich freue mich daher schon auf zahlreiche konkrete Lösungsansätze.
Das Interview führte Nikolaus Fecht, Fachjournalist aus Gelsenkirchen
Downloads
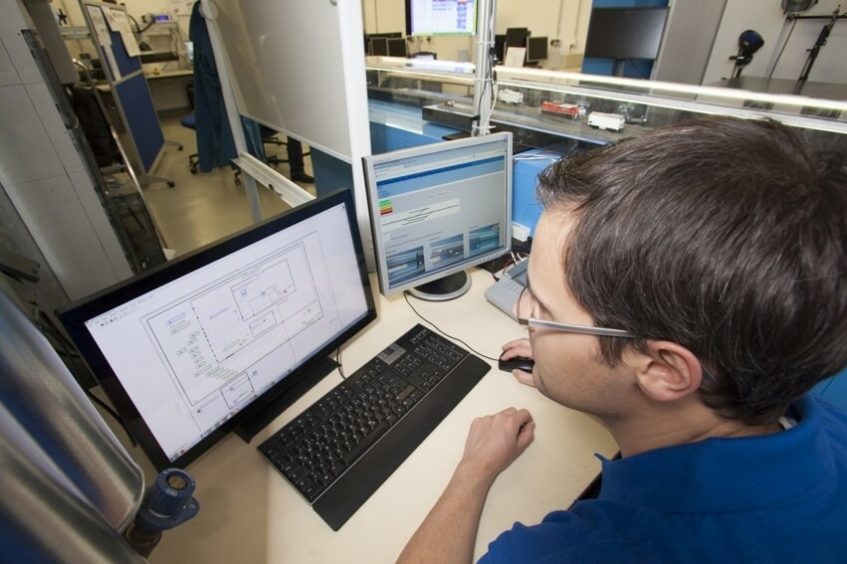