Schleiftechnik im Fokus: Aktuelle Trends auf der GrindingHub 2024
Nach der erfolgreichen Premiere der GrindingHub im Mai 2022 fand vom 14. bis 17. Mai 2024 die zweite Auflage des Branchentreffs der Schleiftechnik in Stuttgart statt. Rund 500 namhafte Hersteller aus 31 Ländern präsentierten auf der Messe zahlreiche Neuheiten entlang der gesamten Prozesskette der Schleiftechnik.
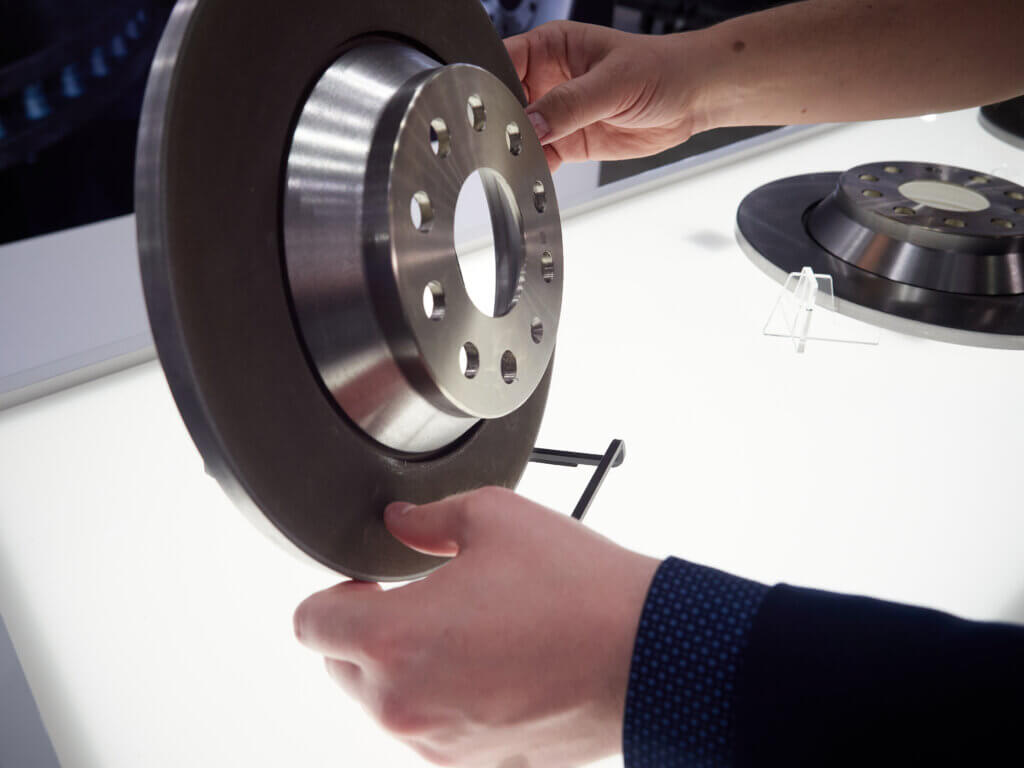
Wie in vielen Industriebereichen zeichnen sich auch in der Schleifbranche die Auswirkungen gegenwärtiger Krisen und struktureller Herausforderungen ab. Vor dem Hintergrund des Kostendrucks und Fachkräftemangels stellten unter anderem die Hersteller von Rund- und Unrundschleifmaschinen, Werkzeugschleifmaschinen für Schneid- und Zerspanwerkzeuge, Flachschleifmaschinen, Schleif-, Polier- und Hohnmitteln sowie Spanntechnik, Filtertechnik und Schleifölen ihre Ansätze zur Ressourcenoptimierung dar. Dabei stand die Reduzierung des Energie- und Rohstoffbedarfs sowie die Abfederung des Fachkräftemangels durch Automatisierung und Digitalisierung im Fokus. Nachfolgend werden einige der Lösungen und technologische Highlights, die auf der GrindingHub präsentiert wurden, vorgestellt.
Neue Schleifmaschinen und -konzepte erhöhen die Variabilität
Die Erwin Junker Maschinenfabrik GmbH aus Nordrach präsentierte auf der GrindingHub erstmals Schleifmaschinen auf Basis der neu entwickelten Plattform 3. Dabei handelt es sich um Schleifmaschinen, die durch verschiedene Konfigurationen flexibel auf ihren Anwendungsfall angepasst werden können. Ein modularer Baukasten erlaubt auf einheitlicher Basis und unter Verwendung möglichst vieler Gleichteile die Realisierung auf verschiedene Anwendungsfälle ausgelegter Schleifmaschinen und -prozesse. Hier sind beispielsweise Hochgeschwindigkeitsschleifmaschinen für die Bearbeitungen mit CBN- und Diamantwerkzeugen oder Schleifmaschinen für konventionelle Korundschleifprozesse zu nennen. Auf diese Weise lässt sich einerseits die Wirtschaftlichkeit erhöhen, anderseits können Durchlauf- und Lieferzeiten reduziert werden. Zusätzlich erhöht sich durch die gestiegene Anzahl an Gleichteilen die Ersatzteilverfügbarkeit. Die Grundlage bildet ein Maschinenbett aus Mineralguss. Darauf aufbauend können verschiedene, an den jeweiligen Anwendungsfall angepasste Tischbaugruppen, Führungen, Werkstückspindel- und Reitstöcke montiert werden. Es können bis zu drei Schleifspindeln eingesetzt werden. Messtechnisch verfügen die Maschinen über ein In-Prozess-Messsystem, das die Werkstückmaße im Prozess misst und davon ausgehend Korrekturdaten berechnet, um Prozesseinflüsse wie Werkzeugverschleiß und Temperaturschwankungen auszugleichen. Eine Besonderheit in dieser Klasse ist dabei der Einsatz eines Absolutmesssystems zum maschineninternen Abrichten. Weiterhin ist bei Schleifmaschinen der Plattform 3 ein integriertes Automatisierungskonzept vorgesehen. Berücksichtigt sind dabei sowohl Ansätze für das manuelle Beladen als auch durch Industrieroboter oder das Beladen durch interne und externe Portallader.
