Technischer Abschlussbericht: EMO Hannover weist Blick in die Zukunft der Produktion
Die diesjährige EMO Hannover fand vom 16. bis 21. September 2019 unter dem Motto Smart technologies driving tomorrow’s production! statt. Auf der Weltleit-messe der Metallbearbeitung wurden zukunftsweisende Themen wie die digitale Vernetzung von Werkzeugmaschinen, das industrielle Internet der Dinge (IIoT) und die universelle Maschinenschnittstelle umati präsentiert. Dass der digitalen Transformation im Bereich der Werkzeugmaschinen eine immer größere Bedeu-tung zukommt, zeigten zahlreiche Aussteller und verknüpften ihre Werkzeugma-schinen mit innovativen Softwarelösungen.
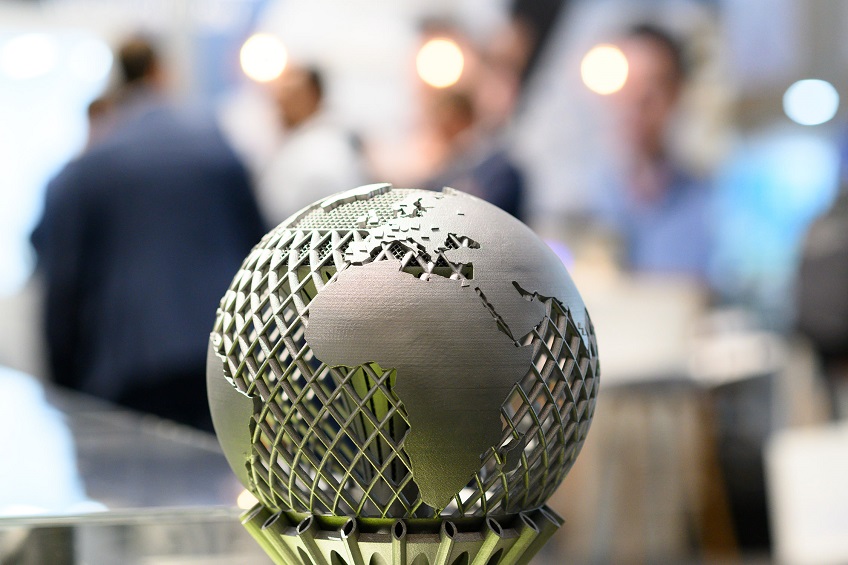
Werkzeugmaschinen
Die Liebherr-Verzahntechnik GmbH aus Kempten folgt dem Trend zur Integration verschiedener Arbeitsvorgänge in eine Verzahnungsmaschine. Ein Highlight, das der Verzahnungsspezialist auf der EMO Hannover präsentierte, war die Verzahnungsmaschine LK 280 DC. Sie ermöglicht durch die Kombination des Wälzschälprozesses und einer automatisierten, hauptzeitparallelen Entgratung die Komplettbearbeitung von Zahnrädern, die in hohen Stückzahlen beispielsweise in der Automobilbranche und im Getriebebau benötigt werden. Die Maschinenbedienung erfolgt über das Programmiersystem LHGearTec, das in die Steuerung eingebunden ist. Diese bietet zudem Zugriff auf die Online-Plattform von Liebherr, über die weitere hilfreiche Zusatzfunktionen, sogenannte LH-Services, abrufbar sind. Dazu zählen unter anderem die Fernüberwachung des Live-Status von Maschinen im Feld. Ein anderes Highlight ist der digitale Maschinenzwilling. Dieser ist besonders im Entwicklungsstadium der Maschine von entscheidendem Vorteil. So können der mechanische Aufbau sowie die Kinematik bereits vor der realen Umsetzung kontrolliert, optimiert und die Bearbeitungszeiten virtuell gemessen werden.
