Innovative Materialien steigern Nachhaltigkeit in der Fabrik
Metallschaum und PFAS-Ersatz verbessern Umweltbilanz
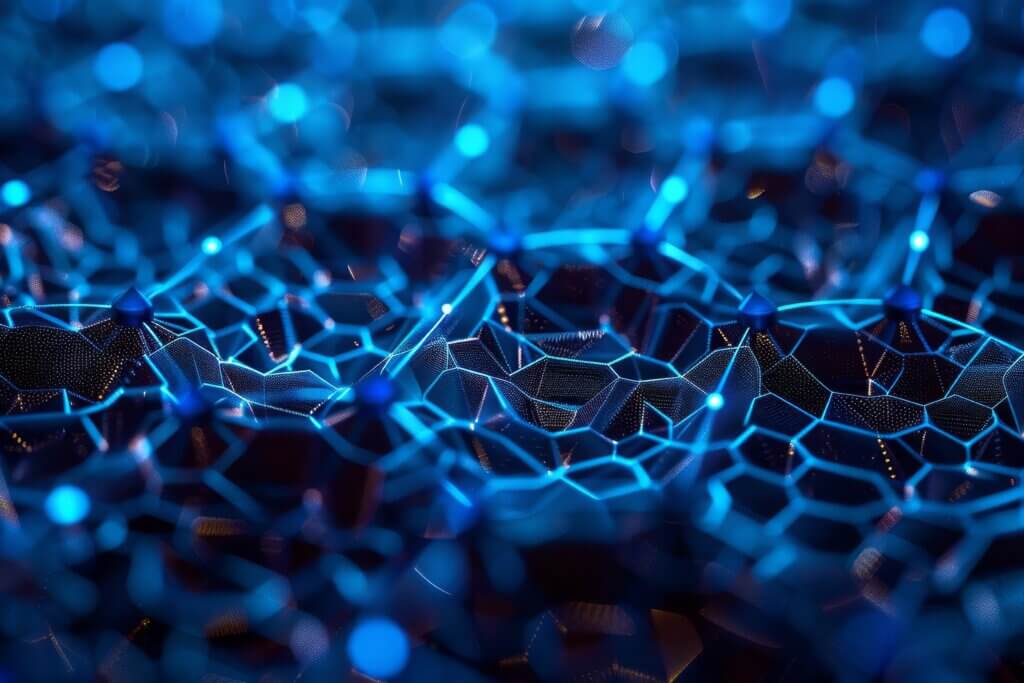
Frankfurt am Main, 16. April 2025. – Dieses Stück Metall ist so locker und leicht, das schwimmt sogar in Milch. Die Rede ist von Metallschaum. Das innovative Material enthält bis zu 90 Prozent Luft und hat verblüffende Eigenschaften. In der Fabrik sorgt es für mehr Nachhaltigkeit und trägt dazu bei, die Umweltbilanz in der industriellen Produktion zu verbessern.
Wegen steigender regulatorischer Anforderungen stehen Produktionstechnikanbieter weltweit vor der Herausforderung, leistungsfähige und umweltschonende Materialien zu integrieren. Welche Lösungen es schon gibt, wird auf der EMO Hannover 2025, der Weltleitmesse für Produktionstechnologie, vom 22. bis 26. September zu sehen sein. Besonders Metallschäume und Ersatzstoffe für per- und polyfluorierte Alkylsubstanzen (PFAS) geraten in den Fokus.
Metallschäume helfen dabei, Maschinen effizienter, leichter und gleichzeitig stabiler zu gestalten. Der hochporöse Werkstoff weist – ähnlich wie seine natürlichen Vorbilder Knochen oder Holz – eine zellulare Struktur auf, die Energie in Form von Schwingungen, Stoß oder Schall absorbieren kann.
Wie Brotbacken
Aluminiumschaum kann in einem Verfahren hergestellt werden, das im Prinzip ähnlich abläuft wie Brotbacken. Man nehme Pulver, Treibmittel und Wärme, und fertig ist der Aluminiumschaum. Im Detail gestaltet sich die Herstellung des Hightech-Werkstoffs freilich etwas komplexer. „Für die Herstellung von Aluminiumschäumen werden ein Aluminiumlegierungs- und ein Treibmittelpulver miteinander vermischt, meist durch Axialpressen vorkompaktiert und anschließend durch Strangpressen zu schäumbaren Strängen verdichtet“, erklärt Carsten Lies, Abteilungsleiter Funktionsintegrierter Leichtbau am Fraunhofer-Institut für Werkzeugmaschinen und Umformtechnik (IWU) in Chemnitz. „Für die Herstellung von Aluminiumschaum-Sandwiches werden zugeschnittene, schäumbare Aluminiumstränge zwischen zwei im Abstand zueinander positionierte Deckbleche gelegt“, beschreibt der Ingenieur den Produktionsprozess weiter.