Im Feld der Außenrundschleifbearbeitung zeigte die NSH Group, Chemnitz, auf der GrindingHub ihr neustes Modell Wotan S3A. Dabei handelt es sich um eine kompakte Außenrundschleifmaschine zur Bearbeitung kleiner bis mittelgroßer Werkstücke bis maximal 600 kg und je nach Ausführung einer wählbaren Spitzenweite zwischen 600 und 2.000 mm. Neben einem Maschinenbett aus Granit verfügt die Maschine über zwei CNC-gesteuerte Linearachsen die in z- und x-Richtung hydrostatisch gelagert sind. Sie weisen in Verbindung mit einem Linearantrieb im Vergleich zu Kugelgewindetrieben oder Rollen-Umlaufeinheiten einen reduzierten Verschleiß auf. Je nach Genauigkeitsanforderung kann die Maschine mit einer riemengetriebenen, direktangetriebenen oder hydrostatisch gelagerten Spindel ausgerüstet werden. Weitere Adaptionsmöglichkeiten betreffen die integrierbare Abrichttechnik, Messtechnik und Konfiguration der Schleifeinheit.
Die Rollomatic SA aus der Schweiz präsentierte ihre neue Maschine GrindSmart 630 RS. Dabei handelt es sich um eine 6-achsige Werkzeugschleifmaschine zur Fertigung von Werkzeugen bis zu einer Gesamtlänge von 500 mm in einem Durchmesserbereich von 0,1 bis 20,0 mm und einer Nutlänge von maximal 140 mm. Diese Werkzeuge werden beispielsweise in der Medizintechnik in Form von Knochenbohrern unter Verwendung chirurgischer Roboter eingesetzt. Das Werkzeughandling innerhalb der Maschine erfolgt robotergesteuert. Spindelseitig können verschiedene Konfigurationen mit und ohne Schleifscheibenwechsler realisiert werden. Der Antrieb der Achsen erfolgt über Linearmotoren.
Um Schadstoff- und Feinstaubemissionen zu reduzieren, ist in der Euro7 Norm eine Obergrenze für Feinstaubemissionen von Bremssystem festgelegt. Darauf liegt deshalb ein Fokus aktueller Entwicklungs- und Forschungsvorhaben. Ein Ansatz zur Umsetzung sind hartstoffbeschichtete Bremsscheiben. Sie bieten das Potenzial, den Abrieb um bis zu 90 Prozent zu reduzieren. Allerdings bringt die Hartstoffbeschichtung in Folge einer relativ weichen Matrix mit eingebetteten Karbiden und den unterschiedlichen Zerspanverhalten beider Materialen Herausforderungen bei der Bearbeitung mit sich. Die Prozesskette zur Herstellung hartstoffbeschichteter Bremsscheiben umfasst unter anderem Drehen, Laserbeschichten und Schleifen. Aus diesen Prozessschritten resultieren weitere Einflussfaktoren, die in der Prozessführung des Schleifprozesses berücksichtigt werden müssen. Dies erfordert eine ganzheitliche Betrachtung und Abstimmung der Prozessschritte.
Die Emag-Gruppe aus Salach präsentierte auf der GrindingHub Teile der Bearbeitungskette hartstoffbeschichteter Bremsscheiben wie beispielsweise die VLC 450 DG, eine Spezialmaschine für das Hochpräzisionsschleifen von hartbeschichteten Bremsscheiben. Hier wird doppelseitig geschliffen. Aufgrund seiner hohen Produktivität durch die gleichzeitige Bearbeitung beider Reibringflächen, eines hohen Durchsatzes und kurzer Taktzeiten, wird das Verfahren überwiegend in der Bremsscheibenfertigung eingesetzt. Die dabei senkrecht zur Rotationsachse erzeugten Kreuzschliffstrukturen verbessern das tribologische Einlaufverhalten der Bremsscheiben im Vergleich zu Strukturen in Umfangsrichtung. Die vertikale Spindelanordnung erleichtert den Abtransport der Hartstoffpartikel und ermöglicht gleichzeitig eine gute Zugänglichkeit für Rüst- und Wartungsarbeiten. Das Schleifwerkzeug ist als Wechselring konzipiert, der aufgrund seines geringen Gewichts von unter fünf Kilo eine verhältnismäßig gute Handhabung beim Werkzeugwechsel ermöglicht. Die Maschine verfügt über eine automatisierte Be- und Entladung durch ein Zuführshuttle und einen Werkstücklift. Dies erlaubt die Integration in die Produktionslinie.
Auch viele kleinere Hersteller haben ihre Produkte auf der GrindingHub präsentiert. Beispielhaft sind Avyac Machines aus Veauche (Frankreich) und das schweizerische Start-up G-Elements GmbH zu nennen.
