Internationales METAV-Presseforum zu Gast bei Phoenix Contact- Kommunikation ist der Schlüssel
Vom 20. bis 24. Februar 2018 ist die METAV in Düsseldorf Schauplatz für moderne Technologien, Dienstleistungen und Trends der Metallbearbeitung. Neben Exponaten und Themen entlang der Wertschöpfungskette, geht es auf so genannten Areas um Lösungen etwa aus dem Bereich Werkzeug- und Formenbau oder um Zukunftstechnologien wie Additive Manufacturing und Industrie 4.0. Um die auf der METAV erlebbare Verbindung von klassischer Metallbearbeitung und innovativen Entwicklungen zu beleuchten, lud der Veranstalter der METAV, der Verein Deutscher Werkzeugmaschinenfabriken (VDW) zu einem internationalen Presseforum ins westfälische Blomberg (zwischen Paderborn und Bielefeld) ein. Bei Gastgeber Phoenix Contact standen neben den Themen „Digitale Prozessketten im Werkzeugbau“ und „Additive Fertigung“ vor allem Strategien für Industrie 4.0 im Mittelpunkt der Diskussion.
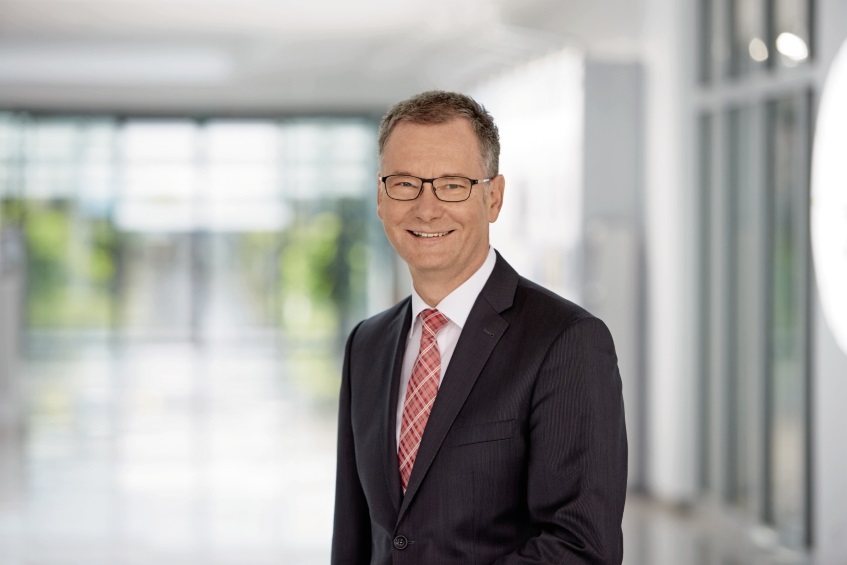
Das Produktionsspektrum von Phoenix Contact umfasst Komponenten, Systeme und Lösungen im Bereich der Elektrotechnik, Elektronik und Automatisierung. Das traditionsreiche Familienunternehmen, 1923 als Ein-Mann-Betrieb für den Handel von Fahrdrahtklemmen für elektrische Straßenbahnen gegründet, darf beispielhaft für die wachsende Bedeutung der Verbindungs- und Automatisierungstechnik stehen. Heute beschäftigt das Unternehmen weltweit rund 15.000 Mitarbeiter. Zur Phoenix Contact-Gruppe gehören 12 Unternehmen in Deutschland sowie mehr als 50 eigene Vertriebsgesellschaften und 40 Vertretungen in Europa und Übersee. Einer, der selbst rund 30 Jahre dieser Entwicklung miterlebt und mit gestaltet hat, ist Roland Bent, Corporate Technology Officer bei Phoenix Contact. „Die Automatisierung hat die industrielle Entwicklung wesentlich beschleunigt“, sagt er. „Doch dies wird künftig bei weitem übertroffen von der Geschwindigkeit, mit der sich die industrielle Welt jetzt, im Zeitalter der Digitalisierung, verändern wird.“ Bent sieht die Industrie in der Phase, „in der wir miteinander und voneinander lernen“. Doch jedes Unternehmen stehe grundsätzlich vor der Entscheidung, „die digitale Transformation einfach auf sich zukommen zu lassen oder sie aktiv mit zu gestalten“.
Digitalisierung der Wertschöpfungskette
Bei Phoenix Contact sind die Weichen gestellt. Industrie 4.0 hat für das Unternehmen hohe Priorität mit zwei wesentlichen Aspekten: Zum einen geht es um smarte Technologien für die eigene Produktion, die mit eigenem Maschinenbau und hoher Fertigungstiefe ein exzellentes Terrain für die durchgängige Nutzung digitaler Daten bietet. Zum anderen entwickeln die westfälischen Spezialisten in „kooperativen Konzeptionen“ innovative Automatisierungsprodukte für die Produktionsanlagen von Kunden. Über allem steht eine „digitale Agenda“, die auf der Digitalisierung der Wertschöpfungskette aufbaut: „Nur wer ein virtuelles Abbild seiner Produktionsergebnisse bereitstellt, kann zukünftig in diese Kette liefern“, ist Roland Bent überzeugt.
