Komplexe Fertigungsprozesse für die E-Mobilität sicher beherrschen
Für die automobile Zukunft geht kein Weg mehr an der Elektrifizierung des Antriebsstrangs vorbei. Für die Fertigungsbetriebe gilt es hierbei, sowohl Produkte wie Zahnräder, Getriebe oder Brennstoffzellen ins Visier zu nehmen, als auch die Herstellungsprozesse neu anzugehen.
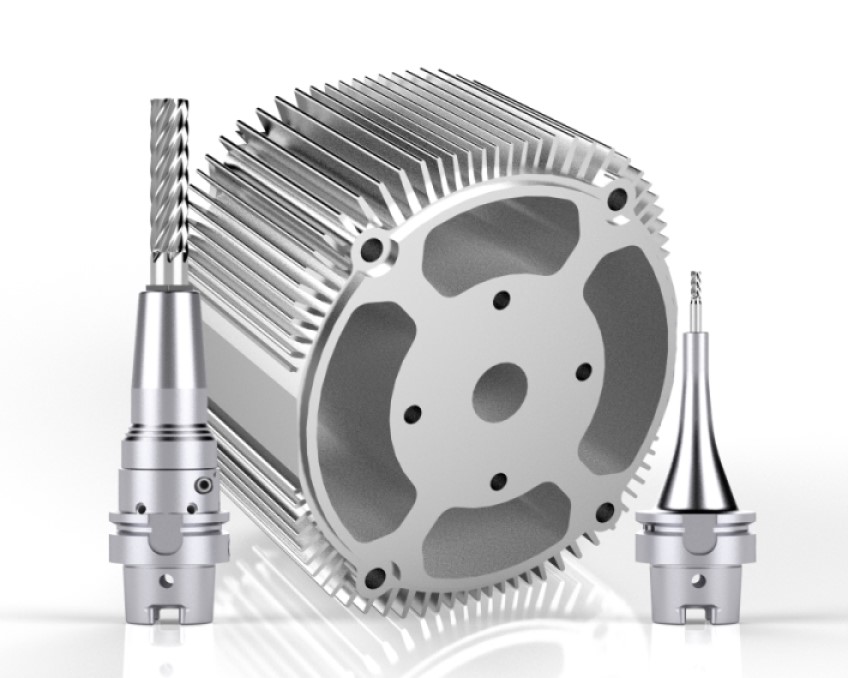
Lösungen auf der METAV 2022 zu sehen
Die 22. Auflage der Internationalen Messe für Technologien der Metallbearbeitung METAV vom 21. bis zum 24. Juni 2022 in Düsseldorf bietet ausgezeichnete Chancen, sich mit Experten auf diesem Fachgebiet auszutauschen.
Neben dem Anspruch, die Herstellungsabläufe prozesssicher und wirtschaftlich auszulegen, stehen Nachhaltigkeit und die Einhaltung der engen Fertigungstoleranzen im Fokus dieses herausforderndes Themenfeldes. Einige METAV-Aussteller befahren diesen Parcours bereits erfolgreich.
Ohne Schwingung zu mehr Standzeit und Sicherheit
Komplexe Bauteile, wie sie in der E-Mobilität zum Einsatz kommen, werden zunehmend auf 5-Achs-Bearbeitungszentren (BAZ) in einer Aufspannung komplett gefräst. Für einen wirtschaftlichen Fertigungsprozess ist vor allem das Zusammenspiel zwischen Werkzeug und Spannfutter entscheidend. Zudem sind häufig hochwertige CAD/CAM-Systeme beteiligt. Damit steigen die Anforderungen an die Bearbeitung weiter. „Wir bieten dafür das passende Werkzeugspannfutter. Es lässt sich ohne jede weitere Vorrichtung von Hand betätigen“, beschreibt Marc Heinrich, Sales Manager bei der Albrecht Präzision GmbH & Co. KG aus Wernau. Das patentierte Spannprinzip sorgt für eine höhere Dämpfung beim Fräsen, was Vibrationen am Werkzeug auf ein Minimum reduziert. So werden die Standzeiten des Werkzeugs verlängert und ergo Kosten reduziert. Das Spannsystem ist lang und schlank gebaut und erhöht damit auf den modernen 5-Achs-BAZ die Zugänglichkeit zum Werkstück. Verschiedene Spannhülsen erlauben zudem unterschiedliche Kühlungsarten – mit Innen- und Peripheriekühlung oder auch mit Coolant 2.0 für noch mehr Kühlleistung. Das Spannfutter deckt einen Spannbereich von 2 bis 20 mm Durchmesser ab und ist für verschiedene Werkstücke einsetzbar. Damit lassen sich Komponenten wie Motoren- und Elektronikgehäuse, Halter für Sensorik oder das Fahrwerk kostengünstig bearbeiten.