Avyac zeigte ihr 5-Achs-CNC-Bohrer-Schleifzentrum NC18. Dabei handelt es sich um ein vollautomatisiertes, kompaktes Maschinenkonzept zur Fertigung von HSS und VHM-Bohrern im Durchmesserbereich von 1 bis 8 mm, das sich optional auf 14,5 mm erweitern lässt. Die maximale Werkzeuglänge beträgt dabei 320 mm. Ein Kreislader ermöglicht die Bestückung mit bis zu 90 Werkzeugen, die durch einen speziellen Aufbau unter Ausnutzung der Gravitation be- und entladen werden. Es kommen Diamant- oder CBN-Schleifscheiben mit einem Durchmesser von 100 mm zum Einsatz. Der integrierte Messtaster ermöglicht das Antasten der Schneiden und damit die Bestimmung der Schneidposition für Werkzeugnachschleifprozesse.
Neue Softwarelösungen erlauben vereinfachte Prozessgestaltung und -Planung
Neben Werkzeugschleifmaschinen wurden ebenfalls zahlreiche Softwareentwicklungen für die Prozessplanung und -auslegung präsentiert. Ein Beispiel ist die Implementierung von Power Skiving Tools in die SIGSpro Software der Alfred H. Schütte GmbH & Co. KG aus Köln. Dies ermöglicht unter Eingabe der Werkstück-, Schleifscheiben- und Technologiedaten die automatisierte Erzeugung von CNC-Programmen, die an die Maschinensteuerung übertragen und dort abgearbeitet werden können. Wälzschalen beziehungsweise Power Skiving ist ein alternatives Verfahren zur Fertigung von Verzahnungen. Dabei sind die Werkzeug- und Werkstückachse schräg zueinander angeordnet. Infolge der Anstellung des Werkzeugs, eines definierten Axialvorschubs und der gekoppelten Drehzahl von Werkzeug und Werkstück entsteht eine Relativbewegung, wodurch die Zahnlücke entlang der Hauptschnittrichtung aus dem Werkzeug geschält wird. Vorteile des Verfahrens sind die Fertigung von Außen- und Innenverzahnungen, ein kleiner Auslauf und die Fertigung verschiedener Verzahnungen in einer Aufspannung.
Ai-omatic solutions GmbH aus Hamburg und die Tetralytix GmbH aus Hannover, zwei Start-Ups, führten ihre Softwarelösungen zur Optimierung von Produktionsprozessen vor. Die Software Toolyzer von Teralytix erlaubt die Untersuchung und Bewertung beliebiger Werkzeuggeometrien und Zerspanprozesse. Neben Prognosen von Prozesskräften, Moment und Leistung können auch kritische Eingriffsverhältnisse erkannt und die Werkstückqualität vorhergesagt werden. Dies bietet unter anderem das Potenzial, Entwicklungszeiten zu verkürzen und Kosten einzusparen. Eine weitere Möglichkeit beim Fertigungsprozess Ausgaben zu minimieren, ist die Gewährleistung eines stabilen Fertigungsprozesses und die Vermeidung von Maschinenausfällen. Die Firma ai-omatic hat hierfür eine Software entwickelt, die mithilfe von probabilistischen Modellen eine Alternative zu konventionellen Wartungsansätzen darstellen kann. Dazu werden in Echtzeit der Zustand der Maschinen detektiert und auf Grundlage verschiedener integrierbarer Datenquellen Vorhersagen zum Wartungsbedarf der Maschinensysteme getroffen.
Ganzheitliche Betrachtung von Schleifmaschine und Peripherie erlaubt effiziente Prozessführung
Zur produktiven Fertigung hochwertiger Werkstücke ist nicht allein eine fähige Schleifmaschine entscheidend. Die Auslegung eines effizienten und ressourcenoptimierten Schleifprozesses erfordert eine ganzheitliche Betrachtung der Schleifmaschine in Verbindung mit ihrer Peripherie. Bei der Schmierstoffversorgung lässt sich beispielsweise unterscheiden zwischen dem Schmierstoff an sich, entsprechenden Zuführstrategien sowie der Filterung und Wiederaufbereitung von Schmierstoffen nach dem Schleifprozess. Zahlreiche Firmen präsentierten im Rahmen der GrindingHub ihre Produkte aus diesen Bereichen. Hierfür stehen stellvertretend die Oelheld GmbH aus Stuttgart, die Carl Bechem GmbH aus Hagen, die schweizerische Blaser Swisslube AG oder die Knoll Maschinenbau GmbH aus Bad Saulgau.
Eine wichtige Komponente aller Werkzeug- und Schleifmaschinen ist die Spindel. Die Firma GMN aus Nürnberg zeigte beispielsweise ihre neue Spindelreihe UH für Innen- und Außenrundschleifprozesse. Variantenübergreifend zeichnet sie sich durch deutliche Optimierungen entscheidender Leistungsmerkmale aus. So setzt GMN erstmals in einer Serienspindel Synchronmotoren mit einer maximalen Leistung von 32 kW und Drehzahlen bis 120.000 U/min ein. Durch das höhere Drehmoment kommen Synchronmotoren im Vergleich zu Asynchronmotoren bei den meisten Anwendungen mit einem Drittel weniger installierter Leistung aus. Daraus ergeben sich eine bessere Ausnutzung des zu Verfügung stehenden Leistungsbereiches und ein höherer Wirkungsgrad. Aus der gesteigerten Leistungsdichte bei gleichzeitig reduzierter Leistungsaufnahme folgen zudem verschiedene Vorteile bei der konstruktiven Auslegung der Spindel. Größere Achslöcher, Kugellager und Wellendurchmesser führen in Verbindung mit kürzeren Wellen zu einer höheren Laufruhe. Zusätzlich können die aus der besseren dynamischen Steifigkeit und Belastbarkeit resultierenden Potenziale entweder durch größere Werkzeugschnittstellen oder höhere Maximaldrehzahlen ausgenutzt werden. Da sich der Rotor weniger erhitzt, verlagert sich einerseits die Welle thermisch weniger und andererseits wird weniger Kühlung benötigt. Dadurch sinken Luft- und Ölbedarf der Spindel.
