Wenn die Laserschrift den Rundlauf stört
Auch wenn die digitale Transformation zunehmend alle Bereiche der METAV 2018 beflügelt, steht eines fest: Selbst der hochmoderne, digitalisierte Metallverarbeiter verdient immer noch mit der Schneide sein Geld. Worauf es hier bei Mikrowerkzeugen für den Werkzeug- und Formenbau ankommt, berichtet der badische Werkzeugfabrikant Stefan Zecha, Geschäftsführer und Geschäftsführender Gesellschafter der Zecha Hartmetall-Werkzeugfabrikation GmbH aus Königsbach-Stein. Das Unternehmen stellt in der Moulding Area aus.
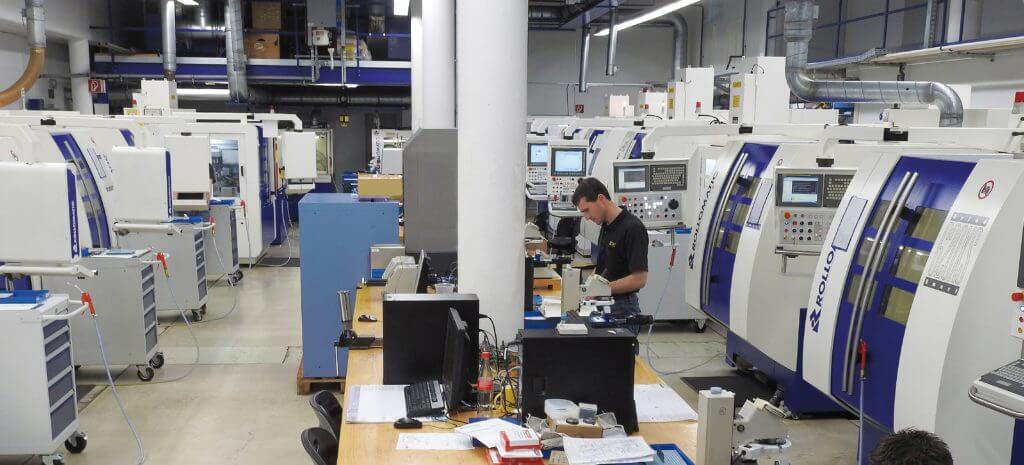
Herr Zecha, zu Ihren Kunden zählen Unternehmen aus dem Werkzeug- und Formenbau: Welche Anforderungen stellt diese Branche an die Zerspanungswerkzeuge?
Stefan Zecha: Wir stellen Präzisionswerkzeuge mit Mikrometer-Genauigkeit her, bei denen der Werkzeug- und Formenbau nicht nur auf hohe Wiederholgenauigkeit, sondern auch auf pünktliche und schnelle Lieferung der Produkte wert legt.
Wie weisen Sie dieser bekanntlich sehr qualitätsbewussten Branche die Einhaltung der Qualität bei Ihren Bohrern, Fräsern, Gewindewirblern und Reibahlen nach?
Stefan Zecha: Wir bringen seit über zehn Jahren mit dem Laser auf jedem Werkzeug eine Nummer an, mit der sich rückverfolgen lässt, wer es wann unter welchen Bedingungen aus welchem Hartmetall-Rohling gefertigt hat und wo das entsprechende Protokoll zum Fertigungsprozess und den Messungen gespeichert ist. Anhand der so genannten Lebensnummer lässt sich also ein Werkzeug auch Jahre nach einem Kundenauftrag eindeutig zuordnen. Wir beschriften das Schaftende und nicht wie andere den Schaft.
Warum bringen Sie die Identnummer nicht auf dem Schaft an?
Stefan Zecha: Werkzeug- und Formenbau setzen bei Werkzeugen auf optimale Rundlaufeigenschaften, die ein gelaserter Schaft nicht erfüllen kann, weil die Oberfläche dann nicht mehr ganz glatt ist. Wegen der hohen Ansprüche fertigen wir übrigens auch alle unsere Schäfte selbst, denn am Schaft fängt die Präzision an.
Stefan Zecha: Was ist Ihr Erfolgsrezept?
Stefan Zecha: Für hohe Qualität sorgt die konsequente Einkaufspolitik. Wir kaufen unser Hartmetall stets bei den gleichen Lieferanten ein. Es kommt also nicht vor, dass wir aus Kostengründen irgendwo in der Welt Hartmetall ordern. Ebenso setzen wir auch bei der Beschichtung nur auf langjährige Partner, mit deren Entwicklungsabteilungen wir eng zusammenarbeiten. Doch bis auf die Beschichtung geschieht die Produktion ansonsten in eigener Regie in hoher Fertigungstiefe. Daher schleifen wir auch selbst. Ein Werkzeug mit einem Durchmesser von einem Millimeter und weniger verzeiht keine Fehler im Bereich von Tausendstel von Millimetern (µm).
Eine Ihrer Spezialitäten ist die Kantenpräparation, mit deren Präzision der spätere Zerspanungserfolg steht und fällt: Wie genau können Sie die Schneidkanten in die gewünschte Form bringen?
Stefan Zecha: Wir können sie auf 0,5 bis 0,8 µm exakt präparieren und nur so gleichbleibende Qualität garantieren.
Warum arbeiten Sie in Sachen Graphitbearbeitung mit einem Diamantbeschichter, einem Maschinenhersteller und einem Elektrodenproduzenten zusammen?
Stefan Zecha: Wir müssen heute immer häufiger nicht nur das Werkzeug liefern, sondern zunehmend auch den gesamten Prozess im Blick haben. Dazu gehört zum Beispiel, die Schnittdaten zu ermitteln. Die drei Firmen sind auf unterschiedliche Weise sehr nah an der gesamten Prozesskette dran. Vor allem in Sachen Beschichtungen ist für uns die Zusammenarbeit mit anderen Firmen sehr wichtig, denn heute gibt es im Jahrestakt neue Beschichtungen, auf die wir uns einstellen müssen. Wir testen daher alle infrage kommenden Beschichtungen sehr genau, bevor wir dann Beschichtungen rund drei bis fünf Jahre auf unseren Werkzeugen einsetzen.
Welche Rolle spielen die METAV bzw. die Moulding Area für Sie?
Stefan Zecha: Ich bedaure, dass es bei den Messen vor allem zu diesem Thema einen Trend Richtung Süden gibt. Ich bin daher froh, dass die METAV den Werkzeug- und Formenbau mit der Moulding Area mit einem eigenständigen Themenbereich aufgreift.
Was werden Sie in Düsseldorf an Innovationen für den Werkzeug- und Formenbau sowie andere Branchen vorstellen?
Stefan Zecha: Wir stellen Kugel-, Torus- und Schaftfräser vor, die – dank gezielter Bearbeitung der Schneidkanten mit Lasertechnik (R=1μm) und der speziellen Schneidengeometrie – die Schnittkräfte und Wärmeentwicklung erheblich senken. In Düsseldorf präsentieren wir hier eine Spezialentwicklung für Kupferelektroden.
Das Interview führte Nikolaus Fecht, Fachjournalist aus Gelsenkirchen