In der nachfolgenden Wärmebehandlung expandiert das schäumbare Aluminium um ein Vielfaches. Der entstehende Schaum verbindet sich fest mit den beiden Deckblechen zu einem Sandwich. Nach dem Abkühlen wird das Sandwich auf die finalen Endabmessungen zugeschnitten. „Metallschäume, speziell Aluminiumschäume, werden vorwiegend als Kernmaterial in Sandwiches eingesetzt“, erläutert Lies. Deren Deckbleche sind üblicherweise aus Stahl oder Aluminium gefertigt. „Die Decklagen nehmen angreifende Lasten auf, der Kern hält die Bleche konstant auf Abstand“, erklärt der Fraunhofer-Forscher die besonderen Eigenschaften des Hightech-Materials. Der Verbund zwischen Decklagen und Kern erfolge meist im metallischen Stoffschluss.
Luftig, leicht und steif: Sandwich mit Schaumfüllung
„Sandwiches weisen je nach Auslegung eine sehr hohe Biegesteifigkeit auf. Dieser Effekt wird genutzt, um Baugruppen leichter zu gestalten und dabei die Steifigkeit der Baugruppe zu erhalten oder sogar zu verbessern“, sagt Lies. Sie ersetzen massive Elemente der konventionellen Baugruppe. Je nach Optimierungskriterium, so der Forscher, ließen sich entweder deutliche Gewichtseinsparungen bei gleicher Steifigkeit (bis etwa 30 Prozent) oder bei gleichbleibendem Gewicht deutliche Steifigkeitserhöhungen erreichen. Die konkreten Vorteile beim Einsatz von Metallschaum in der Maschine mit Blick auf Effizienz und Nachhaltigkeit sind laut Lies also „deutlich verbesserte Dämpfung durch den Schaumkern und deutliche Gewichtsersparnis durch Verwendung von Sandwiches“.
Positiv für die Umweltbilanz ist zudem, dass Metallschäume problemlos recycelt werden können. „Da kein Klebstoff für die Sandwichfertigung verwendet wird, kann das Material in bestehende Kreisläufe für die Aufbereitung von Metallschrott aus Stahl und Aluminium eingeschleust werden“, sagt der Forscher aus Chemnitz.
Passgenau aus dem 3D-Drucker
Bauteile aus Metallschaum – oder genauer gesagt Bauteile aus hybriden porösen (HyPo-)Materialien – lassen sich auch im 3D-Druck fertigen. Vorteil des additiv gefertigten Metallschaums: Die Luftkammern lassen sich akkurat anordnen. So erzeugte Bauteile können auf spezielle Anwendungsfälle hin optimiert werden, denn die gradierte Einstellung der Porenstruktur im Inneren des Bauteils lässt mehr Optionen zu als Luftblasen im Metall, wie sie sich beim Schäumen durch Gas bilden. So können im 3D-Drucker Maschinenkomponenten passgenau und mit exakt definierten Eigenschaften entstehen.
„Eine gradierte Einstellung von Porenstruktur und Eigenschaftsprofilen ist in einem monolithisch hergestellten Material nur schwer bis gar nicht möglich, da entweder der Herstellungsprozess oder die weitere Bearbeitung bis zur endgültigen Bauteilgeometrie nicht zu den finalen Anforderungsbedingungen der Beanspruchung passen“, erklärt Thomas Hassel vom Institut für Werkstoffkunde der Leibniz Universität Hannover (LUH). Die additive Fertigung schaffe es, so hebt der promovierte Ingenieur hervor, eine „endkonturnahe Herstellung“ von Bauteilen zu ermöglichen und gleichzeitig an den entsprechenden Stellen die Gradierung „derart einzubringen, dass diese genau im Anforderungsprofil positioniert wird“.