Neben der neuen Spindelbaureihe präsentierte GMN auch ihr neues Prelub GPi Plus Schmieraggregat zur Versorgung der Spindel mit Schmierstoff. Es verfügt wie auch die Spindel selbst über die IloT-Technologie „Integrierte Datenerfassung und -auswertung für Spindeln“, kurz IDEA-4S. Im Prozess stellt die Spindel Daten wie Lager- und Kühlmitteltemperatur, Drehzahl sowie Schwingungen und optional Verlagerungen zu Verfügung. Die Maschinensteuerung identifiziert die Spindel anhand ihres digitalen Typenschilds, liest die für die Schmierung relevanten Daten aus und gibt sie an das Schmieraggregat weiter. Dadurch kann die Schmierung der Spindel entsprechend voreingestellter Schmierparameter automatisiert und bedarfsgerecht gesteuert werden. Auf diese Weise kann unter anderem im Falle des Spindelstillstands der Schmierzyklus unterbrochen und Schmierstoff eingespart werden. Zusätzlich werden anhand der vorliegenden Informationen die Entlüftung geregelt und der Ölvorrat selbständig überwacht.
Die zugrunde liegende IloT-Technologie ist ein von GMN entwickeltes Embedded System. Die Sensorik in der Spindel ermittelt kontinuierlich die wichtigsten Prozessparameter, die in Echtzeit bidirektional über IO-Link zur Maschinensteuerung und in die Produktionsnetze gesendet werden. Dies erlaubt eine permanente Optimierung des Einsatzes und kurzfristige Reaktionen auf Fehlentwicklungen. Zusätzlich ermöglicht es die umfassende Optimierung sämtlicher Prozesse und auf diese Weise eine Verbesserung der Effizienz der Komponenten sowie eine Minimierung des Ressourcenverbrauchs.
Neben der Spindelbaureihe UH und der neuen Schmiergerätegeneration Prelub GPi Plus präsentierte GMN auf der GrindingHub das Online-Berechnungstool SpiOnline. Dadurch kann im Vorfeld der Bearbeitung die Auswahl einer optimalen Werkzeug-Spindel-Kombination für den entsprechenden Schleifprozess vorgenommen werden. Es besteht dabei einerseits die Möglichkeit, für eine bestehende Spindel ein optimales Werkzeug zu suchen, und andererseits lässt sich für Anwendungen, die spezielle Werkzeuge erfordern, die passende Spindel ermitteln. Die Auswahl eines optimalen Werkzeugs erlaubt beispielsweise das Erreichen eines bestimmten Drehzahlbereiches und das Erzielen eines optimalen Bearbeitungsergebnisses.
Additive Fertigungsverfahren eröffnen neue Gestaltungsmöglichkeiten von Schleifmitteln
Neben Maschinenkonzepten sowie integrierten Spindel- und Versorgungssystemen ist die Schleifscheibe das entscheidende Element bei Schleifprozessen. Sie ist in direktem Kontakt mit dem Werkstück und beeinflusst das Bearbeitungsergebnis und die Prozessproduktivität in großem Maße. Deshalb werden Entwicklungen im Bereich der Schleifscheiben und deren Vorbereitung auf den Schleifprozess fortlaufend vorangetrieben.
Ein Trendthema ist aktuell die additive Fertigung von Schleifmitteln. Dabei können der Werkzeuggrundkörper, der Schleifkörper oder beides unter Anwendung additiver Fertigungsverfahren erzeugt werden. Additive Fertigungsverfahren erlauben im Vergleich zu konventionellen Fertigungsverfahren eine deutlich größere Gestaltungsfreiheit der erzeugten Bauteile. Im Gegensatz zu Fertigungsverfahren mit geometrisch bestimmter Schneide, bei denen die wirkstellennahe Zufuhr von Kühlschmierstoff durch das Werkzeug möglich ist, ist dies bei Schleifprozessen meist mit großen Herausforderungen verbunden. Hier bieten additive Fertigungsverfahren die Möglichkeit, Schleifscheibensysteme mit innerer Kühlschmierstoffversorgung zu konzipieren.
Auf der GrindingHub präsentierte 3M strukturierte keramische CBN-Schleifscheiben vom Typ 1PVP für Innenrundschleifprozesse. Durch den adaptiven Aufbau von dünnen Schichten entstehen 3D-gedruckte Strukturen. Sie erlauben höhere Gestaltungsfreiheit im Vergleich zu konventionell hergestellten Werkzeugen, da die Grenzen der mechanischen Bearbeitung nicht berücksichtigt werden müssen. Auf diese Weise lassen sich nahezu beliebige dreidimensionale Formen und Strukturen, Schlitze und Kühlschmierstoffbohrungen realisieren. Des Weiteren weisen additiv hergestellte Werkzeuge eine homogene Verteilung von Körnung und Poren auf. Durch die konstruktiven Freiheitsgrade und die damit verbundene spezifische Auslegung auf den jeweiligen Anwendungsfall sowie die materialseitigen Eigenschaften der additiv gefertigten Schleifkörper, lässt sich im Vergleich zu konventionellen Schleifwerkzeugen eine höhere Effizienz und ein verbessertes Leistungspotenzial erzielen.