Die steigende Nachfrage nach Automatisierungslösungen beflügelt insbesondere auch die Nachfrage nach Industrierobotern. Diese benötigen zur Realisierung hoher Untersetzungen hochpräzise Zykloidenverzahnungen. Bei ihrer Fertigung ist die Einhaltung hoher Genauigkeiten im einstelligen Mikrometerbereich bei der Bearbeitung der Bohrungen und des Zahnprofils entscheidend. Die Bearbeitungsmaschine Viper 500 MFM des Maschinenherstellers Klingelnberg aus Hückeswagen erfüllt diese Aufgabe, die mit Standardmaschinen- und Standardbearbeitungszyklen nicht zu bewältigen ist, besonders zeiteffizient. Dabei werden in einer Aufspannung bis zu vier Zykloidenverzahnungen gleichzeitig geschliffen. Ein Vorteil der Maschine ist die integrierte Messeinrichtung. Sie ermöglicht die individuell nachvollziehbare Kontrolle und Dokumentation der gefertigten Zykloidenverzahnungen. Sollte ein Bearbeitungsergebnis die Sollvorgaben nicht erfüllen, dann berechnet die Messsoftware Korrekturwerte. Diese werden für eine direkte Nachbearbeitung und zur Einhaltung der Toleranzvorgaben automatisch an die Maschinensteuerung übergeben. Der Maschinenbediener muss dazu lediglich eine Freigabe erteilen. Aufwändiges Handling, Anpassung des Prozesses sowie die manuelle Übertragung der Korrekturwerte entfallen.
Als Reaktion auf die zunehmende Bedeutung der E-Mobilität stellt Emag aus Salach auf der EMO Hannover innovative Fertigungslösungen für Komponenten von E-Motoren vor. Die Rotoren von Elektromotoren, die aus Blechpaketen zusammengeschweißt werden, müssen anschließend auf der Mantelfläche nachbearbeitet werden. Die Anforderungen an die hierbei zu erzeugende Oberflächenqualität liegen in einem Bereich, bei dem ein konventioneller Außenlängsdrehprozess nur mit geringem Vorschub eingesetzt werden kann. Durch den Einsatz eines Schäldrehprozesses, bei dem eine Abwälzbewegung des Werkzeugs auf dem Werkstück stattfindet und sich somit der Schneideneingriffspunkt kontinuierlich verschiebt, können Oberflächen ohne den beim Drehen üblichen Drall erzeugt werden. Die Qualität der dabei erzielten Oberflächen kann sonst nur mittels einer Schleifbearbeitung erreicht werden. Zudem kann durch den hohen realisierbaren Vorschub die Prozesszeit im Vergleich zu alternativen Bearbeitungsprozessen deutlich reduziert und so die Wirtschaftlichkeit gesteigert werden.
Neben der mechanischen und elektrochemischen Bearbeitung zeigt Emag auch Maschinen zum Laserschweißen, Laserreinigen und Laserstrukturieren: Durch eine Kombination aus Laserreinigen – also dem Entfernen von Schmutz oder Ölrückständen auf den Bauteilen und anschließendem Strukturieren der Oberfläche auf einer Maschine – können Oberflächen für das Fügen von Bauteilelementen durch Kleben oder für das Lackieren vorbereitet werden. Ein entscheidender Vorteil dieses Verfahrens gegenüber dem Sandstrahlen besteht darin, dass die Bauteile nach dem Laserstrukturieren nicht kostenintensiv gereinigt werden müssen.