Welche konkreten Anwendungen es dazu im Werkzeugmaschinenbau gibt und wie das innovative Material dabei helfen kann, Effizienz und Nachhaltigkeit in der Fabrik zu steigern, ist Gegenstand der Forschung. Im Fokus stehen dabei Komponenten einer Werkzeugmaschine (Werkzeugwechsler, Werkzeughalter, Spindelschlitten) hinsichtlich ihrer Steifigkeit, Dämpfung, ihres thermoelastischen Verhaltens, ihrer Unwucht sowie ihrer Härte und Oberflächenqualität, erläutert Hassel. Durch die Implementierung der HyPo-Bauteile beispielsweise in einer Fräsmaschine wird erforscht, welche Vorteile sich durch die gradierten Bauteile ergeben. „Dabei soll das Betriebsverhalten während der Bearbeitung analysiert werden, da die Fräsbearbeitung eine große Bandbreite unterschiedlicher Lastfälle umfasst“, sagt Hassel. „Hierdurch wird es möglich, den Einfluss des HyPo-Bauteils auf die mechanischen und thermischen Maschineneigenschaften zu bestimmen und die Performance solcher Maschinen wesentlich zu verbessern.“
Ersatz für Ewigkeitschemikalien
Mehr Nachhaltigkeit durch Leichtbaumaterialien ist einer von vielen Ansätzen, um die Umweltbilanz in der industriellen Produktion zu verbessern. Verstärkt in den Blick geraten unterdessen auch umweltschonende Alternativen für so genannte Ewigkeitschemikalien. Im Fokus stehen unter anderem umweltschädliche per- und polyfluorierte Alkylsubstanzen (PFAS), die in der Produktion insbesondere dort zum Einsatz kommen, wo extreme Verhältnisse herrschen: hohe Temperaturen, starker Abrieb oder aggressive chemische Bedingungen. PFAS kommen unter anderem in Dichtungen, Leitungen oder Armaturen vor.
Ob eine Substitution von PFAS möglich ist, sei je nach Anwendungsfall „individuell zu bewerten und lässt sich nicht pauschal beantworten“, sagt Frank Schönberger, Abteilungsleitung Synthese und Formulierung am Fraunhofer-Institut für Betriebsfestigkeit und Systemzuverlässigkeit LBF aus Darmstadt. „Ein 1:1-Ersatz von Fluorpolymeren ist in der Regel nicht möglich, sondern hängt immer von den individuellen Anforderungen der jeweiligen Anwendung ab.“
Es gebe Fälle, in denen ein Fluorpolymer je nach Anforderungen durch ein anderes Hochleistungspolymer (wie PEEK, PEI oder PPS) ersetzt werden könne, zum Beispiel wenn Temperatur- und Medienanforderungen moderat seien oder im Bereich tribologischer Compounds. „Aber es gibt auch Anwendungsbereiche, in denen die komplexen Anforderungen – Stand heute – von keinem anderen Material erfüllt werden können“, schränkt der Forscher ein. „Fluorpolymere besitzen eine weitgehend universelle chemische Beständigkeit und haben eine hohe Temperaturbeständigkeit. In Anwendungen, in denen dies gefordert wird, wie in Pumpen oder Anlagen, die unterschiedlichen Medien unter verschiedenen Bedingungen standhalten müssen, sind Fluorpolymere bislang nicht zu ersetzen“, resümiert Schönberger und fügt an: „Chancen können sich in Anwendungen ergeben, in denen das volle Potenzial der Fluorpolymere nicht erforderlich ist und in Situationen, in denen beispielsweise ein Redesign möglich ist.“
PFAS-Substitution auch für USA relevant
Schönberger zufolge ist der PFAS-Ersatz auch für Märkte außerhalb Europas relevant, insbesondere in den USA. Außerdem gebe es in den Vereinigten Staaten teils vom jeweiligen Bundesstaat abhängige Regulierungen. Auch das zeigt: Mehr Nachhaltigkeit in der Produktionstechnik ist eine globale Herausforderung, auf die in den Fabriken in allen Industrienationen reagiert werden muss.
Kontakte
VDW
Gerda Kneifel
Presse- und Öffentlichkeitsarbeit
Lyoner Str. 18
60528 Frankfurt am Main
Deutschland
g.kneifel@vdw.de
Tel. +49 69 756081-32
www.vdw.de
Fraunhofer-Institut für Werkzeugmaschinen und Umformtechnik IWU
Carsten Lies
Abteilungsleiter Funktionsintegrierter Leichtbau
Reichenhainer Str. 88
09126 Chemnitz
Deutschland
Carsten.Lies@iwu.fraunhofer.de
Tel. +49 371 5397 1941
https://www.iwu.fraunhofer.de/
Institut für Werkstoffkunde Leibniz Universität Hannover (LUH)
Dr. Thomas Hassel
Bereichsleiter Unterwassertechnikum Hannover
Lise-Meitner-Straße 1
30823 Garbsen
Deutschland
hassel@iw.uni-hannover.de
Tel. +49 511 762 9813
https://www.iw.uni-hannover.de/de/
Fraunhofer-Institut für Betriebsfestigkeit und Systemzuverlässigkeit LBF
Dr. Frank Schönberger
Abteilungsleitung Synthese und Formulierung
Schlossgartenstr. 6
64289 Darmstadt
Deutschland
frank.schoenberger@lbf.fraunhofer.de
Tel. +49 6151 705-8705
https://www.lbf.fraunhofer.de/
Daniel Schauber
Fachjournalist
Meerfeldstr. 14
68163 Mannheim
Deutschland
daniel@schauber.com
Tel. +49 1702031976