Ein weiteres Beispiel für aktuelle Entwicklungen zur Herstellung additiv gefertigter Schleifscheibenbeläge zeigte die Firma Riegger Diamantwerkzeuge GmbH aus Affalterbach. Im Rahmen eines geförderten Projekts durch das zentrale Innovationsprogramm Mittelstand (ZIM) des Bundesministeriums für Wirtschaft und Klimaschutz werden Ansätze zur Fertigung von Schleifbelägen für CBN- und Diamantscheiben aus Kunstharz mittels des Digital Light Processing (DLP) entwickelt. Auf Grundlage dieses Verfahrens können individuelle Schleifscheibenprofile erzeugt werden, die in ihrer Dimension lediglich durch die Fähigkeiten des 3D-Druckers beschränkt sind. Vorteile ergeben sich, weil Formteile, der manuelle Aufbau und das Befüllen der Schleifscheibenform entfallen. Dies eröffnet das Potenzial zu Kosteneinsparungen. Gegenwärtige Herausforderungen bestehen beim Erzeugen von homogenen, hoch konzentrierten Schleifbelägen und bei der Hinzugabe von additiven Stoffen zur Optimierung der Bindung.
Neben neuen Konzepten zur Schleifscheibenherstellung ist die Schleifscheibenvorbereitung ein wichtiger Faktor. Durch die Schleifscheibenvorbereitung erhält die Schleifscheibe einerseits ihre finale Kontur, anderseits werden durch das Ausbrechen der Abrasivkörner aus der Bindung neue Schleifkörper freigelegt und so die Basis für die Schleifscheibenwirktopographie geschaffen. Auf der GrindingHub präsentierten zahlreiche Hersteller wie die Firma Cleveland aus Löffingen oder GWD Industrial aus Österreich konventionelle Ansätze zum Abrichten von Schleifscheiben beispielsweise mittels SiC oder Diamantabrichtwerkzeugen. Diese Verfahren zum Abrichten von Schleifwerkzeugen können entweder extern oder maschinenintern durchgeführt werden und erfordern in vielen Fällen einen nachgelagerten Schärfprozess zum Rücksetzen der Bindung und zur Erhöhung der Schnittfreudigkeit der Schleifscheibe.
Ein anderer Ansatz zur Schleifscheibenvorbereitung basiert auf funkenerosiven Verfahren. Bei Schleifbelegen mit leitfähigem Bindungsanteil wird im Lichtbogen die Bindung abgetragen, ohne die nicht leitfähigen Abrasivkörper zu beeinträchtigen. Auf diese Weise entstehen berührungs- und somit kraftlos die Profilgeometrie und Oberflächentopographie der Schleifscheiben. Vorteile dieses Verfahren sind unter anderem die Möglichkeit, mit konventionellen Abrichtverfahren nicht herstellbare Geometrien zu realisieren und einen deutlich erhöhten Kornüberstand zu erzeugen. Damit entsteht eine schnittfreudigere Wirktopographie, durch die höhere Abtragsraten und Schleifscheibenstandzeiten erzielt werden können. Auf der GrindingHub zeigten sowohl der japanische Hersteller Mitsubishi Electric als auch die Firma Häberle aus Laichingen Drahterodiermaschinen zur Vorbereitung von Schleifscheiben mit leitfähigen Bindungssystemen. Häberle führt hierbei auf Basis einer Robocut C400iC Drahterodiermaschine des japanischen Unternehmens Fanuc eine Achserweiterung durch, um so das Rotationserodieren von Schleifscheiben zu ermöglichen. Unter dem Produktnamen Häberle Robocut Plus-Big-R präsentierte Häberle eine Lösung zum automatisierten Abrichten von Schleifscheiben. In Verbindung einer großen Roboterzelle mit dem Fanuc Roboter M20 werden neue Werkstücke vorgehalten und die Häberle Robocut 400 ROT 6-achsig automatisiert be- und entladen. Über eine Rüststation kann die Zelle Hauptzeitparallel mit neuen Werkstücken bestückt werden.
Automatisierung steigert die Produktivität und bietet Antworten auf den Fachkräftemangel
Darüber hinaus zeigten verschiedenste Hersteller zahlreiche weitere Automatisierungsansätze im Rahmen unterschiedlichster Prozesse. So präsentierte Häberle im Rahmen der GrindingHub auch einen Ansatz zur Zuführung von Rohteilen als Schüttgut. Diese werden über ein Förderband unsortiert in den Arbeitsraum eines Roboters geführt. Mithilfe kamerabasierter Systeme wird die Orientierung der Bauteile erfasst, diese Informationen ausgewertet und an den Roboter weitergeben. Auf Basis der Lageinformationen greift sich der Roboter die Bauteile vom Förderband und setzt sie in ihre Spannvorrichtung ein. Um die Position der Bauteile auf dem Förderband zu verändern und dem Roboter das Greifen aller Bauteile zu ermöglichen, führt das Förderband Rüttelbewegungen durch. Weitere mechanische Prozessschritte zur Herstellung einer geeigneten Bauteilorientierung entfallen auf diese Weise.