Krause + Mauser aus Oberndorf am Neckar ist bekannt als Spezialist für Fertigungslösungen für die Automotivebranche. Auf der EMO Hannover stellt das Unternehmen unter anderem innovative Entwicklungen für die CNC-Feinbohrbearbeitung von Pleueln vor. Bisher war es bereits mit dem 2D-Formbohren möglich, eine Trompetenkontur oder Ovalform mit einer Toleranz von wenigen Mikrometern in das kleine Pleuelauge einzubringen, um die Schmierung an dieser Lagerstelle zu verbessern und Reibung zu minimieren. Ein neuentwickelter 3D-Piezobohrkopf mit aussteuerbarer Schneide macht nun auch ein definiertes Unrundbohren im Mikrometerbereich möglich, wodurch die Reibungseigenschaften an der Lagerstelle nochmals verbessert werden. Hierbei lassen sich Ovale oder 3D-Freiformen erzeugen und systematische Formfehler durch Schnittkräfte oder aus Spanneinflüssen ausgleichen.
Die Index-Werke GmbH, Esslingen am Neckar, stellt einen neuentwickelten doppelspindligen Produktionsdrehautomaten vor, der die einspindligen Drehautomaten aus der C-Baureihe ergänzen soll. Durch das tandem genannte Maschinenkonzept mit jeweils zwei baugleichen Haupt- und Gegenspindeln wird die Teileausbringung verdoppelt, ohne dass der Aufwand für Aufstellfläche oder Personal erhöht werden muss. Die Maschine schließt damit eine Lücke zwischen den Einspindel- und den Mehrspindeldrehautomaten. Eine weitere Neuerung aus den Index-Werken ist die zyklusintegrierte Spänebruch-Software ChipMaster. Diese kann auf Index-Drehmaschinen mit aktuellen Siemens-Steuerungen eingesetzt und ggf. nachgerüstet werden. Die Software sorgt durch eine Vorschubvariation für Unterbrechungen in der Spanbildung und kann so die Bildung von langen Fließspänen verhindern. Der Zyklus ist unabhängig vom verwendeten Werkstückmaterial einsetzbar und bietet eine einfache und kostengünstige Lösung, unter anderem um ungeplante Eingriffe des Maschinenbedieners zur Entfernung von Fließ- und Wirrspänen zu vermeiden.
Bei der Gebr. Heller Maschinenfabrik GmbH aus Nürtingen stehen die drei Themen Digitalisierung, Globalisierung mit Kundennähe und neue Geschäftsmodelle im Fokus. Auf der Messe präsentiert der Maschinenhersteller drei neue Maschinen, u. a. die H 2000 und HF 3500. Das 4-Achs-Bearbeitungszentrum H 2000 ist dabei durch Maßnahmen zur Gewichtsreduzierung und Steifigkeitserhöhung produktiver als seine Vorgängermodelle. Erreicht wurde dies durch Topologie-optimierte Gussstrukturen von Bett und Ständer. Das 5-Achs-Bearbeitungszentrum HF 3500 ermöglicht mit dem Speed-Dynamik-Paket eine Steigerung der Dynamik und somit eine Produktivitätssteigerung bei der simultanen 5-Achs-Bearbeitung. Des Weiteren ist das Bearbeitungszentrum durch einen kollaborierenden Roboter von Fanuc in Kombination mit einem Greifersystem von Schunk um eine Automatisierungslösung erweitert worden. Diese werden im modernen Produktionsumfeld, auch bedingt durch den fortschreitenden Fachkräftemangel, zunehmend wichtiger. Auf dem globalen Markt plant Heller, als Basis lokal zugeschnittene Automatisierungslösungen einzusetzen und diese mit Heller-eigenen Applikationen zu erweitert.
Im Bereich der Werkzeugmaschinen für die Präzisionsfertigung stellt die Fa. Kern Microtechnik GmbH aus Eschenlohe ihre neueste Entwicklung aus der Baureihe Kern Micro vor. Das Modell Kern Mikro HD verhindert durch ein optimiertes Temperaturmanagement mit aktiver Temperierung der Maschinenkomponenten zuverlässig Genauigkeitsabweichungen durch Temperatureinflüsse. Durch ein einzigartiges Antriebssystem mit einer Kombination aus Linearmotorantrieben und Mikrospalt-Hydrostatik werden hohe Dynamik und Produktivität, höchstmögliche Bauteilqualität sowie Verschleißfreiheit der Antriebsachsen erreicht. Trotz eines kompakten Maschinendesigns mit einem Platzbedarf von weniger als 5 m², sind Wechsler mit einem Magazin für bis zu 210 Werkzeuge und 60 Werkstücke integriert, wodurch ein mannloser Mehrschichtbetrieb der Maschine möglich ist.