Um auch filigrane Teile zu fräsen, hat Albrecht ein Spannfutter mit einem Spannbereich von 1 bis 6 mm im Programm. Es eignet sich etwa für die Bearbeitung kleiner Steuerungsgehäuse oder Sensorhalterungen, die mit einer hohen Feinheit zu bearbeiten sind. Die Süddeutschen bieten das Spannfutter durch die verfügbaren Spannzangen ebenfalls mit Innen- und Peripheriekühlung an. Darüber hinaus zeigt es auch bei hohen Drehzahlen präzise Rundlaufeigenschaften. Auf der METAV 2022 stehen die Experten für Fragen rund um Spannfutter, Vibrationsdämpfung beim Fräsen und erhöhte Werkzeugstandzeiten zur Verfügung.
Prozessstabilität selbst bei engen Fertigungstoleranzen
Die zunehmende Elektrifizierung der Antriebstechnik führt zu Änderungen bei den zu fertigenden Produkten und den Prozessen. Im Vergleich zu Automatikgetrieben für Verbrennungsmotoren lässt sich eine reduzierte Anzahl an schaltbaren Gängen – und somit auch an Zahnrädern – feststellen. Dieser geringeren Anzahl stehen jedoch höhere Anforderungen an die geometrischen Eigenschaften, Fertigungstoleranzen und die Oberflächenbeschaffenheit gegenüber. Insbesondere die Getriebeakustik ist ein wesentliches Qualitätsmerkmal in der Elektromobilität. Für die Herstellung der Zahnräder bedeutet dies erhöhte Anforderungen an die Prozessstabilität bei gleichzeitig engeren Fertigungstoleranzen. Diesen Ansprüchen ist mit entsprechenden Maschinen- und Werkzeugkonzepten (z.B. kombinierten Polierschnecken) oder neuen Prozessen zu begegnen. Dr. Jens Brimmers, Abteilungsleiter Getriebetechnik am Werkzeugmaschinenlabor WZL der RWTH Aachen, sieht wesentliche Neuerungen in der Bearbeitung von Verzahnungen mit Störkonturen insbesondere bei Stufenplaneten (kombinierte Prozesse in einer Aufspannung, reduzierte Werkzeugdurchmesser, etc.), Innenverzahnungen sowie der Bewertung und Vermeidung von Welligkeiten im Submikrometerbereich auf Zahnflanken.
Die Elektrifizierung beeinflusst zudem entscheidend die Bereiche Elektromotoren und Brennstoffzellenfertigung. Leichtbauoptimierte Bauteile müssen nun effizient und prozesssicher hergestellt werden, wie das Umformen von Bipolarplatten für die Brennstoffzellenfertigung zeigt. Ebenso finden neue Werkstoffe Einsatz in breiteren Anwendungsfällen (z.B. Keramiklager), welche eine Anpassung der bisherigen Fertigungsprozesse bedingen. Die veränderten Herausforderungen für die Industrie zeigen gleichzeitig neue Forschungsfelder für die Wissenschaft auf. Prof. Thomas Bergs vom Lehrstuhl für Technologie der Fertigungsverfahren am WZL und sein Team forschen beispielsweise aktiv an Anwendungsfeldern für die Elektromobilität (Getriebe, E-Motor, Brennstoffzelle, Werkzeugbau, etc.). Dabei betrachten die Forschenden der WGP (Wissenschaftliche Gesellschaft für Produktionstechnik), einem Zusammenschluss führender Professoren der Produktionswissenschaft, die Fertigungsprozesse insbesondere auch in Hinblick auf Nachhaltigkeit.
Fertigung von Bipolarplatten für Brennstoffzellen durch HSC-Fräsen
Für elektrische Antriebe kann die benötigte Energie auch in Form von Wasserstoff gespeichert werden. Hierbei kommen Brennstoffzellen zum Einsatz, die chemische Reaktionsenergie in elektrische Energie wandeln. Kernelement sind Bipolarplatten. Sie bilden die beiden elektrischen Pole der Brennstoffzelle und beeinflussen wesentlich deren Wirkungsgrad über die Gestaltung der so genannten Flow-Fields, enge Strömungskanäle, die für eine optimale chemische Reaktion sorgen.
Die Fertigungstechnik muss nun dahingehend befähigt werden, diese Bipolarplatten – typischerweise aus dünnem Stahlblech – zu produzieren. Dies erfolgt über umformende Verfahren mit anspruchsvollen Werkzeugen. Die Formelemente dieser Umformwerkzeuge werden durch HSC-Fräsen hergestellt. Aufgrund der kleinen Radien von wenigen zehntel Millimetern und der hohen benötigen Oberflächengüte, die sehr geringe Zustellungen bedingt, ergeben sich Bearbeitungszeiten von mehreren Dutzend Stunden. Für diese anspruchsvollen Bearbeitungen eignen sich High-Speed-Cutting-Fräsmaschinen der Röders GmbH aus Soltau, da diese aufgrund des ausgefeilten Temperaturmanagements eine besonders hohe Langzeitgenauigkeit erreichen und so selbst bei Bearbeitungszeiten von mehr als 60 Stunden kein Versatz auftritt. Damit wird die benötigte Genauigkeit von +/-3 µm prozesssicher erreicht. Zudem lässt sich eine Oberflächengüte von weniger als Ra 0,1 µm erzielen. Aufgrund der hohen Härte der Umformwerkzeuge ist für die Fertigungskosten neben der Bearbeitungszeit der Werkzeugverschleiß wesentlich. Auf Maschinen von Röders kann dieser aufgrund der hohen Maschinensteifigkeit und -dämpfung sowie der präzisen Bahnplanung signifikant reduziert werden.