Am Stand der United Grinding Group aus Bern (Schweiz) wurde unter anderem die „ATP – Automated Tool Production“ – eine Automatisierungslösung für zylindrische Präzisionswerkzeuge – der Walter Maschinenbau GmbH aus Tübingen vorgestellt. Sie besteht aus mindestens einer von vorne zugänglichen Roboterzelle für das automatische Be- und Entladen der Maschinen sowie mindestens einem autonomen, mobilen Roboter zum Transport der Werkzeugpaletten oder Einzelteile zwischen den Bearbeitungs- und Lagerstationen. Das System ist in bestehende Anlagenlayouts integrierbar und eignet sich für alle Schleif-, Mess- und Erodiermaschinen von Walter. Zusätzlich kann es als Schnittstelle zu Maschinen anderer Hersteller dienen. Der Transportroboter entnimmt an der Übergabestation der jeweiligen Maschine die Palette oder das Einzelteil und befördert diese zum entsprechenden Zielort. Hierfür kommt ein Leitsystem für die übergeordnete Daten- und Prozesssteuerung sowie ein standardisiertes Kommunikationsmodell zum Einsatz.
Derartige Automatisierungslösungen sind ein Ansatz, dem Fachkräftemangel zu begegnen und die Produktivität zu erhöhen. Gerade in Bereichen des Werkstückhandlings innerhalb der Bearbeitungsmaschine, des Be- und Entladens von Maschinen sowie deren Bestückung bietet die Automatisierung von Prozessen das Potential, Fertigungsprozesse unabhängiger von den zur Verfügung stehenden Arbeitskräften aufrechtzuerhalten und zu skalieren.
Leistungsfähige Zerspanwerkzeuge dank Kanten- und Oberflächenmodifikation
Die Kanten- und Oberflächenmodifikation ist ein bedeutender Arbeitsschritt in der Herstellung von Werkzeugen mit geometrisch bestimmter Schneide. Gründe für derartige Modifikationen sind vielfältig, haben aber hauptsächlich die Verbesserung des Einsatzverhaltens und die Erhöhung der Standzeit der Zerspanwerkzeuge zum Ziel. Unterschieden wird unter anderem zwischen Verfahren zur Schneidkantenpräparation und zur Oberflächenmodifikation von Funktionsflächen. Eine Funktionsflächenmodifikation führt man häufig nach einem Schleifprozess zur Verbesserung der Schichthaftung für den Beschichtungsprozess oder nach dem Beschichtungsprozesses im Rahmen einer Schichtnachbehandlung durch. Eine Schichtnachbehandlung nimmt man vor, um Oberflächenfehler wie beispielsweise Droplets zu reduzieren und so die Oberflächenqualität zu verbessern. Die Oberflächenqualität der Spanflächen kann insbesondere bei Bohr- oder Tiefbohrprozessen die Spanabfuhr und damit die Prozesssicherheit sowie Standzeit beeinflussen. Eine Präparation der Schneidkanten wird häufig in Form einer Verrundung vorgenommen. Dies dient dazu, mögliche Defekte im Bereich der schliffscharfen Kanten zu reduzieren und die Kantenstabilität zu erhöhen. Damit lässt sich das Verschleißverhalten der Werkzeuge positiv beeinflussen und die Standzeit erhöhen.
Ein Ansatz für die Oberflächenbearbeitung und Schneidkantenpräparation ist die Anwendung von Gleitschleifprozessen. Ein neues Verfahren ist die Technologie des Stream Finishings. Rotierende Werkstücke werden in einen sich drehenden, mit Schleif- oder Poliermittel gefüllten Behälter abgesenkt. Diese Verfahren bieten den Vorteil, dass auch kleine Geometrien vollständig bearbeitet werden können. Auf Grundlage dieser Technologie zeigte der australische Hersteller Anca auf der GrindingHub seine neue Stream-Finishing-EPX-SF. Dabei handelt es sich um eine Maschine zur Schneidkantenpräparation und Oberflächenmodifikation, welche sich in automatisierte Zellen integrieren lässt. Sie verfügt über drei Spindeln und elf Achsen und ist in der Lage, die Kantenrauheit auf weniger als 100 nm zu reduzieren und die Kantenradien mit kontrollierbarem K-Faktor auf wenige Mikrometer anzupassen. Die Automatisierung ermöglicht in Verbindung mit dem vollautomatischen Ladesystem, dass bis zu 1.800 Werkzeuge pro Tag präpariert und modifiziert werden können. Zusätzlich ist die Maschine mit einer Werkzeugreinigungsstation und Prozessüberwachungssystemen ausgestattet. Dies soll durch eine fortlaufende Anpassung des Medienpegels eine gleichbleibende Qualität der Werkzeuge gewährleisten.
Neben diesem neuen Verfahren wurden auch konventionelle Methoden zur Schneidkantenverrundung wie das Bürsten gezeigt. Die schweizerische Firma Dynamic Finishing zeigt eine Lösung zur industriellen Erzeugung von definierten Schneidkantengestalten und -oberflächen, die in die Schleifmaschine integriert werden kann. Der Bürstprozess wird auf der Schleifmaschine umgesetzt.
Einen anderen Ansatz verfolgt die Firma GDS aus Ofterdingen. Hier wird ein robotergesteuerter Bürstprozess zu gezielten Schneidkantenverrundung von Schaftwerkzeugen und Wendeschneidplatten vorgestellt. Dabei handelt es sich um eine Roboterzelle mit dem Namen Magicedge. Grundsätzlich wird ein Roboter genutzt, um das Werkzeug gezielt zu bürsten. Die Roboterkinematik beeinflusst die Form, die Größe und den Verlauf der Schneidkantenverrundung. Im Gegensatz zum Gleitschleifen lassen sich bei Bürstprozessen die Schneidkanten und die schneidkantennahen Bereiche präparieren, ohne fernere Bereich zu beeinflussen. In der Roboterzelle lassen sich weitere kundenspezifische Anforderungen wie Pick and Place, Glasperlenstrahlen, Qualitätssicherung und Polieren realisieren.