Digitalisierung und Automatisierung
Die Standardschnittstelle umati (universal machine tool interface) war auf der EMO Hannover 2019 nahezu allgegenwärtig. Zahlreiche über das Messegelände verteilte Maschinen, die mit dem umati-Logo gekennzeichnet waren, legten bereitwillig ihre Live-Daten, z.B. die aktuelle Spindeldrehzahl oder den Bearbeitungszustand, offen. Diese konnte sich jeder interessierte Messebesucher bequem durch Aufruf der umati-Internetseite, beispielsweise über das eigene Smartphone, während der Messe anzeigen lassen. An dem Showcase beteiligten sich 70 Unternehmen aus zehn Ländern, die 110 Maschinen und 28 Mehrwertdienste miteinander vernetzten. Die erfolgreiche Umsetzung sowie der robuste Betrieb über die gesamte EMO-Woche mit Tausenden gleichzeitiger Zugriffe auf die Live-Daten bestätigten, dass umati funktioniert. Der nächste Meilenstein ist die Veröffentlichung der Version 1.0 des OPC UA-Standards, die Mitte des Jahres 2020 erwartet wird.
Der Werkzeugmaschinenhersteller DMG Mori zeigte auf der EMO Hannover, wie mit seinen Produkten die gesamte Fertigungskette von Planung und Vorbereitung bis zu Produktion, Monitoring und Services digitalisiert werden kann. Dazu wurden über 30 digitale Innovationen vorgestellt. Für diesen Weg hin zur digitalen Fabrik und ihren Vorzügen, wie zum Beispiel einer höheren Transparenz durch kontinuierliche Dokumentation und Erfassung von Daten im Shopfloor, sei Konnektivität eine Grundvoraussetzung. Daher sollen ab der EMO Hannover 2019 alle neuen DMG Mori Maschinen im Rahmen des DMG Mori Connectivity Programms kostenlos mit einer IIot (Industrial Internet of Things) -Schnittstelle ausgestattet werden. Sie ermöglicht die Anbindung an eine Vielzahl von IoT-Platformen (Internet of Things), zu denen unter anderem Adamos, MindSphere und Fanuc Field zählen. Darüber hinaus präsentierte der Werkzeugmaschinenhersteller mehr als die Hälfte seiner 45 EMO-Exponate mit Automationslösungen. Zu den Highlights zählt beispielsweise das fahrerlose Transportsystem PH-AGV 50, das selbst in bereits bestehenden Produktionsbereichen für das autonome Paletten-Handling einsetzbar ist. Eigenen Angaben zufolge habe bei DMG Mori die Neuentwicklung von Automationslösungen inzwischen denselben Stellenwert wie die Entwicklung neuer Maschinenmodelle.
Der Anbieter von Linearführungen THK aus Minato, Japan, hat in einer anwendungsorientierten Entwicklung Sensormodule für seine Linearführungen und Kugelgewindetriebe (KGT) entwickelt. Das Sensormodul kann nachträglich auf bereits bestehende Linearführungen installiert werden, auf dem es dann Vibrationen im Einsatz misst. THK schließt mittels dieser Vibrationsmessungen und dem zugehörigen IoT-Service Omni edge auf den Systemzustand und nutzt die gewonnenen Informationen zur Überwachung und Fernwartung seiner Komponenten.