Beladedorn für die Imprägnierung von E-Motor-Statoren
Ein Elektromotor besteht im Inneren aus einem Rotor, der sich in einem ruhenden Stator dreht. Er trägt die Drahtwicklung, die als langer dünner Draht auf so genannten Hairpins eng aufgewickelt wird. Fließt hierdurch ein Strom, wird ein Magnetfeld induziert, das den Rotor dreht. Selbst bei engster Wicklung ergeben sich zwischen den Wicklungen jedoch Hohlräume. Ein Imprägnieren des Stators nach dem Wickeln dient dem Schließen dieser Hohlräume und trägt entscheidend zum Wirkungsgrad des E-Motors bei. Da die Imprägnierstoffe nicht nur bei hoher Temperatur aufgebracht werden (zwischen 100 und 200 °C), sondern auch stark abrasiv sind, geschieht ihre Applikation in überwiegend abgeschlossenen Transferstraßen. Zum Handling der Statoren in einer solchen Produktionsanlage hat die Röhm GmbH aus Sontheim einen speziellen Beladedorn entwickelt. Er wird über eine Automatisierungseinrichtung – meist ein Roboter – in den Stator eingeführt und dann von innen gespannt. Jetzt kann der auf dem Beladedorn gespannte Stator in die Transferstraße geführt werden. Um den Beladedorn zu greifen bzw. loszulassen, befindet sich an dessen Ende eine Steilkegel- oder Hohlschachtkegel-Schnittstelle für einen Greifer, der sich pneumatisch oder hydraulisch öffnen und schließen lässt.
„Der Beladedorn ist mit einer zum Patent angemeldeten Selbsthemmung versehen, sodass der Stator nach dem Loslassen des Beladedorns gespannt bleibt“, erläutert Claus Faber, Head of Marketing and Product Management. „In der Transferstraße selbst wird der Beladedorn an seinem anderen Ende von einem Röhm-Spannzangenfutter gespannt. Darin kann der Stator während des Beträufelns oder Tauchens definiert gedreht werden. Auch beim späteren Passungsschleifen ist der auf dem Beladedorn gespannte Stator über das Spannzangenfutter bearbeitbar. Als Aussteller auf der METAV 2022 stehen wir für diese und zahlreiche weitere Themen rund um die Fertigungstechnik gerne persönlich zur Verfügung.“
(Rund 8.900 Zeichen)
Erstellt von daxTR – Technik + Redaktion, Wermelskirchen
Werkzeugspannung von entscheidender Bedeutung
Weltweit stehen Hersteller von Elektrofahrzeugen und ihre Zulieferer unter Druck, die benötigten Komponenten kostengünstig herzustellen. Um auf diesem hart umkämpften Markt wettbewerbsfähig zu bleiben, gilt es deshalb, Fertigungsprozesse effizient zu gestalten. Dabei setzen sie vermehrt auf neue Verfahren, Materialien und Bauteile. Die Themen Digitalisierung und Industrie 4.0 werden immer wichtiger und damit auch eine zunehmende Vernetzung der beteiligten Maschinen sowie neue Maschinentechnologien. Die Anforderungen an die Fertigungstechnik wachsen. Am Ende steht die Frage: Wie lässt sich hohe Qualität kosteneffizient umsetzen? Die Fertigungskette besteht in aller Regel aus der Bearbeitungsmaschine, dem Werkstück, der Aufspannung, dem Werkzeug und nicht zuletzt der Werkzeugspannung. Um ein ausgezeichnetes Ergebnis zu erzielen, müssen alle beteiligten Komponenten optimal aufeinander abgestimmt sein. Das betrifft vor allem Werkzeug und Spannfutter. Die Spannfutter von Albrecht Präzision beispielsweise überzeugen hier unter anderem mit ihren Dämpfungseigenschaften und tragen so zu langen Standzeiten der Werkzeuge sowie sicheren Prozessen bei.
Hintergrund
Die METAV 2022 findet vom 21. bis 24. Juni in Düsseldorf statt. Sie zeigt das komplette Spektrum der Fertigungstechnik. Schwerpunkte sind Werkzeugmaschinen, Werkzeuge, Zubehör, Messtechnik, Oberflächen- und Computertechnik für die Metallbearbeitung, Software, Maschinen und Systeme für die additive Fertigung, Produktionssysteme und Komponenten für die Medizintechnik. Zusätzlich stellt die METAV 2022 in vier Areas spezifische Lösungen zu den Themen Additive Manufacturing, Medical, Moulding und Quality heraus. Die METAV 2020 musste coronabedingt ausfallen und fand 2021 als Digitalveranstaltung statt.
Detaillierte Informationen, Angebote und Anmeldeunterlagen zur METAV 2022 finden Sie im Internet unter www.metav.de.
Besuchen Sie die METAV auch auf den Social Media-Kanälen