Ein ähnliches Verfahren präsentierte die Firma Nagel aus Nürtingen in Zusammenarbeit mit Bruker Alicona aus Österreich unter dem Namen NaPrep. Auch hier wird ein Werkzeug roboterbasiert präpariert. Die selektive Präparation der einzelnen Kanten erfolgt mittels beschichteter Bearbeitungsbürsten. Daran angeschlossen ist eine optionale Polierbearbeitung. Der automatisierte Prozess ermöglicht einerseits aufgrund eines Greiferbahnhofs Flexibilität hinsichtlich der Werkzeugtypen und anderseits einen mannlosen Betrieb der Anlage. Durch die Integration eines Messsystems ist die In-Prozess-Vermessung der Werkzeuge möglich, was eine selbstregelnde Prozessparameteranpassung – einen Closed Loop – erlaubt. Die messtechnische Erfassung der Schneidkantengestalt erfolgt dabei durch einen EdgeMaster von Bruker Alicona. Dabei handelt es sich um ein optisches Messmittel, das auf Basis der Fokusvariation und in Verbindung mit einer entsprechenden Auswertesoftware die Erfassung und Vermessung von Schneidkanten und deren Gestalten erlaubt.
Gezielte Prozess- und Bauteilkontrolle durch geeignete messtechnische Systeme
Zur Erfassung und Beurteilung des Bearbeitungsresultats von Fertigungsprozessen sind In-Prozess- und Nach-Prozess-Messungen erforderlich. Hierzu kommen neben Messtechnik zur Erfassung der Prozesskräfte oder des Prozessverhaltens insbesondere Messsysteme zur Bestimmung von Maß, Lage und Form sowie zur Analyse der Oberflächenbeschaffenheit zum Einsatz.
Neben dem Konzept zur Schneidkantenpräparation, stellte Bruker Alicona auf der GrindingHub sein neues optisches Messgerät FocusX vor. Die berührungslose Messung optischer Messgeräte ist einer der maßgeblichen Vorteile gegenüber taktilen Messgeräten, da sie sich auch zur Analyse empfindlicher Bauteile eignet. So ist beispielsweise bei Bauteilen aus der Medizintechnik eine Veränderung der Oberfläche durch das Messverfahren auszuschließen. FocusX nutzt die Advanced-Focus-Variation, die erstmals mit dem optischen Messgerät µCMM eingeführt wurde. Diese ist einerseits schneller als die Vorgängertechnologie der Fokus-Variation, anderseits besonders gut für glatte Oberflächen geeignet. Es lassen sich aber auch komplexe Formen, kleine Radien, spitze Winkel und steile Flanken bis hin zu Bohrungen mit einem Durchmesser-Tiefen-Verhältnis von 1:3 bis 1:10 erfassen. Durch Dreh- und Kippachsen können Bauteile aus verschiedenen Blickwinkeln gemessen und durch eine entsprechende Softwareintegration zu einem 3D-Bild zusammengesetzt werden. Des Weiteren lassen sich ISO-konforme Rauheitsmessungen durchführen.
Externe Messsysteme bieten im Vergleich zu maschineninternen Messystemen verschiedene Vorteile. Beispielsweise können eine hauptzeitparallele Nutzung oder kontrollierte Messbedingungen einfacher realisiert werden. In vielen Fällen kann aber auch eine Messung auf der Bearbeitungsmaschine ein zielführender Ansatz sein. Ein Beispiel hierfür ist der Laser Contour Check, den Walter in seine Schleif- und Erodiermaschinen integriert. Damit lassen sich diverse Werkzeugparameter an zylindrischen Werkzeugen berührungslos messen und falls nötig eine automatische Korrektur des Werkzeugdurchmessers und des Werkzeugprofils im Prozess umsetzen.