Werkstückspanntechnik
Jeder Zerspanprozess auf einer Werkzeugmaschine erfordert den Einsatz von Spanntechnik, die das Werkstück während der Bearbeitung sicher in Position hält. Aus den auf der EMO Hannover präsentierten Neuheiten kristallisierten sich insbesondere zwei Trends heraus: die Erleichterung der Handhabung zur Reduzierung unproduktiver Nebenzeiten und die Integration von Elektronik in Spannelemente zur Unterstützung übergeordneter Automatisierungssysteme.
Auf ihrem Messestand stellte die Schunk GmbH & Co. KG, Experte für Greifsysteme und Spanntechnik aus Lauffen am Neckar, gleich mehrere Neuheiten aus. Hierzu zählt der elektrische Kraftspanner KSE 100, der über eine integrierte Spannwegmessung die korrekte Einspannung überwachen kann. Mit dem Nullpunktspannsystem NSE S3 hat Schunk ein Spannelement präsentiert, das die Abfrage des Spannzustands ermöglicht. Dies ist zur Quittierung der erfolgreichen Werkstückübergabe, insbesondere bei automatisierten Beladevorgängen hilfreich. Neben der binären Quittierung misst das Nullpunktspannelement NSE S3 zusätzlich über integrierte Sensorik die Spannkraft. Sie ermöglicht die Kontrolle der zum Spannen von Bauteilen benötigten Kraft und die Gewinnung von Trendinformationen für vorbeugende Instandhaltungsmaßnahmen.
Der Spanntechnikhersteller Römheld GmbH aus Laubach baut seine Digitalisierungslösungen weiter aus. Mit integrierter Wegabfrage erstmals ausgestattete, hydraulische Linearaktoren und Schwenkspanner ermöglichen die Überwachung der Werkstückhöhe. Diese ist z. B. bei Gussbauteilen sinnvoll, deren Geometrie aufgrund des Gießprozesses großen Schwankungen bis in den Millimeterbereich unterliegen können. Die Spannelemente kontrollieren an den Spannpunkten die Werkstückgeometrie mit einer Genauigkeit von einem zehntel Millimeter direkt beim Spannen. Eine Gewinnung vergleichbarer Informationen mit konventionellen Wegmesssystemen im beengten Arbeitsraum der Werkzeugmaschine ist in der Regel zu aufwendig und häufig nicht möglich.
Das Unternehmen Andreas Maier GmbH & Co. KG aus Fellbach stellt einen neuen Greifer vor, mit dem die Werkzeugmaschine selbstständig Handlingaufgaben übernehmen kann. Für diese Automatisierungsanwendung werden normalerweise Roboter eingesetzt. Die Besonderheit des Greifers ist, dass er wie ein Zerspanwerkzeug in die Arbeitsspindel der Werkzeugmaschine eingewechselt und im Werkzeugmagazin aufbewahrt werden kann. Die Betätigungsenergie bezieht der Greifer über Druckluft oder alternativ über die Kühlschmierstoffzufuhr. Mindestens eine der beiden Energiequellen ist in der Regel in Werkzeugmaschinen vorhanden. Die Spannkraft ist in beiden Fällen stufenlos einstellbar. Eine elektrische, batteriebetriebene Abfragemöglichkeit ist ebenfalls implementiert. Diese kontrolliert den Greifvorgang und quittiert per Funk, ob er erfolgreich verlief.
Eine Innovation, die ohne Elektronik auskommt, präsentiert die Hainbuch GmbH aus Marbach mit dem CentroteX S. Hinter diesem Begriff verbirgt sich ein Schnellwechselsystem für Drehspannfutter. Während selbst ein schneller Wechsel bei konventionellen Spannfuttern mehrere Minuten dauert, ermöglicht das neue Wechselsystem einen Spannmitteltausch in weniger als einer Minute. Die Wiederholgenauigkeit ist dabei mit zwei Mikrometern sehr hoch.
