Virtuelles Ebenbild: Der digitale Zwilling
Industrie 4.0, digitalisierte Daten in der Cloud, vernetzte Prozesse in smarten Fabriken – welche Rolle spielt dabei das Zerspanungswerkzeug? Die METAV 2018 in Düsseldorf gibt praxisnahe Beispiele für die wirtschaftliche Umsetzung.
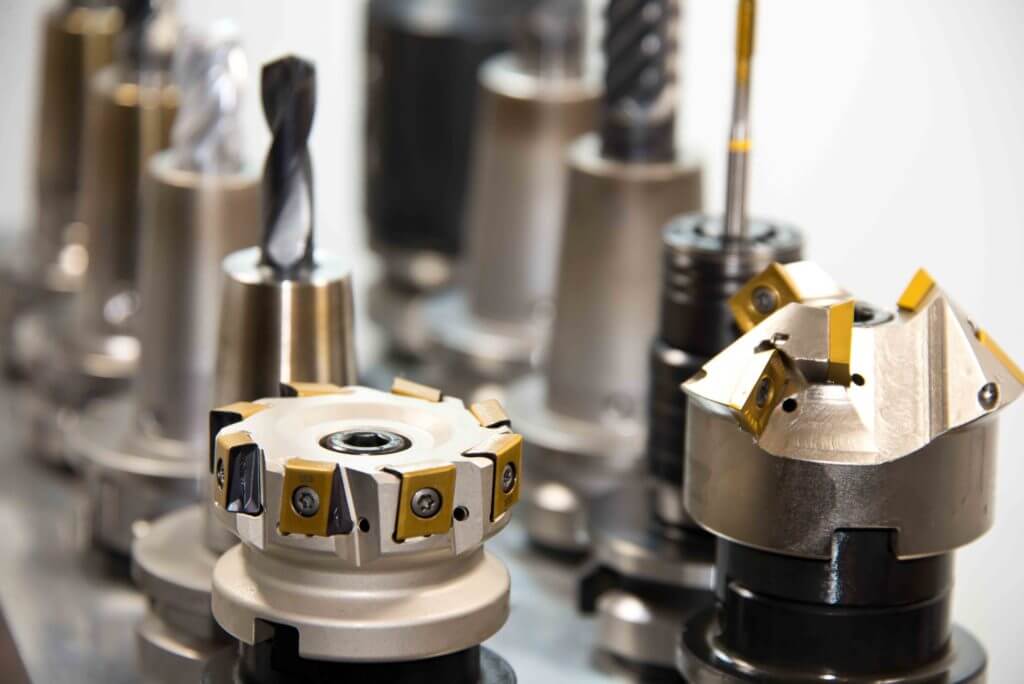
„Wie bei jedem realen Zerspanungsprozess das reale Zerspanungswerkzeug eine wichtige Rolle spielt, so ist für die virtuelle Abbildung von Prozessen das virtuelle Werkzeug entscheidend,“ sagt Claudia Kleinschrodt, wissenschaftliche Mitarbeiterin am Lehrstuhl für Konstruktionslehre und CAD der Universität Bayreuth, die sich dort mit den Problematiken beim CAD-Datenaustausch von Werkzeugmodellen beschäftigt. Dieser digitale Zwilling vereint alle Eigenschaften des realen Werkzeugs und kann dieses durchgängig in allen digitalen Prozessen abbilden.
Simulative Optimierung von Prozessparametern
Eine durchgängige Digitalisierung, erläutert Kleinschrodt, „erlaubt beispielsweise eine virtuelle Inbetriebnahme oder die simulative Optimierung von Prozessparametern. Da es möglich ist, sämtliche Informationen über das Werkzeug zentral abzulegen, kann auf Veränderungen des Werkzeugs während seiner Lebenszeit – etwa durch Nachschleifen – reagiert, die Parameter angepasst und somit eine gleichbleibende Qualität der Produkte gewährleistet werden“. Durch eine Verlagerung vieler zeitintensiver Schritte in die virtuelle Welt können Prozesse zudem wesentlich effizienter gestaltet werden. Die Automatisierung und eine zentrale Planung führen beispielsweise zu geringeren Rüstzeiten, besserer Maschinenauslastung oder optimierten Taktzeiten.