Sonderausstellungsbereiche ermöglichen Vernetzung zwischen Forschung und Wissenschaft, Startups und der Industrie
Im GrindingSolutionPark präsentierten verschiedene Forschungsinstitute aus der Produktionstechnik die Ergebnisse aktueller Forschungsprojekte. Beispielhaft dafür stehen zwei Projekte des Manufacturing Technology Institute (MIT) aus Aachen. Im Rahmen eines Forschungsvorhabens zur „Analyse der tribologischen Verhältnisse beim Schleifen von polykristallinem Diamant (PKD) mit einem wassergemischten Kühlschmierstoff“ werden durch verschiedenste Einsatzversuche Parameter ermittelt, die zur Entwicklung von mathematischen Reibgesetzen für den Einkorn- und Mehrkornkontakt sowie zur numerischen Simulation des thermo-mechanischen Belastungskollektivs herangezogen werden. In einem nachfolgenden Schritt wird daraus ein Erklärungsmodell für die Schleifbearbeitung von PKD mit einem wassergemischten Kühlschmierstoff abgeleitet. Das zweite Vorhaben fokussiert „Untersuchungen der thermo-mechanisch-chemischen Belastungen beim Außenrund-Umfangs-Querschleifen von 100Cr6“. Dieser Werkstoff wird häufig in Wälzlagern eingesetzt, welche aufgrund des Wandels hin zur Elektromobilität steigenden Anforderungen unterliegen. Auf Grundlage der Untersuchungen soll eine gezielte Prozessführung des Schleifprozesses die Bildung einer initialen Grenzschicht auf den Lagerflächen unterstützen. So sollen der Verschleißschutz erhöht und der bisher erforderliche Umfang des Einlaufvorgangs zur Bildung einer additivinduzierten Verschleißschutzschicht reduziert werden. Das Institut für Fertigungstechnik und Werkzeugmaschinen (IFW) aus Hannover präsentierte „Analysemethoden in der Schleifwerkzeugherstellung“. Hierbei werden im Bereich der Bindungs-, Korn- und Porencharakterisierung beispielsweise Biegeversuche, Härtemessungen, Phasenanalysen, Dichtemessungen, Oberflächentopographieaufnahmen, Einzelkornritz- und Scherversuche sowie rasterelektronenmikroskopische Untersuchungen vorgenommen. Das Vorhaben „In-situ assessment of residual stress state in gear grinding process: An Artificial Intelligence Approach“ des IWF aus Berlin beschreibt einen Ansatz zur Bewertung von Eigenspannungen im Bauteil auf Grundlage von Methoden der Industrie 4.0. Dazu werden Schleifprozesse mit prozessbegleitender Messtechnik durchgeführt und anschließend Eigenspannungsmessung vorgenommen. Diese Daten dienen als Eingangsgrößen eines KI-Netzwerks. Auf diese Weise sollen in nachfolgenden Schleifprozessen Vorhersagen über den Eigenspannungszustand getroffen werden können, ohne erneute Eigenspannungsmessungen vornehmen zu müssen. Das Institut für Spanende Fertigung (ISF), Dortmund, stellte aktuelle „Schleiftechnologische Entwicklungen in der additiv-subtraktiven Prozesskette“ vor. Hierbei werden die Möglichkeiten der häufig notwendigen Nachbearbeitung additiv gedruckter Bauteile durch Schleifen, Microfinishen und Nassstrahlspanen thematisiert sowie Ansätze zur gezielten Prozessführung der jeweiligen Verfahren für die Nachbearbeitung additiv gedruckter Bauteile entwickelt.
Auf dem Startup Hub zeigten junge Unternehmen ihre Kompetenzen und Leistungen. Weber Technologies aus Potsdam stellte Diamantbeschichtungen von Hartmetall-Präzisionswerkzeugen vor. WT-DIA Diamantbeschichtungen werden für die Bearbeitung unterschiedlicher Werkstoffe wie CFK, GFK, CFK/ Al-Sandwichmaterial, Keramiken, Grafit und Al-Legierungswerkstoffe eingesetzt und verbessern potenziell das Einsatzverhalten der Werkzeuge. Beschichtet wird im Heißdraht CVD-Verfahren. Hierbei werden Prozessgase im Vakuum in die Beschichtungskammer eingeleitet und unter hoher Temperatur zersetzt. Freiwerdende Kohlenstoffatome lagern sich auf der Substratoberfläche an, sodass eine kristalline Diamantschicht während des Beschichtungsprozesses aufwächst. Die Schicht kann im mikro- und nanokristallinen Bereich sowie mit einer gradierten Struktur in einer Dicke von 3 bis 20 µm aufgebaut werden.
Mit Innovationen aktuellen Herausforderungen begegnen
Zur GrindingHub 2024 standen insbesondere die Automatisierung und Digitalisierung von Fertigungsprozessen im Fokus. Sie können der gegenwärtigen Fachkräftemangel entgegenwirken und die Produktivität erhöhen. Im Spannungsfeld zwischen Fachkräftemangel, Kostendruck sowie nachhaltigen Prozessen und Produkten wurden zahlreiche Detailverbesserungen zur Steigerung der Effizienz verschiedener Komponenten, deren Peripherie und der eingesetzten Schleifwerkzeuge gezeigt. Beispielhaft hierfür stehen additiv gedruckte Schleifwerkzeuge und Effizienzsteigerungen in der Spindeltechnik.
Im Kontext der Mobilitätswende hin zur emissionsneutralen Mobilität kommen schleiftechnischen Verfahren große Bedeutung zu. Neben neuen Antriebskonzepten werden auch emissionsreduzierte Bremssysteme und deren Fertigung fokussiert. Die schleiftechnische Bearbeitung hartstoffbeschichteter Bremsscheiben ist ein wachsender Sektor, der umfassende Innovationen bei Schleifmaschinen, Schleifwerkzeugen und in der Prozessführung erfordert.
Autor: Ulf Hensler, M.Sc., Institut für Spanende Fertigung, Technische Universität Dortmund, E-Mail ulf.hensler@tu-dortmund.de
Downloads
Bilder
Bild 1 Advanced-Focus-Variation ermöglicht auch die optische Messung stark spiegelnder Oberflächen.
Bild 2 Erhöhte Effizienz durch neue Generationen der Spindeltechnik und Maschinenperipherie.
Bild 3 Die Herstellung hartstoffbeschichteter Bremsscheiben erfordert innovative Lösungsansätze in der Prozesskette.
Bild 4 Erweiterte Gestaltungsmöglichkeiten und erhöhtes Leistungspotential von Schleifmitteln durch additive Fertigung.
Bild 5 Automatisierungsansätze bieten das Potential die Produktivität zu erhöhen und dem Fachkräftemangel zu begegnen.
Bild 6 Softwarelösungen ermöglichen effizientere Fertigung komplexer Zerspanwerkzeuge.