Präzisionswerkzeuge
Sandvik Coromant aus Sandviken in Schweden, präsentiert ein neuentwickeltes indexierbares Bohrkonzept, das Bohrungen mit einer Tiefe bis zum Siebenfachen des Bohrdurchmessers (7xD) erreichen kann. Für den CoroDrill® DS20 genannten Wendeschneidplattenbohrer wurde das Design des Grundkörpers und der Wendeschneidplatten neu gestaltet. Dies führt zu einer verbesserten Prozesssicherheit durch geringere Kräfte und leichteres Schneiden, insbesondere beim Eintritt ins Material. Durch die Steigerung der Bohrtiefe kann das Bohren von beiden Seiten eines Bauteils überflüssig werden, wodurch Zeit und Kosten gespart und die Qualität der Bohrung verbessert werden. Ein wichtiger Aspekt bei der Entwicklung war die Reduzierung der Geräuschemissionen, was durch das Design des Werkzeugkonzeptes und die Reduzierung der auftretenden Torsionsschwingungen gelungen ist. Ergänzend bringt Sandvik Coromant eine neue MDI (Modular Drilling Interface) –Schnittstelle auf den Markt. Durch den modularen Aufbau der Kupplung zwischen Bohrer und Adapter kann ein Interface für mehrere Bohrer-Durchmesser verwendet werden. Eine Doppelzentrierung mit hoher Passgenauigkeit ermöglicht eine optimale Rundlauf- und Wiederholgenauigkeit.
Das Emuge-Werk Richard Glimpel GmbH & Co. KG, Lauf a.d. Pegnitz, hat in Kooperation mit Audi, Ingolstadt, eine neue Gewindetechnologie entwickelt, mit der die Zeit für die Fertigung von Gewindebohrungen deutlich reduziert werden kann. Bei der konventionellen Fertigung von Gewinden wird mit zwei Schritten gearbeitet, dem Vollbohren und dem anschließenden Einbringen des Gewindes. Bei der neu entwickelten Taptor-Technologie können das Vollbohren und die Gewindefertigung in einem Arbeitsschritt erfolgen. Durch den Wegfall eines bisher notwendigen Vorbohrens und des Werkzeugwechsels ergibt sich ein deutlicher Zeitvorteil des neuen Verfahrens, wodurch Maschinenkapazität eingespart werden kann. Zusammen mit Audi wird die Technologie in die Serienproduktion von Guss-Aluminium-Bauteilen eingebunden.
Als Spezialist für Tiefbohrwerkzeuge präsentiert die botek Präzisionsbohrtechnik GmbH aus Riederich einen innovativen Schritt zum ressourcenschonenden Umgang mit verschlissenen Werkzeugen. Zukünftig wird es dank botek möglich sein, verschlissene Vollhartmetall (VHM)-Einlippenbohrer vom Typ 113 und 113-HP mit einem neuen Hartmetallkopf zu bestücken. Eine Neubestückung von Einlippenbohrern war bisher nur bei Werkzeugen mit Stahlschaft möglich. Durch das neu entwickelte Verfahren kann der Hartmetallschaft der Werkzeuge nun mehrfach wiederverwendet werden. Die Eigenschaften der Werkzeuge bezüglich Produktivität, Prozesssicherheit und Bearbeitungsqualität werden dadurch nicht beeinflusst. Auch die Möglichkeit des Nachschleifens der Werkzeuge besteht weiterhin. Eine Neubestückung der VHM-Einlippenbohrer ist in einem Durchmesserbereich von 5,0 bis 12,0 mm möglich und hilft dem Kunden, Energie, Material und dadurch Kosten zu sparen.
CAD / CAM und Steuerungssoftware
Ein besonderes Highlight in der Steuerungstechnik ist die Sinumerik One der Siemens AG, München. Durch ihren digitalen Zwilling hilft sie bei der digitalen Transformation, indem Arbeitsprozesse vollständig virtuell simuliert und getestet werden können. Als einziges österreichisches Unternehmen und als einer von wenigen Maschinenbauern beteiligt sich die Fill GmbH aus Gurten als Entwicklungspartner an der Sinumerik One. Auf der EMO Hannover 2019 präsentierte Fill das mit der Sinumerik One-Steuerung ausgestattete Bearbeitungszentrum syncromill h21-63/500, das speziell für die Bearbeitung von Rahmenstrukturbauteilen unter anderem für die E-Mobilität entwickelt wurde.