Um einen Überblick über die große Anzahl an verwendeten Werkzeugen in Betrieben zu erhalten, sind effiziente Toolmanagementsysteme (TMS) unabdingbar. Sie stellen eine Voraussetzung für Automatisierung und Vernetzung dar. Ein funktionierender Datenaustausch ist nicht nur wichtig um das TMS mit den benötigten Informationen zu versorgen, sondern ist für jeden digitalen Schritt in der Prozesskette entscheidend. Hierbei stellt neben dem Informationsgehalt vor allem die Kompatibilität zwischen den unterschiedlichsten Systemen eine große Herausforderung dar. Abgestimmte Systeme und qualitativ hochwertige Daten sind also entscheidend für die Umsetzung von effizient digitalisierten Prozessen. Sind diese Bedingungen erfüllt, so Claudia Kleinschrodt, „können Unternehmen stark von einer Digitalisierung ihrer Prozesse profitieren. Vor allem der Mittelstand kann so effizient und flexibel arbeiten und langfristig wettbewerbsfähig bleiben“.
Große Erwartungen hat die Digitalisierungsexpertin an die bevorstehende METAV 2018 in Düsseldorf: „Speziell im Hinblick auf den Datenaustausch und die virtuelle Fertigung interessieren mich vor allem die Entwicklungen im Bereich Smart Factory und die wirtschaftliche Umsetzung der an Forschungseinrichtungen entwickelten Theorien.“
Riesiges Optimierungspotenzial
„Beim Stichwort Industrie 4.0 denkt man meist an digitale Fabriken, ans Internet der Dinge, an Datenspeicherung in der Cloud oder vielleicht auch an robotergestützte Fertigung. Zerspanungswerkzeuge werden in diesem Zusammenhang kaum wahrgenommen,“ sagt Thomas Funk, M. Sc., Mitarbeiter im Technischen Büro der Emuge-Werk Richard Glimpel GmbH & Co. KG, Lauf an der Pegnitz. Für die digitale Fabrik wurde der digitale Zwilling des Zerspanungswerkzeugs geschaffen. Dieser Zwilling, so Funk, „enthält alle notwendigen Informationen, um alle Stationen, die das Werkzeug in der Fabrik durchläuft, virtuell abzubilden“.
Beherrschbar werden die hierdurch entstehenden Datenmengen durch effiziente Toolmanagement Systeme. Im Rahmen der Digitalisierung werden Prozessanalysen versteckte Kosten in immer mehr mittelständischen Unternehmen aufzeigen. Toolmanagementsysteme werden vermehrt Anwendung finden und mit Hilfe des digitalen Zwillings der Werkzeuge die Effizienz der Produktion weiter erhöhen und Arbeitsabläufe optimieren.
„Ich erwarte,“ so Thomas Funk, „dass der Trend der letzten Jahre anhält und die Bedeutung der digitalen Werkzeugdaten weiter steigt. Die Nachfrage nach Daten steigt stetig und deshalb werden wir auf der METAV 2018 in Düsseldorf unter anderem unsere neue Homepageanwendung präsentieren, auf der der digitale Zwilling zu vielen unserer Katalogartikel für unsere Kunden hinterlegt worden ist und kostenlos heruntergeladen werden kann“.
Zerspanungswerkzeuge sind Teil der Prozesskette
Das Zerspanungswerkzeug, erläutert Markus Kannwischer, Leiter Technik und Mitglied der Geschäftsleitung der Paul Horn GmbH, Tübingen, „ist Teil einer Prozesskette und unterliegt im Gegensatz zu fast allen anderen Produktionsmitteln einem Verschleiß. Informationen zum Werkzeug müssen digital vorliegen, um in der Prozesskette verwendet werden zu können. Dies betrifft zum einen alle Informationen zu geometrischen Abmessungen, zum anderen Informationen zum Einsatz des Werkzeugs“.