Auf dem METAV-Presseforum erläuterte Frank Knafla, Master Specialist Industry 4.0 bei Phoenix Contact, die Bedeutung des Internets für diese Entwicklung: „Die Nutzung des Internets als Kommunikationssystem in industriellen Anwendungen eröffnet völlig neue Möglichkeiten für die Organisation und Steuerung der gesamten Wertschöpfungskette entlang des Lebenszyklus von Produkten und Produktionssystemen“, so Knafla. Die Kombination der Industrial-Ethernet-Kommunikation und des Internets, damit die direkte Verbindung von Dingen, Diensten, Menschen und Maschinen, ermögliche smarte Anwendungen in neuer Dimension. Doch träfen hier auch unterschiedliche Welten aufeinander, die erst lernen müssten, miteinander zu kommunizieren. „Kommunikation ist der Schlüssel“, sagt Knafla.
Profinet und die Cloud
Auf externe Rechnerinfrastrukturen in der Cloud zugreifen zu können, ermöglicht die Verarbeitung riesiger Datenmengen, wie sie künftig entlang der Wertschöpfungskette erfasst werden. Proficloud heißt das Zauberwort, das bei Phoenix Contact für professionelle, ganzheitliche Cloud-Lösungen für die Automatisierung steht. Wie Knafla erläutert, kommunizieren hier dezentrale Systeme auf Basis des bekannten Profinet (Process Field Network)-Standards „direkt und sicher über das Internet“. Dafür werden an beliebigen Standorten Cloud-Steuerungen installiert, die sich über das Internet mit der Proficloud verbinden. Am lokalen Standort erscheinen die dezentralen Cloud-Steuerungen wie lokale Profinet-Teilnehmer, das heißt, völlig transparent und ohne weitere Konfiguration oder zusätzliche Programmierung. Bei der Proficloud von Phoenix Contact sei die Datensicherheit dank TLS (Transport Layer Security)-Verschlüsselung sichergestellt. Alle Informationen, die die Cloud liefert, können direkt in die Feldebene kommuniziert werden. So lassen sich etwa ERP-Auftragsdaten direkt aus der Proficloud über das Profinet-Protokoll in die Produktionsanlage am eigenen Standort übertragen. Neben der professionellen Cloud-Lösung bietet Phoenix Contact die zugehörige Kommunikationstechnik für robuste und sichere Netzwerke, einschließlich WLAN, für den Maschinenbau.
Einstieg über praxisorientierte Handlungsfelder
Da die Vorteile von Industrie 4.0 für die Produktion gerade mittelständischen Unternehmen mitunter etwas abstrakt erscheinen, hat Phoenix Contact praxisorientierte Handlungsfelder definiert. „Dabei wird nicht alles realisiert, was technisch möglich ist“, erläutert Frank Knafla, „sondern nur, was für den jeweiligen Prozess einen Vorteil garantiert“. Aspekte wie Qualität, Flexibilität, Leistungsfähigkeit und Wirtschaftlichkeit stehen im Vordergrund.
Um die Vorteile digitaler Daten etwa im Werkzeug- und Formenbau zu nutzen, müssen zunächst alle Prozessphasen innerhalb des Wertschöpfungsnetzwerks mit einer einheitlichen digitalen Beschreibung unterstützt werden. Jedem physikalischen Produkt werden digitale Daten zugeordnet. Mit der entsprechenden Technik, die von schweren Steckverbindern und Stromversorgungen mit individueller Parametrierung, über Markierungssysteme und individuelle Designlösungen für Embedded Systems reicht, schafft Phoenix Contact die zugehörige Infrastruktur. So lassen sich projektbezogene Informationen etwa zu Kosten und Materialart im Spritzguss erheben und daraus die richtigen Entscheidungen für die Produktion von Kunststoffteilen treffen.
Unverzichtbar in der komplexen vernetzten Industrie sind dabei elektrische Verbindungen und die dauerhafte, eindeutige Kennzeichnung aller Komponenten. Da schnelles und fehlerfreies Verdrahten kostbare Zeit im Installationsprozess gewinnen und den Rüstaufwand modularer Anlagen minimieren kann, entwickelte Phoenix Contact die Push-In Anschlusstechnik. Dezentrale Teilnehmer und Schaltschränke lassen sich so schnell und ohne Werkzeug verdrahten. Leiter werden gesteckt, ohne direkten Kontakt zu stromführenden Teilen. Zur Push-In-Produktpalette gehören etwa Reihenklemmen, Geräteschutzschalter, Steckverbinder und Verteilerblöcke.