Aus dem Bereich der CAM-Lösungen präsentiert die SolidCAM GmbH aus Schramberg die neuen Funktionen ihrer SolidCAM 2019-Software. Mit dieser wird die schnelle und einfache Programmierung von Werkzeugmaschinen, auch mehrkanaligen Drehfräszentren und CNC-Langdrehautomaten, ermöglicht. So lassen sich mithilfe der integrierten Maschinensimulation auch komplexe Maschinen mit einer beliebigen Anzahl an Achsen für die Simulation und Verifikation der Bearbeitungen virtuell abbilden. Dabei wird die zur Verfügung stehende Maschinendatenbank ständig erweitert. Ergänzt wurde die Software um Funktionen, mit denen sich beispielsweise beim Tiefbohren die Drehzahl des Werkzeugs für jede beliebige Bohrtiefe einstellen lässt. Die Zahl der unterstützten Typen der Werkzeuge für die 5-Achs Simultanbearbeitung wurde erweitert, so dass nun alle Typen von Kreissegmentfräsern, unter anderem für Tonnen-, Linsen-, Tropfen und Kegelform verwendet werden können.
DP Technology, Camarillo USA, stellt die Neuerungen seiner CAM-Software Esprit vor. Diese unterstützt mit Esprit-Additive die Programmierung von Maschinen für die additive Fertigung sowie Hybridmaschinen mit einer Kombination aus additiver und subtraktiver Bearbeitung. Durch die Software können sowohl spezialisierte Werkzeugbahnen für additive Fertigungsprozesse wie das Laserauftragsschweißen generiert werden, als auch für die subtraktive Nachbearbeitung der erzeugten Bauteile. Ein weiteres Highlight des Esprit CAM-Systems ist die Integration von Algorithmen, die auf Künstlicher Intelligenz (KI) basieren und das Programm automatisch optimieren. Hierdurch können die Programmierprozesse vereinfacht und die Maschinenproduktivität erhöht werden.
Fertigungstechnik für Elektromobilität
Die Elektrifizierung des Antriebsstrangs stellt auch für die Entwicklung neuer Fertigungslösungen und Werkzeugkonzepte interessante Herausforderungen dar. Dabei ist die Fertigung von Elektromotoren, die in Hybrid- oder Vollelektroautos verbaut werden, von entscheidender Bedeutung. Mit den derzeit steigenden Stückzahlen müssen bei der Herstellung der Komponenten für E-Motoren die Fertigungsprozesse effizient gestaltet werden.
In diesem Kontext präsentiert Ceratizit Luxembourg S.à.r.l., Mamer, Luxemburg, mehrere innovative Werkzeugkonzepte, mit denen Aluminiumgehäuse von Elektromotoren präzise und effizient bearbeitet werden können. Die Herausforderung besteht darin, die Statorbohrungen mit einem Durchmesser von etwa 200 mm bis 300 mm in einer Tiefe von über 300 mm präzise zu bearbeiten. Die Werkzeuge müssen hierbei in Leichtbauweise hergestellt werden, um die zulässige Last der Maschinenspindeln nicht zu überschreiten. Eine der Werkzeuglösungen, die diesen Anforderungen gerecht wird, ist ein auf der EMO Hannover ausgestelltes, vollständig additiv hergestelltes Feinbohrwerkzeug. Hier wurde die generative Fertigung genutzt, um filigrane, verstrebte Strukturen des Grundköpers so zu gestalten, dass ein relativ leichtes und trotzdem steifes Werkzeug realisiert werden kann. Mit diesem lassen sich die Statorbohrungen in einem Schritt bearbeiten und IT6-Toleranzen sowie geforderte Rundheiten im Bereich von bis zu 2/100 mm einhalten.