Informationen zum Verschleiß und zum Einsatz des Werkzeugs sind wichtig für die Prozesssteuerung. Sie können zum einen aus dem Werkzeug selbst generiert werden (Stichwort sensorische Werkzeuge). Hier sendet das Werkzeug selbst Informationen beispielsweise zu Drücken, Temperaturen und Schwingungen. Diese Informationen erlauben Rückschlüsse auf den Zustand und die Belastung der Schneide und zudem auf die Prozessstabilität. Die entsprechenden Zerspanparameter können dann automatisch durch die Steuerung angepasst werden, ähnlich dem autonomen Fahren, bei dem die Geschwindigkeit den Randbedingungen angepasst wird. Zum anderen können Informationen an der Spindel, an der Maschine oder über separate Messvorrichtungen aufgenommen werden, die ebenfalls Rückschlüsse über den Zustand der Schneide erlauben.
Eine Reihe von Forschungsprojekten beschäftigt sich aktuell mit der Frage, wie der Zerspanprozess im Zuge der Digitalisierung „intelligenter“ d.h. verlässlicher gesteuert werden kann: Sollen Standzeiten voll ausgenutzt werden, ist die Betrachtung des Zerspanprozesses für jede einzelne Schneide notwendig? „Wir erwarten,“ sagt Markus Kannwischer, „von der METAV 2018 in Düsseldorf neue Erkenntnisse über den aktuellen Stand dieser Projekte“.
Zum Werkzeug gehören heute Dienstleistungen
Nach Ansicht von Dr. Jochen Kress, Mitglied der Geschäftsleitung der Mapal Dr. Kress KG, Aalen, reicht es heute nicht mehr, das beste Werkzeug zu liefern: „Zum Werkzeug gehören heute Dienstleistungen, wie das Toolmanagement und die korrespondierenden Daten. Wir reagieren darauf unter anderem mit dem Toolmanagement 4.0, das wir auf Basis der Open-Cloud-Plattform c-Com anbieten.“
Bezogen auf das Werkzeug spiele vor allem der digitale Zwilling für die Optimierung der tatsächlichen Bearbeitung eine Rolle. Denn durch ihn ist es möglich, in einer NC-Simulationssoftware den gesamten Bearbeitungszyklus durchzuspielen. So können Kollisionen erkannt und das Werkzeugverhalten getestet werden. Das vermeidet nicht nur, dass kostenintensiver Ausschuss produziert wird, sondern kann in vielen Fällen sogar den Einsatz eines Bauteil-Prototypen ersetzen. Über den Zerspanungsprozess hinaus, erleichtern die richtigen Daten zu den Werkzeugen die gesamten Aufgaben, die während des Lebenszyklus eines Werkzeugs anfallen. Das betrifft von der Auftragserstellung bis zur Entsorgung sämtliche Prozesse, beispielsweise den Einkauf, den Nachschliff der Werkzeuge oder die Maschinenabnahme beim Kunden.
Heute werden in der zerspanenden Fertigung die Prozesse rund um die benötigten Werkzeuge, wie die Beschaffung, Einstellung oder Bereitstellung, mehr und mehr ausgelagert. Jochen Kress: „Wir haben diese Entwicklung früh erkannt und ein effizientes Toolmanagement erarbeitet.“ Nur durch das Teilen von Daten auf einer gemeinsamen Plattform wie c-Com und damit der größtmöglichen Transparenz können angewandte technische Lösungen innerhalb des Unternehmens verglichen werden. Dadurch, do Kress abschließend, „wird die Interaktion zwischen dem Einkauf und der Produktion sowie zwischen dem Einkauf und den Lieferanten vereinfacht“.