Losgröße eins zu Kosten der Massenfertigung
Mit seinem Produktportfolio, den Diensten und Lösungen will Phoenix Contact die Voraussetzungen schaffen, damit sich zunehmend individuellere Endprodukte vollautomatisiert bis zur Losgröße eins fertigen lassen. Wie dies aussehen kann, demonstriert das Unternehmen am Beispiel einer eigenen Fertigungslinie, bei der Produktion von Trennverstärkern am Standort Bad Pyrmont. Trennverstärker, so die Erläuterung des Unternehmens, werden in elektrotechnischen Anlagen immer dann benötigt, wenn sensible Messwertsignale störungsfrei von der Sensor- in die Steuerungsebene übertragen werden sollen. Da sich hier bisweilen sehr individuelle Anforderungen ergeben, stellen die Automatisierungsspezialisten die Trennverstärker als konfigurierbare Varianten in flexiblen Produktionsanlagen her. Die Kommunikation zwischen Produkt, Mitarbeiter und Maschine führe zu einem verbesserten Prozessablauf, heißt es, in dem sich selbst geringe Losgrößen wirtschaftlich produzieren lassen. Von der Auftragserstellung bis zum fertigen Produkt nutzen alle beteiligten Systeme digitale Daten.
Zur Verdeutlichung lässt sich die Entstehung eines Trennverstärkers so beschreiben: Eine SMD (Surface Mount Device – oberflächenmontiertes Bauelement) – bestückte Leiterplatte, auf der sich bis zu 154 Komponenten befinden können, läuft auf der Produktionslinie durch Stanze und Laserbeschriftung bis zur „Hochzeit“ mit dem Gehäuse. Nachdem das Produkt mit der Firmware programmiert wurde, folgt ein elektrischer Test, bevor es zum Versand geht. Vom ersten Schritt an stellt ein RFID-Tag die Verbindung zu den Informationen her, die das übergeordnete System liefert. Dazu gehört etwa die Angabe, welche Prüfungen am Gerät durchzuführen sind und welche Firmware implementiert werden muss. Aufgrund des Tags kennt das übergeordnete System den aktuellen Bearbeitungszustand des einzelnen Moduls. Auf dem Bildschirm sieht der Mitarbeiter die Informationen, die er für seine Aufgabe benötigt. Dank der Kommunikation zwischen Produkt und Anlage könne der Mitarbeiter die Komplexität, die sich aus der Variantenvielfalt ergibt, jederzeit beherrschen.
Tatsächlich beginnt die Entstehungsgeschichte des Produkts aber viel früher: Der Anwender wählt mithilfe eines Web-Konfigurators das für ihn am besten geeignete Gerät und legt dann die individuelle Konfiguration fest. Der nach seinen Vorstellungen nun produzierte Trennverstärker wird ohne Aufpreis selbst in Losgröße 1 geliefert. Doch damit nicht genug. Verändern sich die Bedingungen später in der Fabrik, etwa weil die Anlage erweitert wird, kann der Trennverstärker an die neuen Anforderungen adaptiert werden. Der Anwender definiert die neuen Parameter über eine App oder PC-Software und überträgt sie per NFC (Near Field Communication) oder Bluetooth an das Gerät. Informationen zu den Geräten bleiben erhalten, sodass jede Konfiguration nachbestellt werden kann. Die eindeutige Identifizierung des jeweiligen Moduls erlaubt zudem das Abrufen des zugehörigen Kalibrier-Zertifikats.
Vernetzung und Kooperation für neue Geschäftsmodelle
Unabhängig von den technischen Voraussetzungen für Industrie 4.0, die bei Phoenix Contact auf dem METAV-Presseforum dargestellt wurden, liegen die Herausforderungen der Zukunft darin, aus den technischen Möglichkeiten neue Geschäftsmodelle zu entwickeln. Hier kommt dem Austausch mit anderen Playern sowie gemeinsamen Forschungsprojekten auch mit Wissenschaftsinstitutionen eine immens hohe Bedeutung zu. Bei Phoenix Contact werden zugleich die mit der Digitalisierung verbundenen Auswirkungen auf die Arbeitswelt erforscht. Gemeinsam mit der Hochschule Ostwestfalen-Lippe wurde im Unternehmen die „Zukunftswerkstatt Combicon“ entworfen, in der Veränderungen von Tätigkeitsinhalten und Qualifikationen untersucht werden.
Industrie 4.0 live auf der METAV
Mit dem industriellen „Internet der Dinge“, also der Zusammenführung von Maschinen- und Sensordaten mit der virtuellen Welt, dürfte die klassische Fabrik- und Prozessautomation deutlich Fahrt aufnehmen, das wurde beim METAV-Presseforum deutlich. In Düsseldorf wird der „Themenpark Industrie 4.0“, der sich bereits bei seiner Premiere vor zwei Jahren als Besuchermagnet auf der METAV erwiesen hat, das Thema aufgreifen und Einblicke in die digitale Fertigung ermöglichen. Hier soll auch die Frage beantwortet werden, wie kleine und mittelständische Unternehmen von der digitalen Fertigung profitieren können. Am Gemeinschaftsstand präsentieren Unternehmen und Forschungseinrichtungen bereits realisierte Problemlösungen. Das zugehörige Fachforum soll Best-Practice-Beispiele darstellen und für weiteren Gesprächsstoff sorgen. Die Stände der Aussteller bieten ausreichend Gelegenheit zum Informationsaustausch, ganz nach dem Motto: Kommunikation ist der Schlüssel – für Innovationen ebenso wie für die weitere digitale Entwicklung.