Als weiteres Konzept eines Feinbohrwerkzeugs stellt Ceratizit eine Kunststoff-Stufenbohrstange vor, die kostengünstiger und durch modularen Aufbau einfach herstellbar ist. Dieses Werkzeug besteht aus einem rohrförmigen Leichtbau-Grundkörper, der konventionell mit zerspanenden Verfahren hergestellt wird. Auf diesen Grundkörper werden additiv hergestellte Stufen appliziert, welche PKD (Polykristalliner Diamant) oder mit Wendeschneidplatten bestückte Kassetten enthalten und so den bearbeitenden Durchmesser der Statorbohrung realisieren. Diese Stufen bestehen aus einem speziell entwickelten, faserverstärkten Kunststoff und sind in der Lage, entstehende Bearbeitungskräfte gezielt in den Grundkörper abzuleiten. Durch den modularen Aufbau aus Grundkörper und Stufen lässt sich das Werkzeug schnell und kostengünstig an die Kundenanforderungen anpassen.
Additive Fertigung
Mit der zunehmenden Bedeutung der additiven Fertigung in der Massenfertigung steigt die Nachfrage nach automatisierten additiven Fertigungsprozessen. Hierzu hat der schweizerische Werkzeugmaschinenhersteller GF Machining Solutions, Biel, mit der DMP Flex 350 eine neue Maschine für den 3D-Metalldruck vorgestellt, die besonders durch ihre hoch reproduzierbare Bauteilqualität und Automatisierbarkeit hervorsticht. Die Qualität wird erreicht, indem bei dem pulverbettbasierten Verfahren vor dem Einlassen des Schutzgases ein Vakuum hergestellt wird. Dadurch wird die sauerstoffhaltige Luft sogar aus den Pulverzwischenräumen entzogen und prozessstörende Reaktionen mit derselben verhindert. Nach dem 3D-Druck kann die dichte Vakuumkammer mitsamt dem Pulver und den Bauteilen automatisiert aus der Maschine entnommen werden. Der Vorteil dabei sind kurze Umrüstzeiten, da die Maschine nach dem Einsetzen einer neuen Vakuumkammer direkt mit dem nächsten Druckprozess beginnen kann. Das Blockieren der Maschine durch zeit- und aufwandsintensive Bauteilentnahmen, die unter anderem auf die Handhabung der feinen und gesundheitsschädigenden Pulverpartikel zurückzuführen sind, entfällt.
Fazit
Die EMO Hannover 2019 machte deutlich, dass der Wandel zur Digitalisierung kontinuierlich fortschreitet und die damit einhergehenden Vorteile nicht zuletzt aufgrund zunehmend besserer Konnektivität in den metallbearbeitenden Prozessen häufiger genutzt werden. Offene Schnittstellen erhöhen zudem die Transparenz, besonders bei interdisziplinär agierenden Systemen, und stellen eine höhere Fertigungsflexibilität sicher. Für eine wirtschaftliche Produktion in künftigen Fertigungsabläufen, die von noch geringeren Losgrößen und steigender Nachfrage nach Automatisierungslösungen geprägt sein dürften, ist eine solche Flexibilität von hoher Bedeutung.
Autoren
Johann Kiesner, Dipl.-Ing., Institut für Fertigungstechnik und Werkzeugmaschinen (IFW), Leibniz Universität Hannover,
Tel. +49 511 762 5210, E-Mail kiesner@ifw.uni-hannover.de
Jan Nickel, M.Sc., Institut für Spanende Fertigung (ISF), Technische Universität Dortmund,
Tel. +49 231 755 6426, E-Mail jan.nickel@tu-dortmund.de
Downloads
Dokumente